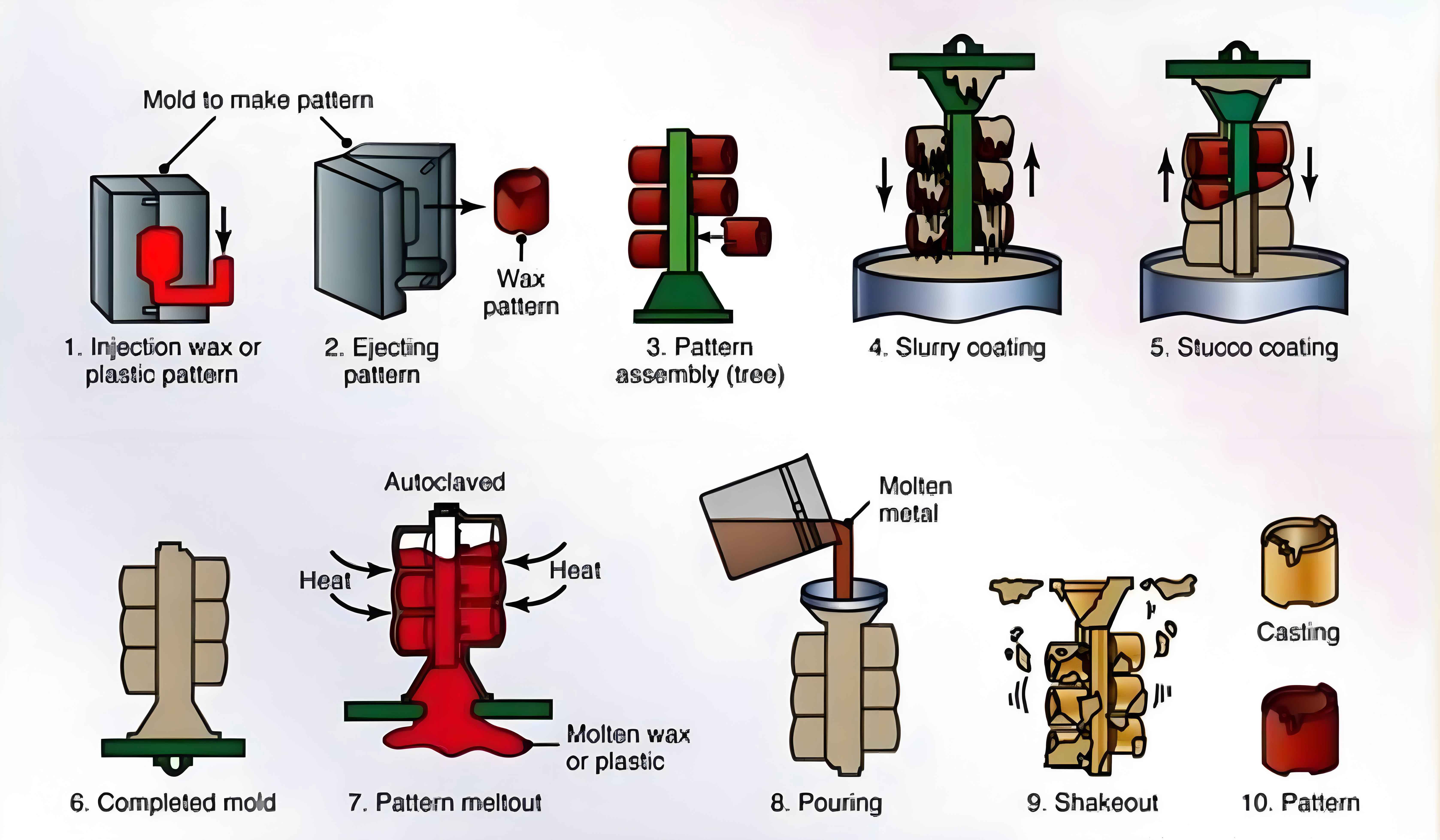
Introduction
Investment casting, despite its many advantages, can encounter challenges such as porosity and surface defects, which can compromise the integrity and performance of the final product. Addressing these issues is crucial to maintaining high quality and reliability in cast components. This analysis explores the common causes of porosity and surface defects in investment casting and provides solutions to minimize these issues.
Common Challenges in Investment Casting
- Porosity:
- Types: Includes gas porosity, shrinkage porosity, and micro-porosity.
- Causes: Can arise from trapped gases, solidification shrinkage, or inadequate mold filling.
- Surface Defects:
- Types: Includes rough surfaces, inclusions, and cracks.
- Causes: Can result from poor mold material quality, improper mold handling, or suboptimal investment casting parameters.
Solutions for Minimizing Porosity
- Improved Mold Ventilation:
- Solution: Ensure proper ventilation in the mold to allow gases to escape. This can be achieved by designing vents and risers strategically.
- Benefit: Reduces gas porosity by allowing trapped air and gases to exit the mold during pouring.
- Control of Pouring Temperature:
- Solution: Maintain optimal pouring temperatures to ensure proper mold filling and solidification.
- Benefit: Reduces the risk of shrinkage porosity by ensuring consistent and controlled cooling rates.
- Degassing of Molten Metal:
- Solution: Use degassing techniques, such as vacuum degassing or inert gas purging, to remove dissolved gases from the molten metal.
- Benefit: Minimizes gas porosity by reducing the amount of gas that can form bubbles during solidification.
- Use of Grain Refiners:
- Solution: Add grain refiners to the molten metal to promote uniform grain structure.
- Benefit: Reduces micro-porosity by improving the overall solidification structure and reducing segregation.
- Optimal Mold Design:
- Solution: Design molds with proper gating systems to ensure smooth metal flow and minimize turbulence.
- Benefit: Reduces the likelihood of trapped air and shrinkage defects by promoting even and controlled filling.
Solutions for Minimizing Surface Defects
- High-Quality Mold Materials:
- Solution: Use high-quality refractory materials for molds to ensure a smooth surface finish.
- Benefit: Reduces surface roughness and the occurrence of inclusions from mold material.
- Proper Mold Handling:
- Solution: Handle molds carefully to avoid damage and contamination.
- Benefit: Minimizes the risk of cracks and inclusions caused by mishandling or contamination.
- Optimized Wax Pattern Production:
- Solution: Use high-quality wax and precise pattern-making techniques to create accurate and smooth wax patterns.
- Benefit: Ensures that the final cast component has a smooth surface and accurate dimensions.
- Controlled Shell Building Process:
- Solution: Carefully control the ceramic shell building process, including drying times and layer application.
- Benefit: Prevents surface defects caused by uneven shell layers or improper drying.
- Post-Casting Surface Treatments:
- Solution: Apply post-casting surface treatments such as shot blasting, polishing, or chemical etching to improve surface finish.
- Benefit: Enhances the surface quality and removes minor surface imperfections.
- Regular Maintenance and Calibration of Equipment:
- Solution: Conduct regular maintenance and calibration of investment casting equipment to ensure optimal performance.
- Benefit: Prevents defects caused by equipment malfunction or misalignment.
Advanced Techniques and Innovations
- Computational Modeling and Simulation:
- Solution: Use computational fluid dynamics (CFD) and finite element analysis (FEA) to simulate the investment casting process and predict potential defects.
- Benefit: Allows for optimization of mold design and investment casting parameters to minimize defects before actual production.
- In-Situ Monitoring:
- Solution: Implement in-situ monitoring techniques using sensors and real-time data analysis during the investment casting process.
- Benefit: Enables immediate detection and correction of issues, reducing the occurrence of defects.
- Additive Manufacturing for Mold Creation:
- Solution: Use 3D printing to create precise and complex molds directly from digital designs.
- Benefit: Enhances mold accuracy and reduces the risk of defects associated with traditional mold-making techniques.
Conclusion
Investment casting offers significant advantages for producing complex geometries and high-precision components, but challenges such as porosity and surface defects can impact the quality of the final product. By implementing solutions such as improved mold ventilation, control of pouring temperatures, degassing techniques, and high-quality mold materials, these challenges can be effectively minimized. Advanced techniques like computational modeling, in-situ monitoring, and additive manufacturing further enhance the ability to produce defect-free cast components. Continuous innovation and meticulous process control are key to overcoming these challenges and ensuring the reliability and performance of investment-cast parts.