Gasket castings are produced by two pieces in one box. Considering the same distance from the casting system to each part of the castings, a casting is simulated and analyzed.The three-dimensional casting model is introduced into AnyCasting, meshed and repaired to meet the analysis requirements.
Parameter setting: setting heat transfer coefficient of air and other entities is 0.001 W/(m2.C), heat transfer coefficient of casting and sand is 0.1 W (m2.C), pouring temperature is 1 350 C, material shrinkage rate of nodular cast iron is 0.8%, data acquisition frequency is selected as filling mode, solidification is completed every 5% acquisition, and casting is selected as 100% solidification at the end condition.
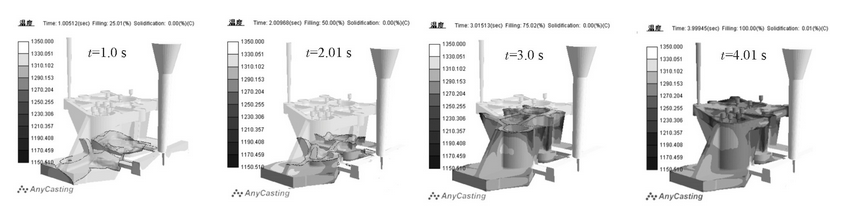
After casting process improvement, the model was analyzed.The filling analysis of the modified casting is shown in Figure 1.After adding risers and vents at the top of the casting, the metal liquid color band becomes more uniform and the filling process is smoother.
After casting process improvement, the model was analyzed.The filling analysis of the modified casting is shown in Figure 1.After adding risers and vents at the top of the casting, the metal liquid color band becomes more uniform and the filling process is smoother.
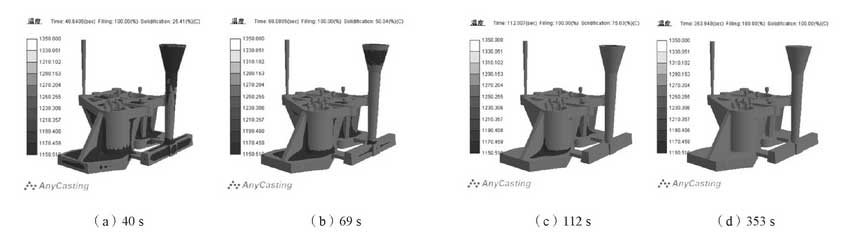
The entire filling solidification process of the optimized castings is simulated as shown in Figure 2.After the process improvement, the casting solidification is more orderly, the local residual heat is reduced, and the areas where hot spots exist inside the casting are significantly improved.As can be seen from Figure 10c, the pouring system has been completely cooled, at which time the casting cooling rate reaches about 75%.Cold iron is set at the bottom hot spot of the castings, which accelerates the cooling rate of the castings. The combination of riser and cold iron plays a great role in the compensation of the castings.
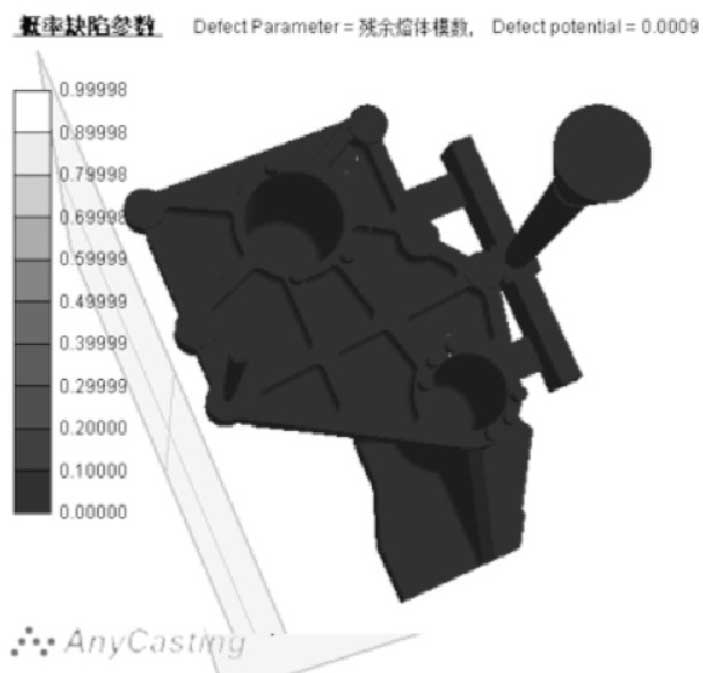
Similarly, the probabilistic defect parameters of the optimized castings are analyzed. As shown in Figure 3, the defects at the bottom of the castings and the joint of the two cylinder cavities are obviously disappeared, and the potential defects account for 0.09% of the volume of the castings. The proportion of defects is reduced by half compared with the previous ones, and the defects of the castings are concentrated in one position and can be removed by later machining.Therefore, the feed system and air outlet are set in the process, which effectively reduces casting defects and improves the yield of the casting.The casting defect area after analysis and optimization shows that the yield rate of casting process reaches more than 90%.