Figure 1 shows the location of shrinkage porosity in a casting. See Figure 2 for the process plan before improvement. After pouring, overheating occurred at positions 1, 2 and 3 in Figure 1, and the casting shrinkage defects were serious. See Figure 3 for the improved process plan. The heat dissipation condition of the casting after pouring was improved, and the shell temperature was reduced to about 600 ℃ before pouring. The heat dissipation condition was further improved, and the shrinkage defect of the casting was solved.
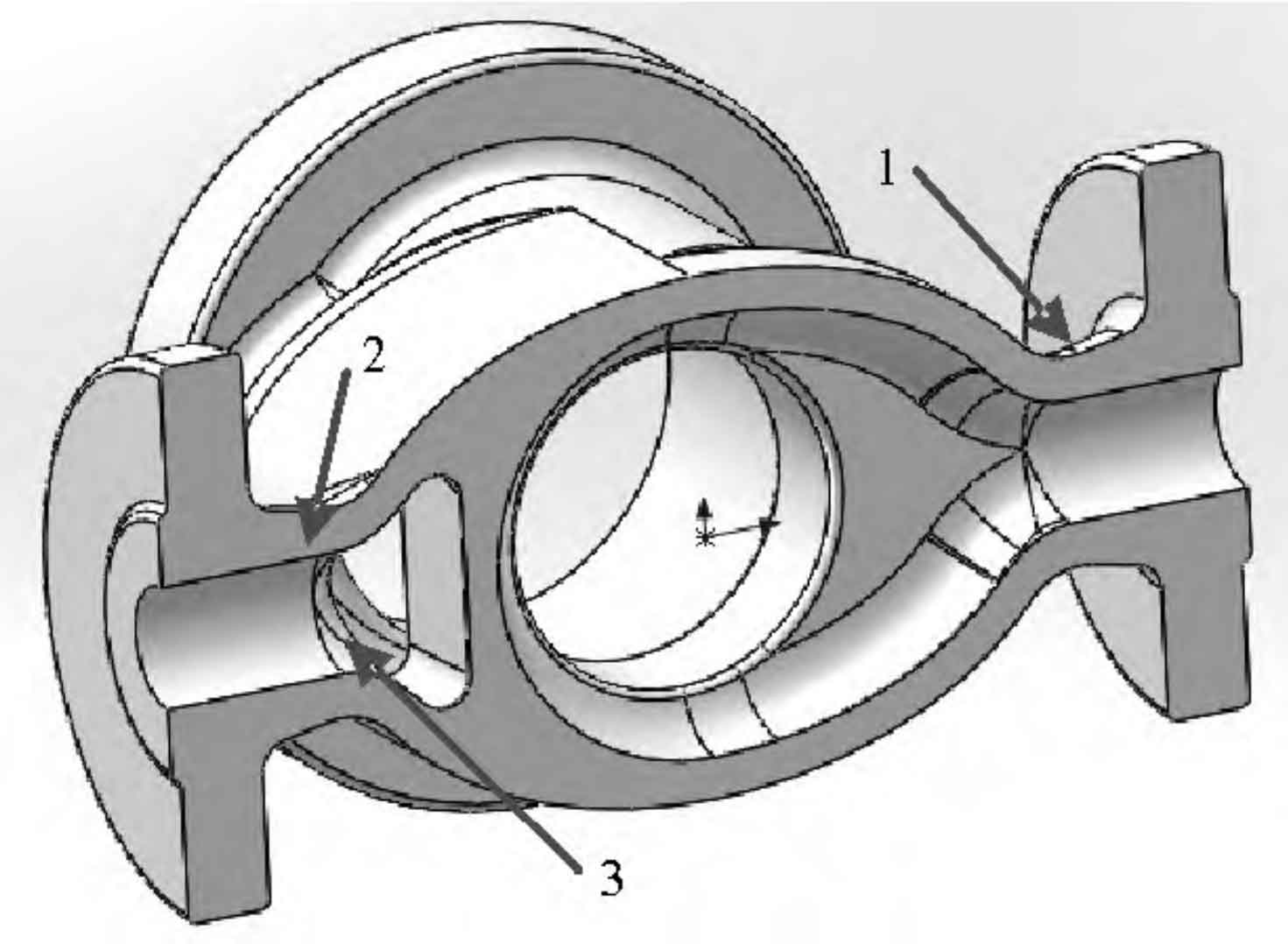
In addition, there are many ways to eliminate shrinkage defects by improving the heat dissipation conditions, such as buried sand cooling of the casting shell after pouring, dispersed placement cooling of the casting shell after pouring, cooling of the casting shell on the shelf after pouring, water cooling after pouring, local chilling, etc. The ambient temperature of the casting workshop will also affect the shrinkage defects of the casting.
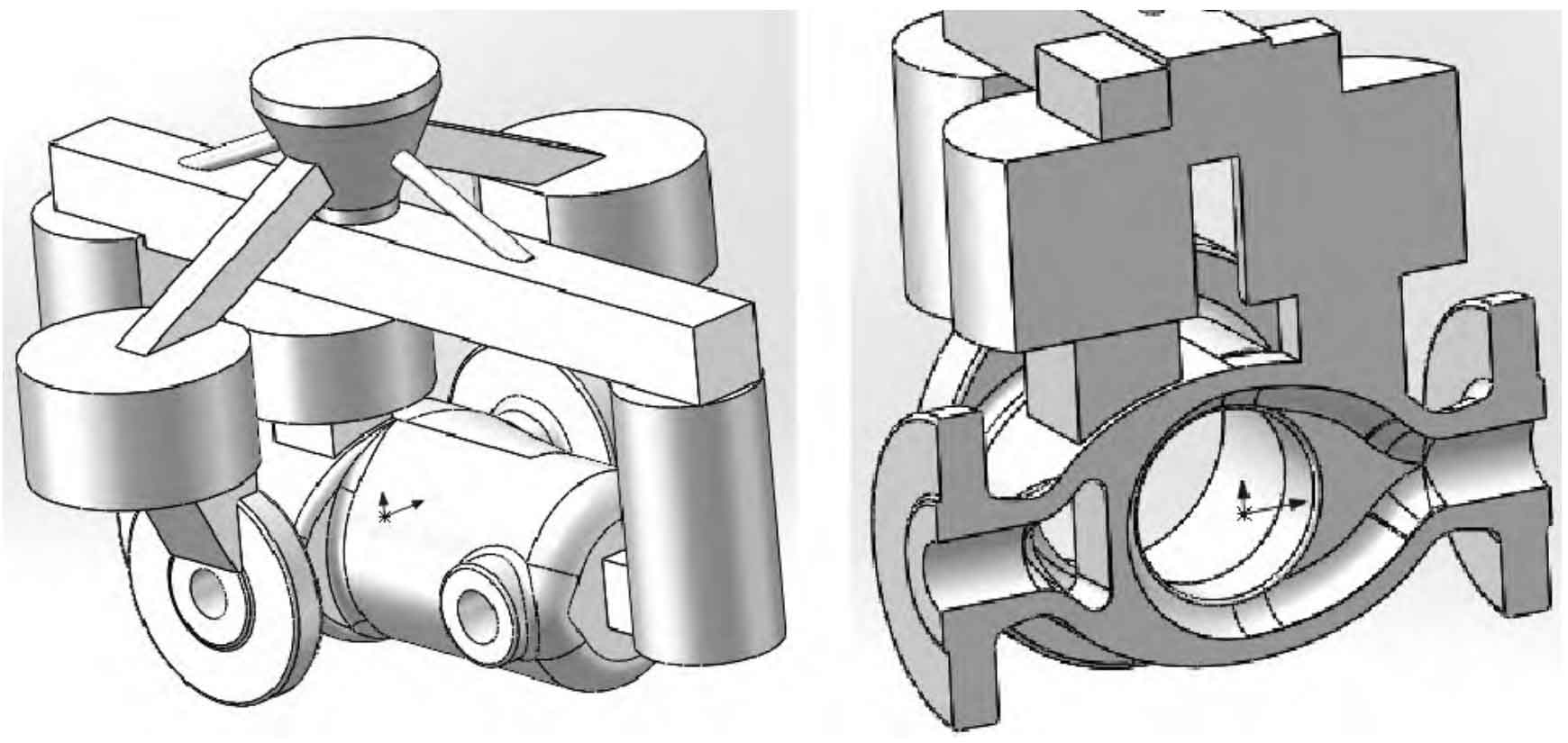