To meet the application requirements of advanced aviation engines for complex shell castings of high-strength and heat-resistant aluminum alloys, this study compared and analyzed the process and mechanical properties of a new type of Al-Si-Cu-Mg-Sc high-strength and heat-resistant aluminum alloy with ZL101A and ZL205A cast aluminum alloys. The metal casting process design and experimental verification of the complex casing of the oil pump were carried out using the high-strength and heat-resistant aluminum alloy, and the quality of the casting products was evaluated. The results showed that the new high-strength and heat-resistant Al-Si-Cu-Mg-Sc alloy had better casting fluidity and hot cracking resistance than the ZL205A high-strength cast aluminum alloy, and the qualification rate of the complex shell of its metal casting oil pump was comparable to that of the same type of shell ZL101A. The average tensile strengths at room temperature of the separated test bar of casting and test specimen from casting itself of the new alloy were both above 420 MPa, significantly higher than that of ZL101A alloy, and its tensile strength at 250 °C was superior to ZL205A alloy. The surface quality, internal quality, airtightness, and pressure-resistant performance of the casting case all met the design requirements of the product.
1. Introduction
1.1 Application Requirements of Aviation Engine Oil Pump Housing Castings
Aviation engine oil pump housing castings have complex shapes and intricate internal oil passages, which can only be fabricated by casting methods. These castings are required to have high pressure-bearing strength and airtightness, demanding extremely high quality. Therefore, the selected casting materials must not only possess high strength but also have good casting process performance. With the continuous improvement of aviation engine performance, the working medium and environmental temperature of the oil pump housing are also increasing, posing higher requirements for the strength and heat resistance of the castings.
1.2 Limitations of Conventional Casting Aluminum Alloys
ZL101A aluminum alloy, commonly used at present, has excellent casting processability and is suitable for producing complex structural housings with high metallurgical quality requirements. However, its material strength decreases rapidly with increasing temperature, making it difficult to meet the application requirements of new-generation aviation engines. ZL205A aluminum alloy has the highest tensile strength among current casting aluminum alloys, and its mechanical properties can reach the levels of some ferrous metals and forged aluminum alloys. It is often used to manufacture complex components that bear large loads and have high yield strengths. However, it has disadvantages such as a large hot cracking tendency, a tendency for porosity, and poor casting fluidity, making it difficult to apply the metal casting process and meet the requirements of high pressure-bearing strength and no oil leakage or air leakage under high-pressure conditions.
1.3 Advantages and Research Significance of Al-Si-Cu-Mg-Sc High-Strength and Heat-Resistant Aluminum Alloy
Al-Si casting alloys are widely used in the aerospace field due to their excellent casting properties and low thermal expansion coefficients. Traditional high-strength Al-Si casting alloys mainly include the Al-Si-Mg and Al-Si-Cu systems. The alloys in these two systems mainly use β′-Mg₂Si and θ′-Al₂Cu as the main precipitation strengthening phases, respectively. However, the β′ phase is prone to coarsening at a high temperature of 150 °C, and the θ′ phase has relatively low thermal stability at temperatures above 200 °C. Studies have shown that adding Cu and Mg elements in a certain proportion and trace amounts of Sc, Ti, Zr, and other elements can simultaneously improve the room-temperature and high-temperature mechanical properties of the alloy. The addition of a trace amount of Sc element can not only form a highly thermally stable Al₃Sc nano-precipitation phase but also improve the thermal stability of θ′-Al₂Cu, thereby significantly improving the high-temperature mechanical properties of the aluminum alloy. This work evaluated the casting and mechanical properties of a new type of Al-Si-Cu-Mg-Sc high-strength and heat-resistant casting aluminum alloy and studied the casting process of typical complex shell castings based on the characteristics of the alloy and detected the quality of the castings.
2. Experimental Materials and Methods
2.1 Experimental Materials
The nominal composition of the new heat-resistant aluminum alloy used in the experiment was Al-7Si-4Cu-0.35Mg-0.15Sc (mass fraction/%). The actual chemical composition of the alloy measured by a direct-reading spectrometer is shown in Table 1.
Si | Cu | Mg | Sc | Al |
---|---|---|---|---|
7.1 | 3.8 | 0.32 | 0.13 | Bal. |
2.2 Experimental Methods
2.2.1 Alloy Preparation
300 kg of furnace charge was prepared using pure aluminum Al (>99.70%), pure magnesium Mg (>99.8%), AlCu50 master alloy, AlSi12 master alloy, and AlSc2 master alloy according to the actual composition of the alloy in Table 1. The alloy was heated in a resistance melting and holding furnace. After the pure aluminum was melted, AlSi12, AlCu50, and AlSc2 were added in turn. After the alloy was completely melted, it was stirred thoroughly, and then pure magnesium was added. The alloy was held at 720 °C, and high-purity argon gas was introduced at a rotation speed of 400 r/min for 10 min of rotary degassing. After standing at 740 °C for 20 min, casting was performed.
2.2.2 Casting Process
The casting process of the aviation engine oil pump housing involved preheating the metal mold to 300 °C and using tilting casting with a pouring time of 11 s. Ten castings were poured, and metal mold single-cast tensile test bars were poured simultaneously. The sample size was 12 mm in diameter and 60 mm in gauge length. After casting, the castings were cut to remove the gating and riser systems, and then subjected to solution treatment at 495 °C for 24 h and aging heat treatment at 180 °C for 8 h (T6), followed by sandblasting and inspection.
2.2.3 Testing and Analysis
The complex housing was inspected according to the detection requirements specified in HB 963-2005. The metallographic structure of the alloy was observed using a Primotech Mat optical microscope (OM). The microstructure of the T6-treated alloy was observed using a SU3800 scanning electron microscope (SEM). The precipitates in the T6-treated alloy were characterized using a FEI Tecnai F20 transmission electron microscope (TEM). The room-temperature and high-temperature mechanical properties of the single-cast samples and samples taken from the complex housing were tested using an EUT5105 electronic universal testing machine at a tensile strain rate of 5 × 10⁻⁴ s⁻¹.
3. Experimental Results and Analysis
3.1 Casting Properties of the New Heat-Resistant Aluminum Alloy
3.1.1 Fluidity
The casting fluidity of the new Al-Si-Cu-Mg-Sc heat-resistant casting aluminum alloy was 400 mm. The fluidity of the ZL101A alloy was greater than 420 mm, and that of the ZL205A alloy was 245 mm (consistent with the description in the literature). It can be seen that the fluidity of the new heat-resistant aluminum alloy was significantly better than that of the ZL205A alloy but lower than that of the ZL101A alloy.
3.1.2 Hot Cracking Tendency
The hot cracking tendency test results of the casting aluminum alloy ring specimens are shown in Figure 1. It is generally believed that the narrower the width of the ring specimen when the first hot crack occurs, the better the hot cracking resistance of the alloy. As shown in Figure 1(a), the new heat-resistant aluminum alloy did not experience hot cracking at a width of 7.5 mm but cracked at a width of 5.0 mm. Under the same process parameters, the ZL205A alloy cracked at a width of 25.0 mm, and two hot cracks were observed at a width of 15.5 mm (Figure 1(b)). No hot cracks were observed in the ring specimen of the ZL101A alloy (Figure 1(c)), indicating that the hot cracking tendency of the new heat-resistant aluminum alloy was lower than that of the ZL205A alloy but higher than that of the ZL101A alloy.
Figure 1 | Test Results of Hot Tearing Susceptibility of Circular Specimens |
---|---|
(a) | Al-Si-Cu-Mg-Sc heat-resistant cast alloy |
(b) | ZL205A alloy |
(c) | ZL101A alloy |
3.1.3 Solidification Characteristics
The solidification process of the new heat-resistant casting aluminum alloy, ZL205A alloy, and the commonly used ZL101A alloy in aviation engines was simulated and analyzed using the thermodynamic calculation software Scheil solidification model. Figure 2 shows the variation of the solid-phase volume fraction with temperature during the solidification process of the three alloys. The ZL101A alloy, with a high Si content, had a liquidus temperature of 612 °C, a solidus temperature of 567 °C, and a solidification crystallization temperature range of 45 °C. The alloy had good casting fluidity, resulting in a low tendency for casting porosity. The ZL205A alloy had a liquidus temperature of 650 °C, a solidus temperature of 558 °C, and a solidification crystallization temperature range of 92 °C. The casting exhibited a mushy solidification mode and was prone to porosity defects. The new heat-resistant casting aluminum alloy in this study had the same Si content as the ZL101A alloy and a higher Cu content. Its liquidus temperature (600 °C) was lower than that of the ZL101A and ZL205A alloys, and the solidus temperature decreased to 522 °C. It can be seen that the solidification crystallization temperature range (78 °C) of the new heat-resistant casting aluminum alloy was lower than that of the ZL205A alloy, and its liquidus temperature was significantly lower than that of the ZL205 alloy. During solidification, it had a larger degree of superheat, so its fluidity was better than that of the ZL205A high-strength casting aluminum alloy.
Figure 2 | Variation of Solid Phase Volume Fraction with Temperature during Solidification Process of Three Types of Cast Aluminum Alloys |
---|
The formation of hot cracks in casting aluminum alloys is closely related to the amount of remaining liquid phase at the end of solidification and is affected by the chemical composition of the alloy. When the amount of remaining liquid phase is insufficient to compensate for the solidification shrinkage between dendrites, intergranular separation occurs, resulting in hot cracks. Li et al. proposed multiple theoretical models to evaluate the hot cracking tendency of alloys. Kou considered the effects of shrinkage, growth, and feeding in the mushy zone at the end of solidification and proposed using the value of |dT/dfs¹/²| when the square root of the solid-phase volume fraction (fs¹/²) was around 1 as the hot cracking evaluation index. Since the lower growth rate between adjacent grains slows down the connection of cracks and the longer intergranular channels hinder the inhibition of cracks by liquid-phase feeding, a higher value of |dT/dfs¹/²| indicates a greater hot cracking tendency. According to the variation of the solid-phase volume fraction with temperature shown in Figure 2, the values of |dT/dfs¹/²| of the ZL101A, ZL205A, and heat-resistant aluminum alloys were calculated when 0.91 < fs¹/² < 0.95, and the results were 39, 207, and 436, respectively. It can be seen that the hot cracking tendency of the three alloys was the smallest for ZL101A, followed by the heat-resistant aluminum alloy, and the largest for ZL205A, which was consistent with the experimental results.
3.2 Mechanical Properties of the New Heat-Resistant Aluminum Alloy
3.2.1 Microstructure
Figure 3 shows the microstructure of the as-cast and heat-treated high-strength heat-resistant aluminum alloy. As shown in Figures 3 (a) and 3 (b), the low-magnification metallographic structure of the new heat-resistant aluminum alloy in the as-cast state was similar to that of the ZL101A alloy, both being typical dendritic structures with a large amount of eutectic Si phase at the dendrite boundaries. In addition, a small amount of Mg₂Si phase and needle-like Al₅FeSi phase were present in the ZL101A alloy, while Al₂Cu phase and a small amount of Al (Cu,Sc) phase could be observed in the as-cast microstructure of the new heat-resistant aluminum alloy. Studies have shown that in Al-Cu-based casting alloys, the addition of Sc element can effectively segregate at the interface between the θ′ phase and the matrix, reducing the interfacial energy between the θ′ phase and the matrix and improving the thermal stability of the θ′ phase. The interfacial segregation of Sc element can also increase the nucleation density of the θ′ phase, further improving the material properties. Therefore, the presence of the Al (Cu,Sc) phase may be beneficial to the high-temperature stability of the new heat-resistant aluminum alloy. During the solution treatment process, the Si phase in the alloy partially dissolved and spheroidized (Figure 3 (c)), reducing the impact of the hard and brittle Si phase on plasticity compared with the as-cast state. Moreover, most of the Al₂Cu phase dissolved back into the matrix, reducing the risk of stress concentration and 有利于 improving the plasticity of the alloy. The T6-treated ZL101A alloy mainly exhibited precipitation strengthening through a small amount of β′-Mg₂Si precipitates, while the new heat-resistant aluminum alloy added relatively high contents of Cu and Mg elements. In addition to the precipitation of the θ′ phase in the α-Al matrix, a thermally more stable Q′-Al₅Cu₂Mg₈Si₆ phase could also be precipitated. This phenomenon could be observed in the TEM image of the aged state in Figure 3 (d), i.e., a large amount of needle-like θ′-Al₂Cu and fine spherical Q′-Al₅Cu₂Mg₈Si₆ phases were present in the microstructure after aging heat treatment. The Q′ phase could still maintain relatively high thermal stability at 300 °C and would not coarsen significantly, which was beneficial for improving the mechanical properties, especially the high-temperature mechanical properties, of the alloy.
Figure 3 | As Cast Low Magnification Microstructures of ZL101A(a) and New Heat-Resistant Aluminum Alloys(b), and Solid Solution Microstructure(c) and Aging State TEM Image(d) of New Heat-Resistant Aluminum Alloys |
---|
3.2.2 Tensile Properties
Table 2 shows the comparison of the tensile properties of the three casting aluminum alloys. It can be seen that the T6-treated single-cast sample of the new heat-resistant aluminum alloy had a relatively high tensile strength (Rm), with an average tensile strength above 420 MPa, significantly higher than that of the ZL101A alloy, but the elongation (A) was lower compared with the ZL101A alloy. Compared with the ZL205A alloy, the new heat-resistant aluminum alloy exhibited lower strength and plasticity.
Alloy | Separated test bar of casting | Test specimen from casting itself | ||
---|---|---|---|---|
Rm/MPa | A/% | Rm/MPa | A/% | |
New high-strength and heat-resistant aluminum alloy | 425 ± 7 | 1.2 ± 0.3 | 448 ± 23 | 1.3 ± 0.3 |
ZL101A | 310 ± 5 | 3.3 ± 0.7 | 241 ± 3 | 4.8 ± 2 |
ZL205A[12 – 18] | 484 ± 7 | 7.2 ± 7.0 |
To evaluate the heat resistance of the alloy, the high-temperature tensile properties of the T6-treated single-cast test bars of the new heat-resistant aluminum alloy were tested at 150, 180, 220, and 250 °C. At the same time, the tensile properties of the T6-treated test bars of the ZL101A alloy produced under the same conditions were tested at the same temperatures and compared with the data of the ZL205A alloy. As shown in Table 3, the new heat-resistant aluminum alloy had relatively high strength and good heat resistance. Its tensile strength at different temperatures was more than 100 MPa higher than that of the ZL101A alloy. Compared with the ZL205A alloy, the Cu content of the new high-strength heat-resistant aluminum alloy was relatively low. Although its room-temperature strength was lower than that of the ZL205A alloy, the strength loss of the new heat-resistant aluminum alloy was slower with increasing temperature, and it was better than the ZL205A alloy at 250 °C. This may be attributed to the higher thermal stability of the Q′ phase compared with the θ′ phase.
Temperature /°C | New high-strength and heat-resistant aluminum alloy | ZL101A alloy | ZL205A alloy[17] | |||
---|---|---|---|---|---|---|
Rm/MPa | A/% | Rm/MPa | A/% | Rm/MPa | A/% | |
150 | 346 | 1.5 | 220 |
3.2.2 Tensile Properties (Continued)
Temperature /°C | New high-strength and heat-resistant aluminum alloy | ZL101A alloy | ZL205A alloy[17] | |||
---|---|---|---|---|---|---|
Rm/MPa | A/% | Rm/MPa | A/% | Rm/MPa | A/% | |
150 | 346 | 1.5 | 220 | 8 | 390 | 11.5 |
180 | 319 | 1.5 | 199 | 7 | – | – |
220 | 288 | 1.5 | 175 | 7 | – | 10.5 |
250 | 242 | 2.0 | 140 | 9 | 204 | 19.0 |
As mentioned above, the heat-resistant performance of the new heat-resistant casting aluminum alloy was better than that of the ZL205A alloy and the commonly used ZL101A alloy in aviation engines at present, but its plasticity was lower than that of these two alloys. The room-temperature tensile fracture surface of the alloy was analyzed using a scanning electron microscope. It can be seen that there were porosity defects with a diameter of 0.5 – 1 mm in some local areas of the fracture surface, as shown in Figures 4 (a) and 4 (b). These defects mainly appeared at the bottom of the fracture surface, i.e., the location where cracks preferentially initiated. Figure 4 (c) shows that the porosity exhibited a network-like void similar to the dendrite boundary, and the interface was smooth without plastic deformation. It is 推测 that due to the relatively long solidification interval of the alloy (Figure 2), a small amount of quaternary eutectic reaction occurred in the later stage of solidification, forming the Q′-Al₅Cu₂Mg₈Si₆ phase. Since the quaternary eutectic temperature was relatively low and the liquid-phase content was relatively small at this time, the liquid phase in some local areas could not completely compensate for the solidification shrinkage, resulting in microscopic porosity. In the areas without porosity defects, a small-sized dimple morphology was observed (Figure 4 (d)), indicating good plastic deformation ability. Therefore, it is analyzed that the microscopic porosity was the main reason for the relatively low plasticity of the high-strength heat-resistant casting aluminum alloy. The ZL101A alloy was a casting aluminum alloy with β′-Mg₂Si as the precipitation strengthening phase. The β′ phase was prone to coarsening and growth at temperatures higher than 150 °C, resulting in relatively low high-temperature mechanical properties. Since the θ′-Al₂Cu and Q′-Al₅Cu₂Mg₈Si₆ phases in the high-strength heat-resistant casting aluminum alloy had higher thermal stability than the β′ phase, they exhibited higher strength than the ZL101A alloy in the test temperature range from room temperature to 250 °C. Compared with the ZL205A alloy, the high-strength heat-resistant casting aluminum alloy formed the Q′ phase with higher thermal stability than the θ′ phase in its microstructure. Although the θ′ precipitation phase still existed in the microstructure, the addition of a trace amount of Sc element helped to improve the thermal stability of the θ′ precipitation phase. Therefore, the tensile strength of the high-strength heat-resistant casting aluminum alloy was better than that of the ZL205A alloy at 250 °C (Table 3).
Figure 4 | Fracture Morphologies of High-Strength and Heat-Resistant Cast Aluminum Alloys at Room Temperature after Tensile Testing |
---|---|
(a), (b) | Fracture morphologies in region with porosities |
(c) | Enlarged image of porosities in fig.(b) |
(d) | Fracture morphology in region without porosities |
3.3 Casting Process and Performance Evaluation of the Complex Shell Casting
3.3.1 Casting Process Design
Given the excellent casting and heat-resistant properties of the new high-strength heat-resistant casting aluminum alloy, this study carried out application verification using a complex housing of an aviation engine as an example. The contour size of the housing was 260 mm × 220 mm × 60 mm, and several 5 mm thick reinforcing ribs were arranged on the outer surface. The overall wall thickness of the casting was uneven, with a thin wall thickness of 4 mm and a thick wall thickness of up to 25 mm. In addition, multiple 异型 curved and spatially interleaved oil passages were arranged in the inner cavity of the casting, as shown in Figure 5. The housing needed to meet the requirements of no air leakage in a 0.5 MPa airtightness test and no oil leakage in a 33 MPa hydraulic test. The surface quality and internal quality of the casting needed to meet the HB 963 – 2005 standard, and it was required to be formed by metal casting.
Figure 5 | Schematic Diagrams of Complex Shell Casting Structure |
---|---|
(a) | Outline structure |
(b) | Intracavity structure |
Due to the uneven overall wall thickness of the casting, the curved and interleaved arrangement of the inner cavity oil passages, the metal melt flowing to the thin-wall parts during the casting filling process was prone to rapid temperature loss and a decrease in flow velocity, resulting in cold shut or insufficient filling defects. The mounting interfaces on both sides of the casting were thick and large structures, and the intersection parts with the surrounding structures formed relatively large hot spots. During the solidification process, these hot spots were the last to solidify. If the feeding was insufficient, porosity defects were prone to occur. Moreover, the metal mold had no yielding property, and the intersecting structures on the outer surface of the casting were prone to hot cracking defects during the volume shrinkage in the later stage of solidification. In addition, the inner cavity oil passages had a complex 异型 structure and could only be formed using sand cores. The vertically and horizontally interleaved sand cores were likely to cause poor internal feeding channels of the casting. At the same time, the gas generated by the sand cores was likely to cause more pores during casting, and the complex outer shape and vertically and horizontally interleaved sand cores also affected the escape of gas in the mold cavity, resulting in pore defects remaining in the casting. Therefore, during the casting process design stage, it was necessary to consider avoiding casting defects such as pores, porosity in the thick and large hot spot areas, insufficient filling in the reinforcing rib areas, and cold shut on the thin-wall oil passage walls while ensuring rapid sequential solidification, so that the casting had good surface quality and dense internal quality after casting.
Tilting casting involved pouring the metal melt into a pouring basin and slowly flowing the metal liquid into the mold cavity under the action of gravity by tilting the mold at a specified speed using a casting machine. By controlling the tilting speed at different angles, different filling speeds could be achieved. Compared with the ordinary top gating method, this process could avoid splashing and turbulence caused by too fast metal flow velocity. Compared with the bottom gating method, it could ensure that the alloy liquid entering the riser cavity later had a relatively high temperature, which was beneficial for the sequential solidification of the casting. To ensure the metallurgical quality of the casting, this study adopted the tilting casting process for production. The overall forming scheme was to use a metal mold to form the complex outer shape of the casting and a thermosetting resin sand core to form the inner cavity oil passages. A top riser was designed on the top of the housing casting with a large processing surface for centralized feeding, and side risers were designed on both thick sides of the casting for feeding. The Anycasting software was used to simulate and optimize the casting process scheme. By adjusting the local process allowance and casting fillet, a casting process scheme was formed after iterative simulation, as shown in Figure 6. According to this scheme, a set of two-part metal mold tilting casting molds and two sets of thermosetting resin sand shell core molds were designed and manufactured, as shown in Figure 7.
Figure 6 | Pouring Scheme of Heat-Resistant Cast Aluminum Alloy |
---|
Figure 7 | Schematic Diagrams of Casting Mould |
---|---|
(a) | Metal outline mould |
(b), (c) | Shell mould |
3.3.2 Performance Evaluation of the Casting
The high-strength heat-resistant aluminum alloy housing casting was subjected to T6 heat treatment, and its tensile properties, macrostructure grade, internal quality, airtightness, and pressure resistance were analyzed and compared with those of the ZL101A housing casting with the same structure and casting process in the company. As can be seen from Table 2, the tensile strength of the samples cut from the heat-resistant aluminum alloy casting body was significantly higher than that of the single-cast samples, with an average value more than 200 MPa higher than that of the samples cut from the same position of the ZL101A casting body. Aluminum alloy had a relatively strong gas absorption tendency, and hydrogen absorption and release during melting and casting were inevitable, resulting in pinhole defects. Low-magnification samples were cut from the position near the casting at the root of the riser and detected according to the method in JB/T 7946.3 – 2017, and the porosity level was rated according to the standard spectrogram in HB 963 – 2005. After testing, the porosity of the casting reached level 1, which was equivalent to the same level of the ZL101A alloy metal casting.
The casting was inspected by fluorescent penetrant testing according to the HB/Z 61 standard method. None of the 10 castings had linear defects and penetrating defects, and there were no cold shut and hot cracking defects. The surface quality of the casting met the HB 963 – 2005 standard requirements, further indicating that the new heat-resistant casting aluminum alloy had excellent casting fluidity and low hot cracking tendency. The casting was inspected by X-ray according to the HB 20160 standard method. One of the cross-sectional X-ray films of the casting is shown in Figure 8. It can be seen that the casting had a dense microstructure. According to the requirements for Class II castings in the HB 963 – 2005 specification, the internal quality of the 10 castings was evaluated, and the casting qualification rate reached 80%, which was equivalent to the X-ray inspection qualification rate level of the ZL101A alloy casting of the same type.
Figure 8 | X-ray Detection Film of High-Strength and Heat-Resistant Aluminum Alloy Shell Castings |
---|
The airtightness of the casting was tested by pressurization. First, 0.5 MPa compressed air was introduced into the inner cavity of the shell, and then the casting was immersed in kerosene to check the airtightness. After testing, none of the 10 castings leaked air. Finally, 33 MPa hydraulic oil was introduced into the inner cavity of the shell for a strength pressure test. None of the 10 castings cracked or leaked, meeting the product performance requirements.
4. Conclusions
(1) The Al-Si-Cu-Mg-Sc high-strength heat-resistant casting alloy had good casting fluidity, low hot cracking tendency, and high airtightness. Its casting process performance was better than that of the ZL205A high-strength casting aluminum alloy. The alloy could meet the requirements of the metal casting process and was suitable for producing complex shell castings with high airtightness, thin walls, and multiple inner cavities.
(2) The room-temperature tensile strength of the high-strength heat-resistant casting aluminum alloy was higher than that of the ZL101A alloy but lower than that of the ZL205A alloy. The strength decreased slowly with increasing temperature, and its tensile strength at 250 °C was better than that of the ZL205A alloy. The elongation of the single-cast samples and the samples taken from the housing casting body was at the level of 1% – 1.5%. The presence of porosity with a diameter of 0.5 – 1 mm was the main reason for the relatively low plasticity.
(3) The complex oil pump housing designed based on the Al-Si-Cu-Mg-Sc casting aluminum alloy was prepared using the metal mold tilting casting process. The quality of the produced casting met the technical requirements of the HB 963 – 2005 standard, and the metallurgical quality of the casting was equivalent to that of the ZL101A alloy casting of the same type.
In summary, the new Al-Si-Cu-Mg-Sc high-strength heat-resistant casting aluminum alloy has excellent properties and great application potential in the field of aviation engine complex shell castings. Future research can focus on further optimizing the alloy composition and process to improve its comprehensive performance and meet the increasingly stringent requirements of aviation engines.
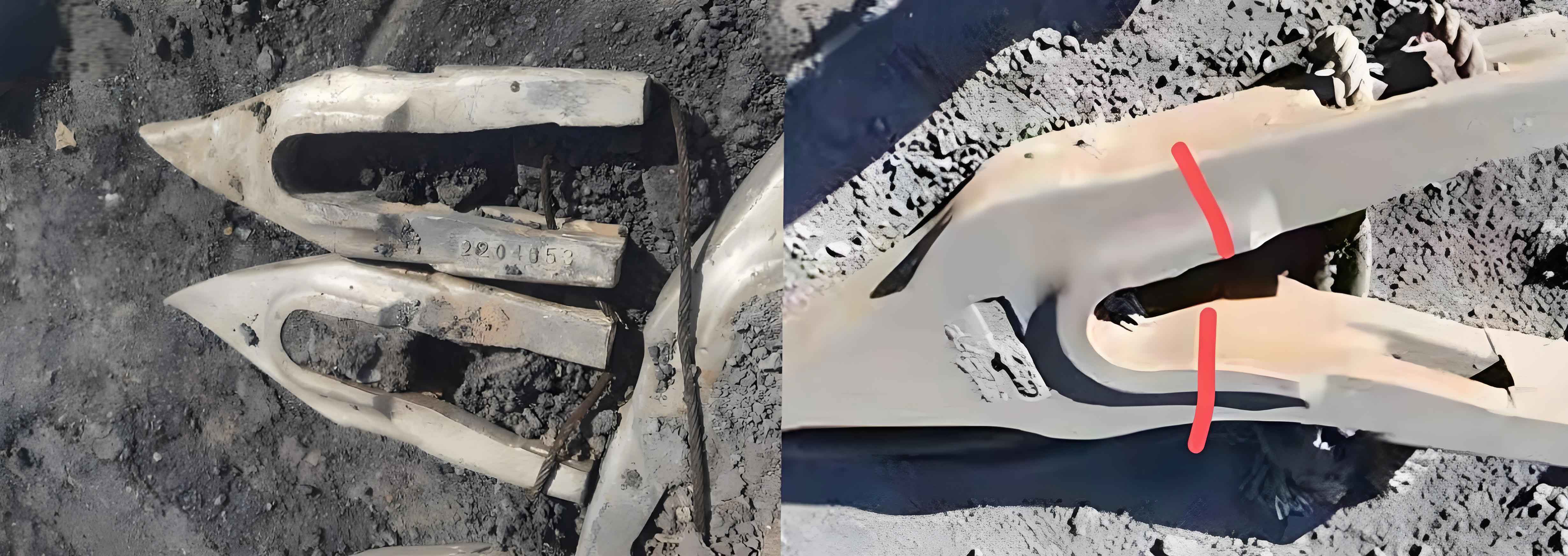