During the production of lzqt600-3 ductile iron profile, due to its inherent process characteristics, the molten iron after spheroidizing treatment will have a rapid cooling phenomenon in the production process of horizontal continuous casting. In the water-cooled graphite crystallizer, the supercooling degree at the edge of the profile is the largest, and the molten iron in this part solidifies rapidly, 1 / 2R The undercooling degree of the section and the center decreases gradually, and the solidification time is relatively long. Therefore, such solidification mode directly leads to the uneven cross-section structure and uneven performance of the produced profiles. On the premise of studying the difference of microstructure and properties from the edge to the center of large section ductile iron profile, combined with the central shaft hole d = 35 mm and plunger distribution circle diameter D1 = 95 mm (Kawasaki k3v112 high pressure and large flow plunger and pump cylinder body [14]), Figure 2-1 is the sampling diagram, continuous casting lzqt600-3 profile edge a (Ф 100 mm) and B (Ф 70) at 1 / 2R of the large section ductile iron profile The sample block with the size of 15 mm × 20 mm × 40 mm is taken from the center C (Ф 35 mm).
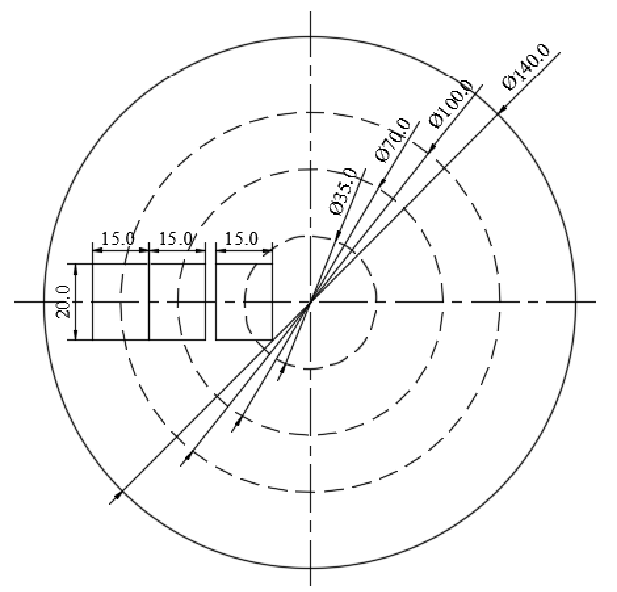
The as cast microstructure of edge, 1 / 2R and core was analyzed, and one sample was taken from each part, totaling 3 as cast samples; the samples of edge, 1 / 2R and core were nitrocarburized, and the experiment was designed by orthogonal test method L9 (34) orthogonal table was used to carry out nine groups of experiments. Because the samples were damaged by the analysis of the cross-section infiltration layer and the friction and wear test, two samples were prepared for each heat treatment process to ensure the preciseness and accuracy of the test; one cast sample was added as a comparison in the friction and wear test, totaling 57 samples.