Key problems and solutions to be solved by the large-scale casting composite squeeze casting forming equipment. According to the analysis results, the overall structure scheme applicable to the large-scale casting composite squeeze casting forming equipment is shown in the figure.
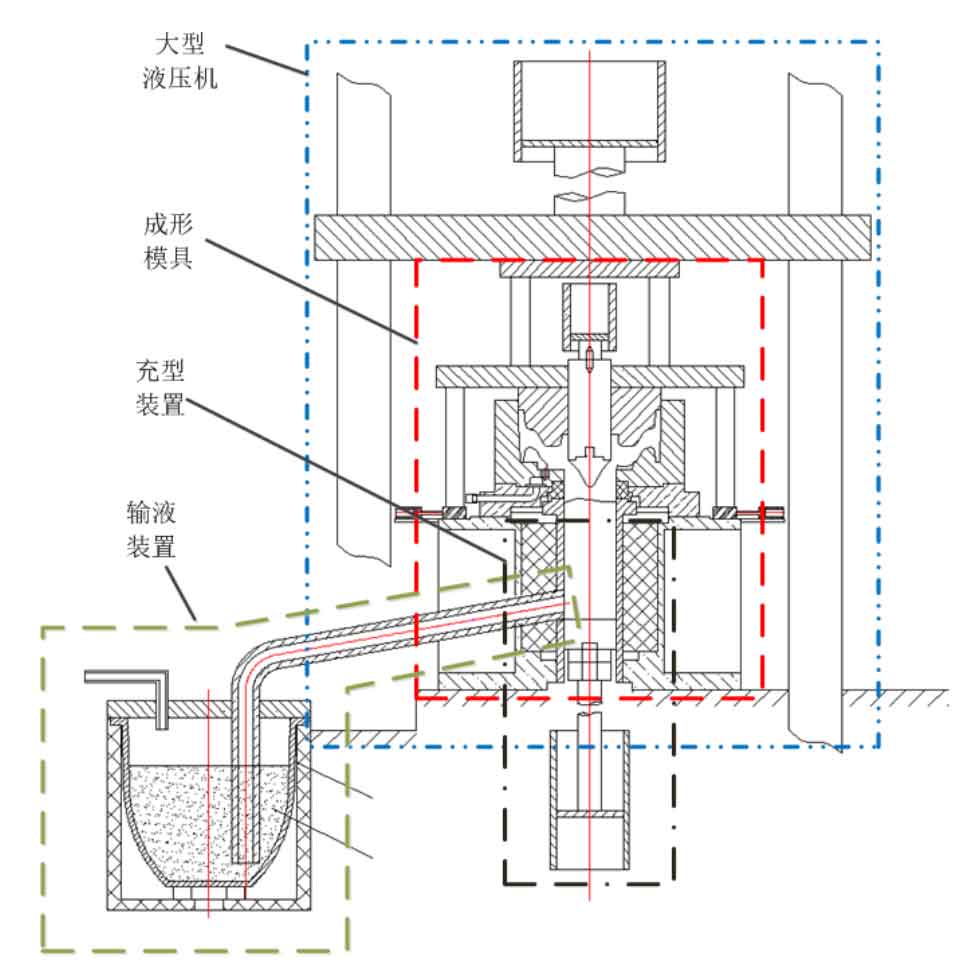
The structure scheme mainly includes a large hydraulic press, a forming die, a mold filling device and an infusion device. The infusion device transmits the molten liquid to the mold filling device, and then the molten liquid is introduced into the mold cavity by the mold filling device, and then the large-scale hydraulic press provides the basic pressure requirements for metal molten liquid forming to ensure that the metal molten liquid solidifies and forms under pressure.
The composite squeeze casting forming equipment must first realize the pre closing of the mold, and the relative positions of the upper mold and the lower mold during pre closing must be accurately controlled. The implementation methods are as follows:
(1) Set up independent pre closing mechanism for positioning, such as crankshaft connecting rod mechanism, but this method requires additional mechanism and control equipment;
(2) The pre closing type is realized through the accurate positioning of the movable cross beam of the hydraulic press. Since the movable cross beam of the large hydraulic press will naturally fall under the action of its own weight, to ensure that the position of the movable cross beam remains unchanged during the whole mold filling process, cushion blocks must be set to support the movable cross beam. For different pre closing amounts, different cushion block heights need to be set, and auxiliary hydraulic cylinders need to be set when unlocking, If manual unlocking is used, the movable crossbeam needs to go up first to release the clamping force;
(3) It is realized by innovating the mold structure.
Finally, the third method is adopted. See Chapter 4 for details. The molten metal in the mold cavity must be extruded quickly and effectively. Due to the large extrusion pressure required by large castings, under the existing production technology conditions of large-scale hydraulic presses, the development of larger hydraulic presses or the addition of hydraulic energy storage devices to hydraulic presses can solve some problems, but it will take a long time and cost. In addition to developing hydraulic press with larger forming pressure, it is an economical and effective way to increase the forming pressure by improving the structure of the die.
The composite squeeze casting forming equipment needs to provide effective power to ensure that the metal melt is smoothly transported to the mold filling cavity in the closed pipe. When the melt in the mold filling cavity reaches the predetermined volume, the remaining melt in the closed pipe must flow back to the holding furnace. At the same time, the metal melt in the mold filling cavity needs to be sent to the mold cavity at an appropriate speed. Therefore, the implementation of the composite squeeze casting process must have an independent infusion device and mold filling device.