Abstract
This paper delves into the precision casting of heat-resistant austenitic steel specifically designed for boiler pipe fittings. It analyzes the optimization of casting processes to enhance the material’s performance under high-temperature conditions, emphasizing corrosion resistance and tensile strength. Through comprehensive experiments and thermodynamic calculations, this study identifies the optimal processing conditions for heat-resistant austenitic steel to ensure its suitability for precision casting of boiler pipe fittings.
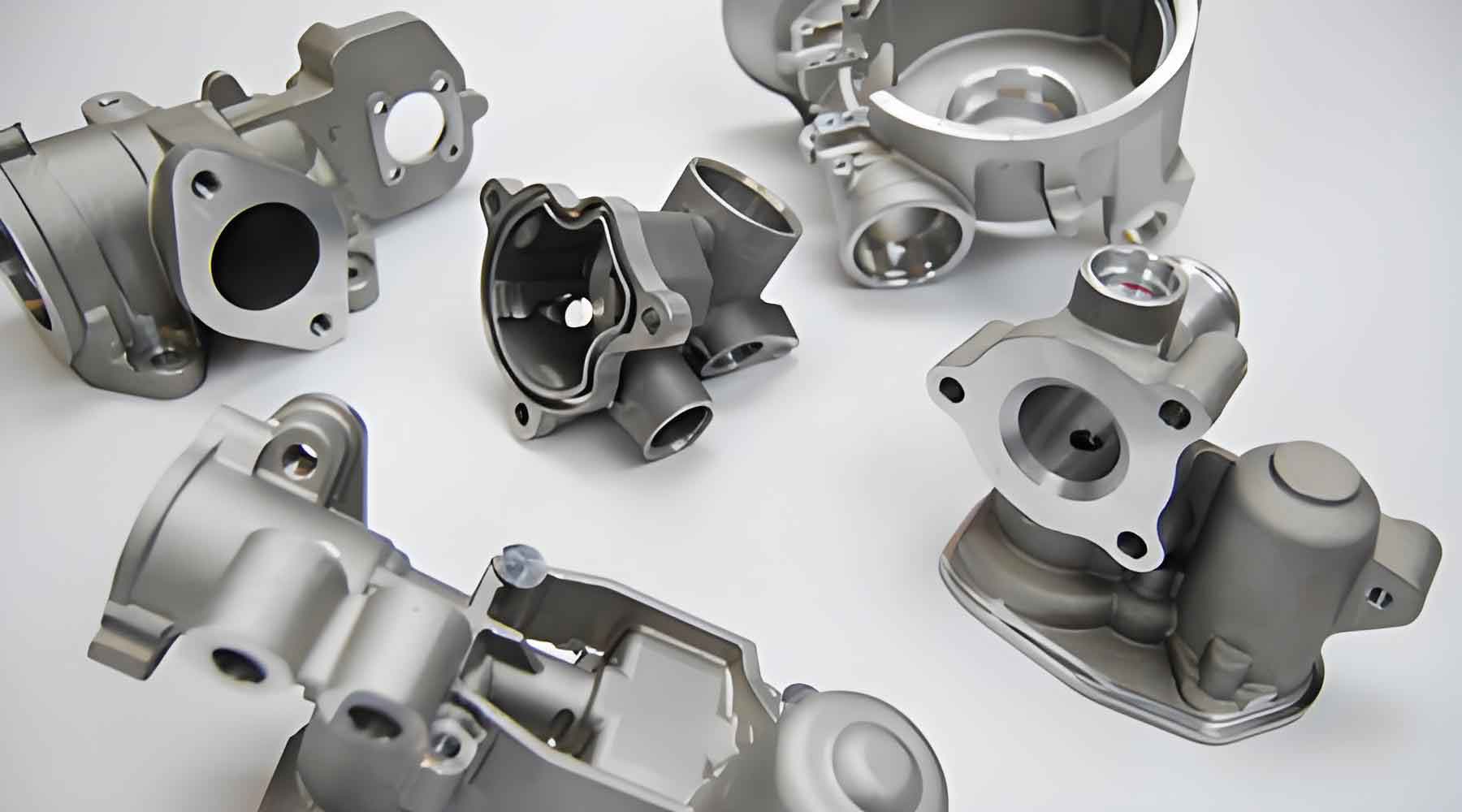
Introduction
The demand for high-performance materials in the energy sector, particularly for boiler applications, has significantly increased in recent years. Heat-resistant austenitic steels have emerged as a viable option due to their exceptional corrosion resistance, high-temperature strength, and ductility. Precision casting techniques play a pivotal role in the production of boiler pipe fittings, ensuring dimensional accuracy and material integrity. This study focuses on optimizing the precision casting process for heat-resistant austenitic steel used in boiler pipe fittings.
Materials and Methods
1. Material Selection
Heat-resistant austenitic steel with the composition Fe-15%Cr-25%Ni-3.5%Al-0.6%Nb-2%Mo-0.02%C (by weight) was chosen for this study. This composition provides excellent corrosion resistance and high-temperature strength, making it ideal for boiler pipe fittings.
2. Casting Process
The casting process involves the following steps:
- Melting and Alloying: The steel was melted in a vacuum induction furnace to ensure homogeneity and to minimize impurities.
- Pouring and Solidification: The molten steel was poured into preheated molds designed for precision casting.
- Cooling and Heat Treatment: The castings were subjected to a heat treatment regimen to refine the microstructure and improve mechanical properties.
3. Experimental Setup
- Thermodynamic Calculations: JMatPro software was utilized to simulate the phase transformations and precipitation behavior of the alloy at different temperatures.
- Mechanical Testing: Tensile, bend, and impact tests were conducted on the castings to evaluate their mechanical properties.
- Corrosion Testing: The castings were exposed to various temperatures in a controlled environment to assess their corrosion resistance.
Results and Discussion
1. Thermodynamic Calculations
The thermodynamic calculations revealed the phase stability and precipitation behavior of the heat-resistant austenitic steel at various temperatures (600-1200°C). the phase distribution at 650°C, with the austenitic phase accounting for 82% of the microstructure, followed by NiAl (6.64%), σ-phase (10.88%), and MC carbides (0.19%).
2. Microstructural Analysis
Optical microscopy was employed to analyze the microstructure of the castings. the micrographs of the as-cast and heat-treated samples. The as-cast microstructure exhibits a coarse grain structure with some porosity, while the heat-treated sample displays a finer grain structure with a more uniform distribution of precipitates.
3. Mechanical Properties
Table 1 summarizes the mechanical properties of the heat-resistant austenitic steel at different cold deformation levels. As the cold deformation increases from 0% to 50%, both the yield strength and tensile strength increase, while the elongation decreases. However, the increase in strength becomes less pronounced above 20% deformation.
Cold Deformation (%) | Tensile Strength (MPa) | Yield Strength (MPa) | Elongation (%) |
---|---|---|---|
0 | 798 | 405 | 50 |
20 | 1082 | 866 | 29 |
50 | 1131 | 889 | 15 |
Table 1: Mechanical properties of heat-resistant austenitic steel at different cold deformation levels.
4. Corrosion Resistance
The corrosion resistance of the heat-resistant austenitic steel was evaluated at temperatures ranging from 650°C to 725°C. Table 2 shows the corrosion parameters, including corrosion pit depth, external oxide layer thickness, and internal oxide zone width. The results indicate that the material’s corrosion resistance decreases with increasing temperature, with S31042 exhibiting the best corrosion resistance.
Material | Temperature (°C) | Corrosion Pit Depth (μm) | External Oxide Layer (μm) | Internal Oxide Zone (μm) |
---|---|---|---|---|
S31035 | 650 | 20-80 | 200-400 | 10-30 |
675 | 30-120 | 20-80 | 10-30 | |
700 | 40-150 | 20-50 | 15-30 | |
725 | 50-180 | 30-100 | 20-50 | |
S31042 | 650 | 10-40 | 100-200 | 10-20 |
675 | 20-60 | 10-30 | 10-20 | |
700 | 20-80 | 20-30 | 0-10 | |
725 | 20-100 | 20-50 | 10-30 |
Table 2: Corrosion parameters of heat-resistant austenitic steel at various temperatures.
5. Optimization of Processing Parameters
The optimization of casting and heat treatment parameters played a crucial role in improving the material’s performance. Preheating the molds to ≥5°C, maintaining a voltage of 13-14V, using a current range of 190-200A, and controlling the interlayer temperature between 50-230°C resulted in castings with excellent dimensional accuracy and minimal defects.
Conclusion
This study successfully optimized the precision casting process for heat-resistant austenitic steel used in boiler pipe fittings. Through thermodynamic calculations, microstructural analysis, mechanical testing, and corrosion resistance evaluations, the optimal processing conditions were identified. The results indicate that cold deformation up to 20% enhances the material’s strength without significantly compromising its ductility. Furthermore, proper heat treatment refines the microstructure and improves corrosion resistance. Overall, this study provides valuable insights into the precision casting of heat-resistant austenitic steel for boiler pipe fittings, ensuring their suitability for demanding high-temperature applications.