Lost wax casting is a critical manufacturing process in the aerospace industry. It enables the production of highly complex and precise components that meet the stringent requirements of aerospace applications. Optimization of lost wax casting processes is essential to enhance the performance, reliability, and efficiency of aerospace parts. This article explores the latest techniques and strategies for optimizing lost wax casting processes for aerospace applications.
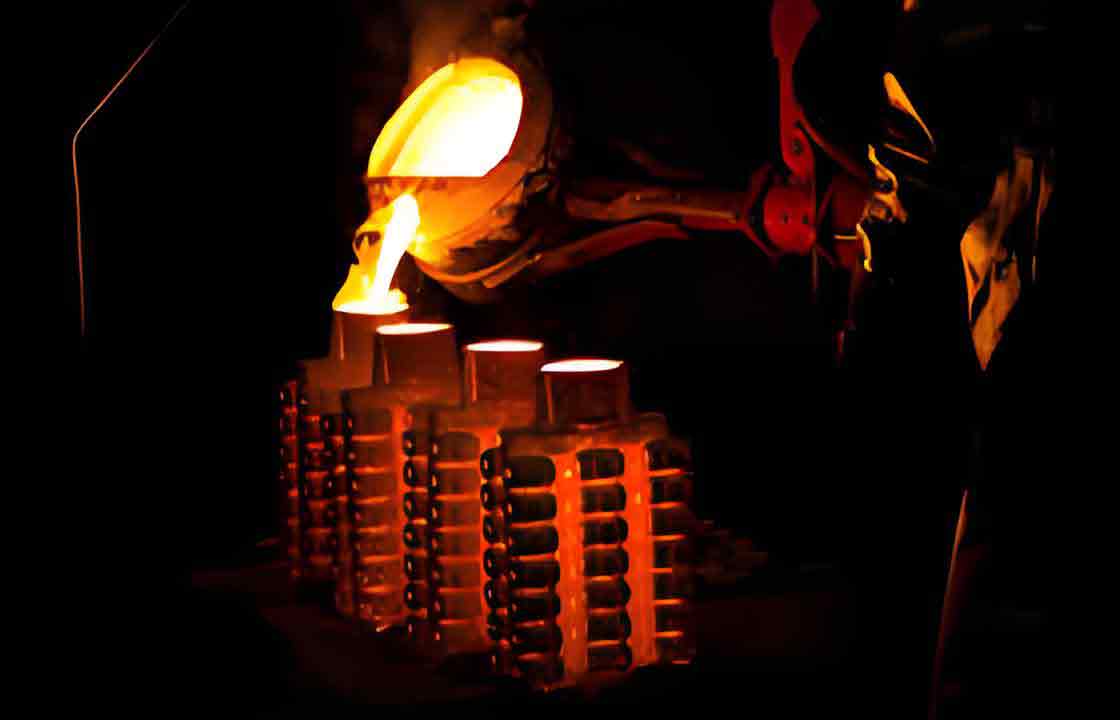
Introduction
The aerospace industry demands components that exhibit exceptional strength, lightweight properties, and the ability to withstand extreme conditions. Lost wax casting is ideally suited for producing such components due to its ability to create intricate shapes with high dimensional accuracy. Optimizing this process involves advancements in materials, pattern creation, mold construction, casting techniques, and quality control measures.
Key Areas of Optimization
- Pattern Creation and Design:
- 3D Printing of Wax Patterns: Leveraging additive manufacturing to produce highly detailed and accurate wax patterns, which reduces the need for manual intervention and improves repeatability.
- Design for Manufacturability (DFM): Implementing design principles that simplify the casting process, minimize defects, and enhance the performance of the final components.
- Material Selection:
- High-Performance Alloys: Utilizing alloys such as nickel-based superalloys and titanium alloys that offer superior mechanical properties, high-temperature resistance, and corrosion resistance.
- Material Characterization: Conducting thorough material testing and analysis to ensure optimal alloy composition and properties for specific aerospace applications.
- Ceramic Shell Construction:
- Advanced Ceramic Materials: Using stronger and more heat-resistant ceramics to construct molds capable of withstanding the high temperatures and stresses of casting aerospace components.
- Precision Shell Building Techniques: Implementing multi-layer shell construction and controlled drying processes to enhance mold stability and reduce the risk of cracking or deformation.
- Casting Techniques:
- Vacuum Casting: Utilizing vacuum environments to reduce gas entrapment, improve metal flow, and enhance the overall quality of the cast parts.
- Directional Solidification: Controlling the solidification process to align grain structures, which improves the mechanical properties and performance of the cast components.
- Quality Control and Inspection:
- Non-Destructive Testing (NDT): Employing X-ray, ultrasonic testing, and CT scanning to inspect the internal structure of cast parts and detect any defects without causing damage.
- Process Simulation: Using advanced simulation tools to model the casting process, predict potential issues, and optimize parameters for better quality and efficiency.
Impact on Aerospace Applications
Optimizing lost wax casting processes has a significant impact on the performance and reliability of aerospace components. The following benefits are particularly noteworthy:
- Enhanced Component Performance:
- Improved Mechanical Properties: Optimized casting techniques and materials result in components with superior strength, toughness, and fatigue resistance.
- High-Temperature Capability: High-performance alloys and advanced ceramic molds enable components to operate effectively in extreme temperature environments.
- Increased Reliability:
- Reduced Defects: Precision pattern creation, advanced ceramic shells, and rigorous quality control measures minimize the occurrence of casting defects, enhancing component reliability.
- Consistent Quality: Automated processes and real-time monitoring ensure consistent quality across production batches, reducing variability and improving overall reliability.
- Cost and Time Efficiency:
- Reduced Lead Times: Rapid prototyping with 3D printing and streamlined casting processes accelerate production timelines.
- Lower Production Costs: Near-net shape casting minimizes material waste and reduces the need for extensive machining, lowering overall production costs.
Table: Key Optimization Strategies for Lost Wax Casting in Aerospace
Optimization Area | Techniques and Innovations | Benefits |
---|---|---|
Pattern Creation | 3D printing, Design for Manufacturability (DFM) | High accuracy, reduced defects, faster prototyping |
Material Selection | High-performance alloys, material characterization | Superior properties, tailored performance |
Ceramic Shell Construction | Advanced ceramics, multi-layer shell building | Enhanced mold stability, high-temperature resistance |
Casting Techniques | Vacuum casting, directional solidification | Improved metal flow, better mechanical properties |
Quality Control | Non-destructive testing, process simulation | Defect detection, optimized casting process |
Case Study: Optimization of Turbine Blades for Jet Engines
Background: A leading aerospace manufacturer aimed to optimize the production of turbine blades for jet engines. The goal was to enhance the blades’ performance, durability, and efficiency while reducing production costs and lead times.
Approach:
- Pattern Creation:
- Used 3D printing to produce highly detailed wax patterns with complex internal cooling channels.
- Applied Design for Manufacturability principles to simplify the casting process and minimize defects.
- Material Selection:
- Selected a nickel-based superalloy known for its high-temperature strength and resistance to oxidation and corrosion.
- Conducted extensive material testing to ensure the alloy’s suitability for the demanding operating conditions of jet engines.
- Ceramic Shell Construction:
- Utilized advanced ceramic materials to build molds that could withstand the high temperatures and stresses of casting the superalloy.
- Implemented multi-layer shell construction to enhance mold stability and reduce the risk of cracking during casting.
- Casting Techniques:
- Employed vacuum casting to minimize gas entrapment and improve the quality of the cast blades.
- Used directional solidification to align grain structures, enhancing the blades’ mechanical properties and performance.
- Quality Control:
- Conducted non-destructive testing, including X-ray and CT scanning, to inspect the internal structure of the cast blades and detect any defects.
- Used simulation software to model the casting process, predict potential issues, and optimize parameters for better quality and efficiency.
Results:
- Achieved turbine blades with superior mechanical properties and high-temperature capability, improving engine performance and efficiency.
- Reduced lead times and production costs through rapid prototyping, streamlined processes, and minimized material waste.
- Enhanced reliability and consistency of the blades, reducing the occurrence of defects and improving overall engine reliability.
Conclusion
Optimizing lost wax casting processes is crucial for producing high-performance, reliable, and efficient components for aerospace applications. By leveraging advancements in pattern creation, material selection, ceramic shell construction, casting techniques, and quality control, manufacturers can achieve significant improvements in the performance and reliability of aerospace parts. These optimizations not only enhance the mechanical properties and durability of the components but also reduce production costs and lead times, contributing to the overall efficiency and competitiveness of the aerospace industry. As technology continues to advance, further innovations in lost wax casting will undoubtedly play a pivotal role in the future of aerospace manufacturing.