The existence of white zone is one of the characteristics of austempered ductile iron. Quenched martensite and retained austenite are generally called white zone. Its existence, especially the quenching martensite in the white zone, significantly reduces the plasticity and toughness of the crankshaft, and reduces the bending fatigue resistance of the crankshaft.
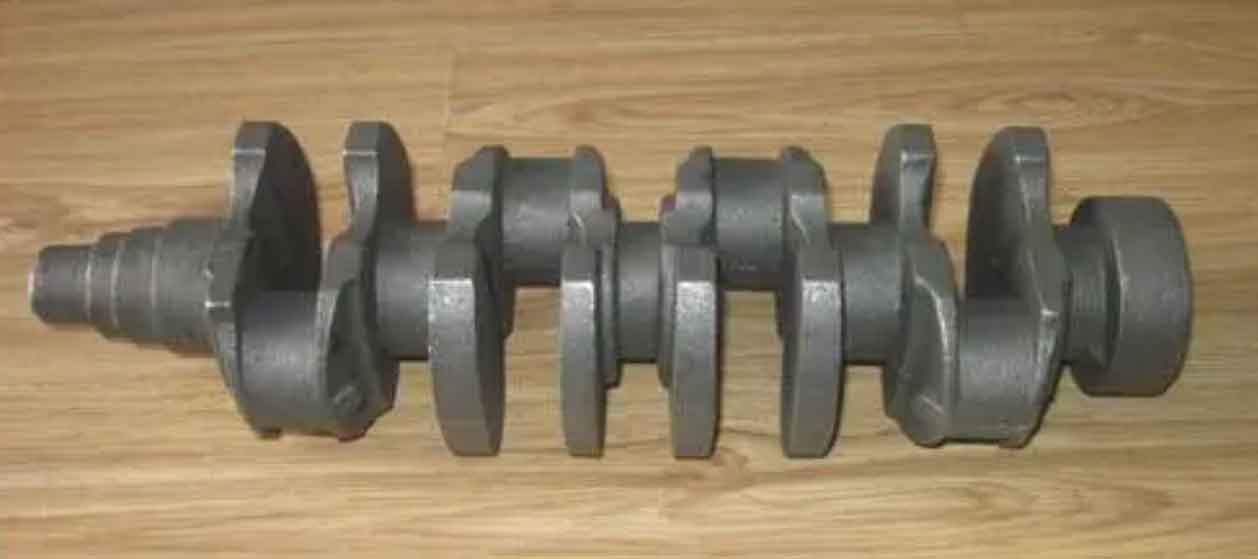
1. Shape and position of white area
The white zone is located at the junction of eutectic clusters, where anti graphitization elements such as manganese, phosphorus and chromium are easy to segregate, inhibiting bainite transformation and stabilizing austenite. Quenched martensite often coexists with lower bainite in the white zone, while residual austenite often coexists with upper bainite in the white zone. The two interlaced make the residual austenite fragmented.
2. Main factors affecting the number of white areas
2.1 Process factors
High austempering temperature has good Austenite Stability, and most of the retained austenite in the white zone after austempering; The austempering temperature is low, and the quenching martensite is in the majority in the white zone after austempering.
2.2 Chemical composition
Silicon is mainly dissolved in the matrix, which significantly promotes bainite transformation, especially enriched around graphite. With high silicon content, it can increase bainite volume and reduce the number of white areas. In order to improve the toughness of austempered ductile iron, the silicon content can be increased.
Manganese is easy to segregate at the eutectic grain boundary in ductile iron, which improves the hardenability of this region and is conducive to the formation of quenched martensite in the white zone. In order to improve the toughness of austempered ductile iron, the manganese content can be reduced.
The positive segregation of phosphorus at the eutectic grain boundary increases the number of white areas, but the phosphorus content in nodular cast iron is low, so the effect of phosphorus is small. The common alloy elements affect the fluidity of molten iron, tend to form shrinkage cavity and porosity, and increase the hardenability of nodular cast iron, which is conducive to the formation of quenched martensite in the white zone. In order to improve the toughness of Austempered nodular cast iron, the content of alloying elements in nodular cast iron crankshafts should be low, even without alloying elements.
2.3 Micro area composition
Region | Mn(%) | Si(%) | Cr(%) | Fe(%) |
White area | 1.78 | 1.25 | 0.51 | 95.22 |
Bainite zone | 0.17 | 2.33 | 0.10 | 97.41 |
Micro segregation is also one of the reasons for the formation of white zone, and is the main reason for the formation of quenched martensite in white zone. The energy spectrum analysis has been carried out for the white area of Austempered nodular cast iron crankshaft (evaluated as grade 3 according to JB 3021-1981 metallographic standard for austempering of rare earth magnesium nodular cast iron, and most of the quenching martensite is in the white area). The results are shown in Table 3. The content of manganese and chromium in the white area is 4~5 times that in the normal bainite area, and the segregated alloy elements are the main reason for the formation of quenching martensite.