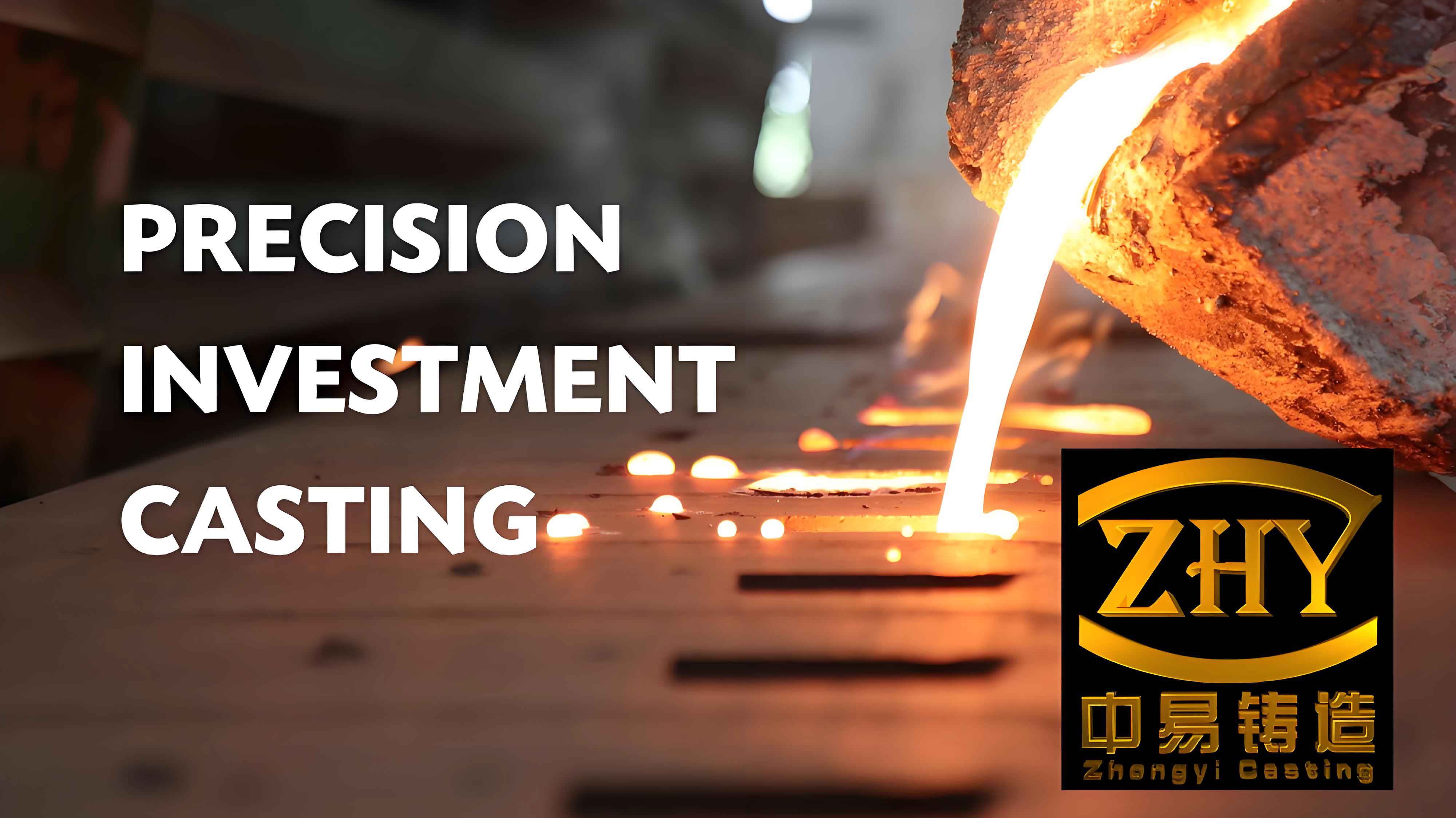
1. Introduction to Precision Investment Casting and Surface Pitting Defects
Precision investment casting, also known as lost-wax casting, is a highly refined manufacturing process widely used to produce complex, near-net-shape metal components with exceptional dimensional accuracy and surface finish. This method is particularly favored in aerospace, automotive, and medical industries, where component integrity and aesthetics are critical.
However, surface pitting defects—manifested as gray-black spots, pits, or depressions—remain a persistent challenge in precision investment casting, especially for 200/400 series stainless steels, carbon steels, and low-alloy steels. These defects not only compromise the visual appeal of castings but also necessitate costly post-processing or lead to scrapped parts. This article delves into the root causes of pitting and outlines actionable strategies to mitigate these defects, ensuring higher yield and cost efficiency in precision investment casting operations.
2. Characteristics of Surface Pitting Defects
Surface pitting defects typically exhibit the following characteristics:
- Morphology: Small, irregularly shaped depressions or craters (0.1–2.0 mm in diameter) on polished or sandblasted surfaces.
- Common Materials: Predominantly observed in 200/400 series martensitic stainless steels, carbon steels (C ≤ 0.25%), and low-alloy steels.
- Impact: Defects are often irreparable via conventional grinding, leading to increased rejection rates.
3. Root Causes of Surface Pitting in Precision Investment Casting
Surface pitting arises from the interaction between molten metal oxides and impurities in the shell mold system. Key contributing factors include:
3.1 Suboptimal Gating System Design
- Issue: Poor placement of ingates or improper cluster orientation traps residual wax during dewaxing. Residual wax carbonizes during shell firing, reacting with molten metal to form oxides.
- Critical Parameters:
- Ingate positioning relative to thermal hotspots.
- Wax drainage efficiency during dewaxing.
3.2 Low-Quality Shell Refractory Materials
- Issue: High Fe₂O₃ content (>0.05%) in facecoat materials (e.g., zircon flour/sand) promotes interfacial reactions with molten metal. For example:Fe2O3+Cr (in steel)→Cr-O-Fe compounds (pitting nuclei)Fe2O3+Cr (in steel)→Cr-O-Fe compounds (pitting nuclei)
- Critical Parameters:
- Purity of zircon, alumina, or fused silica-based refractories.
- Presence of low-melting-point impurities (e.g., K, Na oxides).
3.3 Incomplete Shell Firing
- Issue: Inadequate shell pre-firing (<950–1200°C) leaves moisture, organics, or salts in the mold. During pouring, these volatiles generate gases that oxidize the metal surface.
- Critical Parameters:
- Firing temperature and dwell time.
- Shell permeability and outgassing capacity.
3.4 Inadequate Metal Deoxidation
- Issue: Residual oxides (e.g., FeO, SiO₂, Al₂O₃) in the melt due to insufficient deoxidizer usage or improper sequencing. For instance, incomplete Al addition fails to reduce oxygen activity:3FeO+2Al→3Fe+Al2O33FeO+2Al→3Fe+Al2O3
- Critical Parameters:
- Deoxidizer type (Mn, Si, Ca, Al) and addition sequence.
- Post-deoxidation slag removal efficiency.
3.5 Secondary Oxidation During Cooling
- Issue: Exposure of hot castings (>800°C) to ambient oxygen promotes surface oxidation. This is exacerbated in Cr/Ni-lean steels (e.g., 201, 410 stainless steels).
4. Preventive Measures and Solutions
The following strategies address the root causes of pitting in precision investment casting:
4.1 Optimizing Gating System Design
- Actions:
- Position ingates away from thermal hotspots to minimize localized overheating.
- Incorporate auxiliary wax drainage channels or secondary dewaxing steps.
- Design Guidelines:ParameterRecommendationIngate locationOffset from geometric centerCluster orientationVertical alignment for gravity-assisted wax drainageWax removal efficiency>99% via vacuum dewaxing
4.2 Selecting High-Purity Refractories
- Actions:
- Use low-Fe₂O₃ (<0.05%) zircon or alumina-based facecoat materials.
- Implement magnetic separation and acid washing for raw materials.
- Material Specifications:Refractory TypeFe₂O₃ (%)SiO₂/Al₂O₃ (%)Grain Size (mesh)Zircon Sand≤0.05ZrSiO₄ >6680/120Fused Alumina≤0.02Al₂O₃ >99325High-Silica Sand≤0.10SiO₂ >9970/140
4.3 Enhancing Shell Firing Parameters
- Actions:
- Ensure complete binder burnout and moisture removal.
- Firing Parameters:Shell TypeTemperature (°C)Dwell Time (min)Waterglass-based950–105030–120Silica Sol-based1050–1200≥30
4.4 Improving Metal Deoxidation Practices
- Actions:
- Follow a staged deoxidation sequence: Mn → Si → Ca → Al.
- Control residual Al content (0.015–0.02%) to avoid excessive alumina formation.
- Deoxidation Protocol:StepDeoxidizerAddition Rate (% of melt)PurposePre-deoxidationMnFe0.5–1.0Initial oxygen scavengingIntermediateSiFe + CaSi0.3–0.5 + 0.1–0.2Slag formation and floatationFinalAl0.10–0.12Residual oxygen removal
4.5 Mitigating Secondary Oxidation
- Actions:
- Apply protective coatings (e.g., graphite powder) to shell backings.
- Use sealed cooling chambers with inert atmospheres (N₂/Ar) for Cr/Ni-lean steels.
- Cooling Guidelines:Material TypeCooling MethodAdditive201/410 StainlessImmediate sealing + wax covering10–30g waste waxCarbon SteelCovered sand with burnt mulletGraphite (0.3–0.5%)
5. Case Studies and Practical Recommendations
Case 1: Resolving Pitting in 420 Stainless Steel Valves
- Issue: Recurring pitting on valve surfaces post-polishing.
- Root Cause: Fe₂O₃-rich facecoat (0.12%) reacting with Cr in the alloy.
- Solution: Switched to high-purity fused alumina (Fe₂O₃ <0.02%) and optimized deoxidation with CaSi.
- Result: Pitting reduced by 85%, scrap rate lowered to <2%.
Case 2: Improving Surface Finish in Carbon Steel Gears
- Issue: Pitting and subsurface voids in gear teeth.
- Root Cause: Incomplete shell firing at 900°C (30 min).
- Solution: Increased firing temperature to 1050°C (60 min) and added graphite to backing layers.
- Result: Defect-free gears achieved; post-processing costs reduced by 40%.
6. Conclusion
Surface pitting in precision investment casting is a multifaceted challenge rooted in material interactions, process parameters, and environmental factors. By adopting a systematic approach—optimizing gating designs, selecting high-purity refractories, enforcing rigorous deoxidation protocols, and controlling cooling environments—foundries can significantly reduce defect rates. Emerging solutions, such as graphite-enhanced shell systems and advanced inert cooling techniques, further underscore the industry’s commitment to elevating the quality and reliability of precision-cast components.
Through continuous innovation and adherence to best practices, precision investment casting will remain indispensable in manufacturing high-integrity, complex metal parts for critical applications.