According to fracture mechanics, once the position of a certain point in the area near the top of the casting crack is determined, the stress intensity factor ki is the only control parameter of the stress, displacement and strain at that point, and the stress state at the tip of the casting crack is completely determined by the stress intensity factor at that point. Therefore, the fracture criterion of the material can be established according to the stress intensity factor and fracture toughness, that is, K Ι< K Ι C.
Under the action of cyclic load, the stress intensity factor ki usually changes with the change of load, and the difference between its maximum value and minimum value is called the stress intensity factor range, which is expressed by Δ Ki indicates. The stress intensity factor (SIF) increases with the expansion of casting crack size. For the same material, under different stress states, its fracture toughness is determined, and the occurrence of fracture is controlled by fracture conditions, because Δ Ki = (1-r) Kimax, so you can also Δ KIC = (1-r) KIC is used as the criterion for unstable propagation of casting cracks.
For casting defects, since the casting defects are two-dimensional or three-dimensional features, and the length of the casting cracks is one-dimensional features, it is impossible to accurately measure the casting crack length corresponding to the defect size from the defect fracture. It is necessary to establish an equivalent relationship between the casting defect size and the casting crack length. Assuming that the effect of the defect with area ADI perpendicular to the load direction in the fatigue process of the casting is equivalent to that of the initial crack defect with length AI (that is, the casting crack length AI is the equivalent initial crack length of area ADI), then the stress intensity factor values of the casting crack with length AI and the casting crack with area ADI are the same. Since the stress intensity factor calculation method based on the casting crack length is known, such as the formula, the equivalent initial crack length AI corresponding to the casting defect area AI can be obtained equivalently with the stress intensity factor as the intermediate variable.
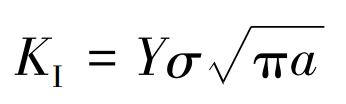
Where: y is the shape correction factor; σ Is the maximum stress; A is the equivalent initial crack length; Δ Ki is the stress intensity factor corresponding to the equivalent casting crack a.
In Paris formula, the propagation rate of casting crack is described by the propagation amount DA / dN of casting crack in a single cycle. When the casting crack extends from AI to AI + 1 after a stress cycle, the propagation rate of the crack is AI + 1-ai. The change value of stress intensity factor corresponding to the two casting crack lengths also increases from ki (I) to ki (I + 1), respectively. Therefore, the casting crack growth rate in this process can also be equivalently expressed as ki (I + 1) – ki (I) by the stress intensity factor, that is, the casting crack growth rate with the stress intensity factor as the parameter. The corresponding relationship between the casting crack growth rate based on the casting crack length and the casting crack growth rate based on the stress intensity factor can be obtained by simultaneously differentiating both sides of the formula equation, as shown in the formula:
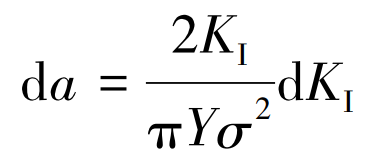
It is substituted into Paris formula to obtain the expression of casting crack growth rate description formula based on stress intensity factor:
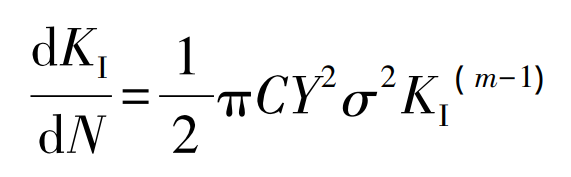
Where: C is the casting crack propagation coefficient; M is the casting crack growth index; C and M can be measured by casting crack growth test.
When the casting crack extends from the initial crack length A0 to the critical crack length AC under the action of cyclic stress, the stress intensity factor increases from ki0 in the initial state to the critical stress intensity factor (fracture toughness) KIC. For the castings containing defects, ki0 corresponds to the initial state AD0 of the casting defect area, and KIC corresponds to the fracture critical state ADC of the casting defect area. Finally, the number of cycles experienced by this process can be obtained by integrating the casting crack growth formula.
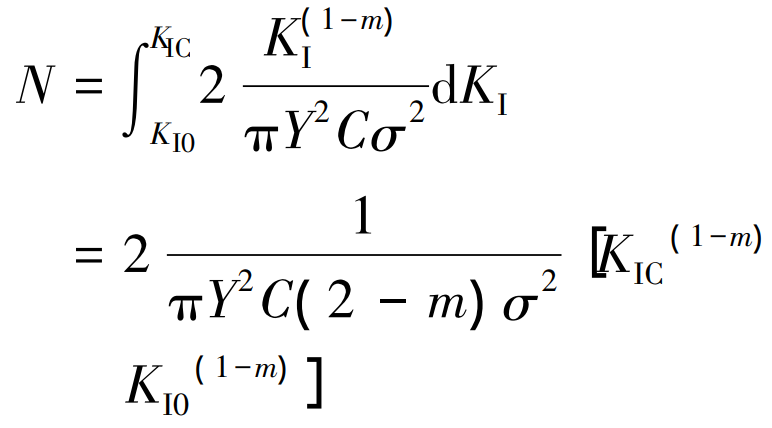
For a given stress intensity factor, the variation Δ In the case of Ki, according to Δ Ki = (1 - R) Ki, the formula can be rewritten as:
