The State Key Laboratory of advanced forming technology and equipment of China Academy of Mechanical Sciences has systematically studied the technology and equipment of sand mold digital dieless casting, and developed a series of digital dieless casting precision forming equipment with independent intellectual property rights (as shown in the figure), with the maximum forming size of 5000 mm × 3000 mm × 1000 mm. The equipment is mainly used for resin sand, coated sand, gypsum mold cutting processing, is a typical precision, green intelligent manufacturing equipment. Digital dieless casting precision forming technology and equipment can realize the short cycle, high precision, high quality and low cost manufacturing of large, complex, high precision and wide wall thickness castings. It is the development direction of single piece, small batch and customized production in the foundry industry in the future. It can fully guarantee the development speed of new products, improve the development quality of products, greatly reduce the development costs and promote the products Occupy the market as soon as possible. For example, it is well-known in China
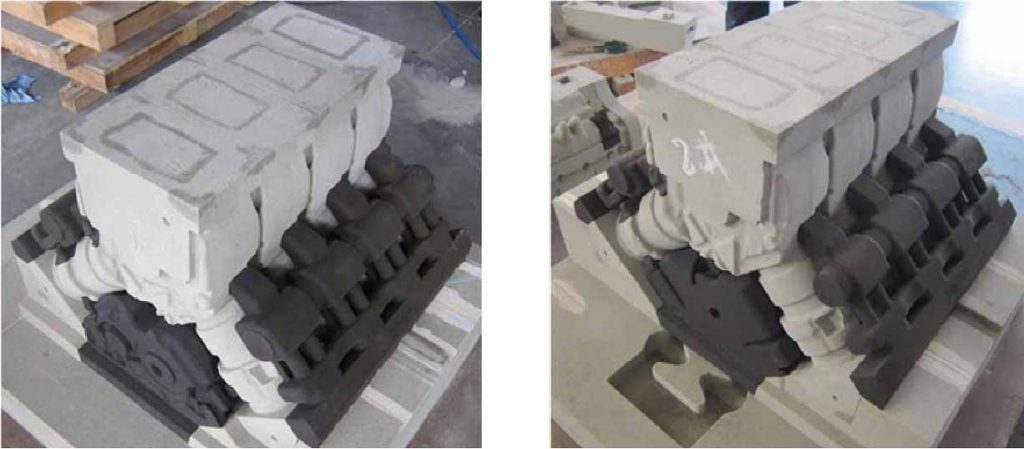
The internal combustion engine manufacturer has developed the cylinder block mold of V8 engine by using digital dieless casting technology and equipment (as shown in the figure). There is no need to develop mold in mold manufacturing process, which greatly shortens the manufacturing cycle and saves a lot of costs. The molding time of V8 engine block is 42h and the casting cycle is 20 days. If the design and development is carried out according to the traditional casting method, it will take at least 6 months, and the manufacturing cost will be as high as millions. It can be seen that the whole process from design and development to manufacturing can be realized very quickly, the intermediate manufacturing links can be effectively reduced, the development cost can be saved, the speed of putting products into the market can be accelerated, and the manufacturing efficiency can be improved.
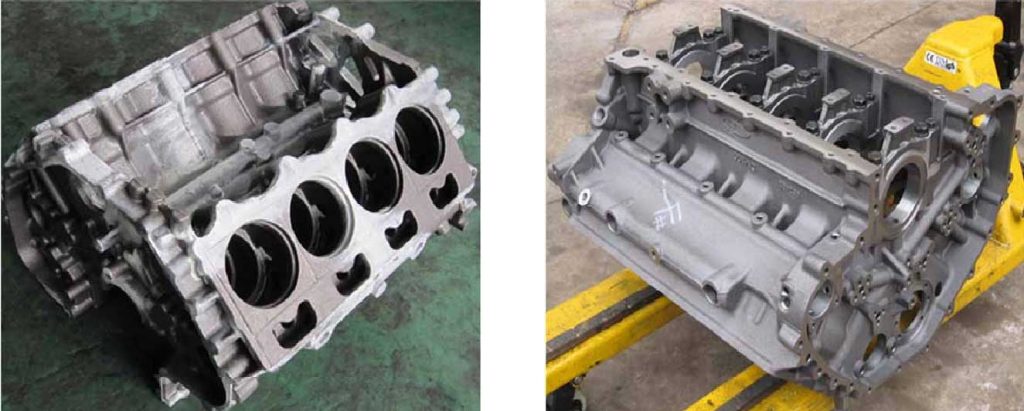
At present, the digital dieless casting precision forming technology has been determined as the development goal of advanced manufacturing technology in 2020 by “China Mechanical Engineering Technology Roadmap”, and has been promoted in many enterprises. It has been widely used in the design, development and production of large single piece and small batch engine cylinder block.
In terms of core making, the domestic foundry adopts cold box core making, hot box core making or film covering shell core making. The advantages of cold box core making process are obviously better than other core making processes, and it has been widely concerned and widely used in the domestic engine block casting industry. Based on the principle of energy-saving and low-carbon, the casting factories with annual output of about 10000 sets adopt PEPSET self hardening sand process and triethylamine cold box process. In addition, the combined process of lock core and multi sand core can greatly improve the dimensional accuracy of cylinder block iron castings, and the overall dimensional error is less than 0.3mm.
In the quality inspection of engine block, the wide application of computer, automation and intelligent detection technology makes the development of cylinder block casting industry enter a new era. More advanced, such as in the casting surface defect detection, German topometer company developed the engine cylinder surface detector. The system consists of a probe imaging unit, a control unit, an image processing unit and a display unit. The principle of the system is that the servo motor drives the camera to collect images on the surface of the cylinder block. The acquired images are analyzed and evaluated by the image processing unit, and finally the test report is generated. The image detection system of engine cylinder block and cylinder head introduced by Shanghai Volkswagen Company uses rectangular coordinate machine The equipment configuration is flexible, and the corners and special areas of the cylinder can still be detected comprehensively. At present, most manufacturers at home and abroad use this instrument for product testing.
The intelligent detection equipment for engine cylinder block and cylinder head casting is designed and developed by China Academy of Mechanical Sciences. The equipment is mainly composed of mechanical motion unit, electrical control unit, image and laser measurement unit, data processing unit and characteristic parameter storage unit. The equipment can not only detect the surface defects of engine cylinder block and cylinder head on-line, but also detect the flatness and Brinell hardness of engine cylinder block and cylinder head on-line.