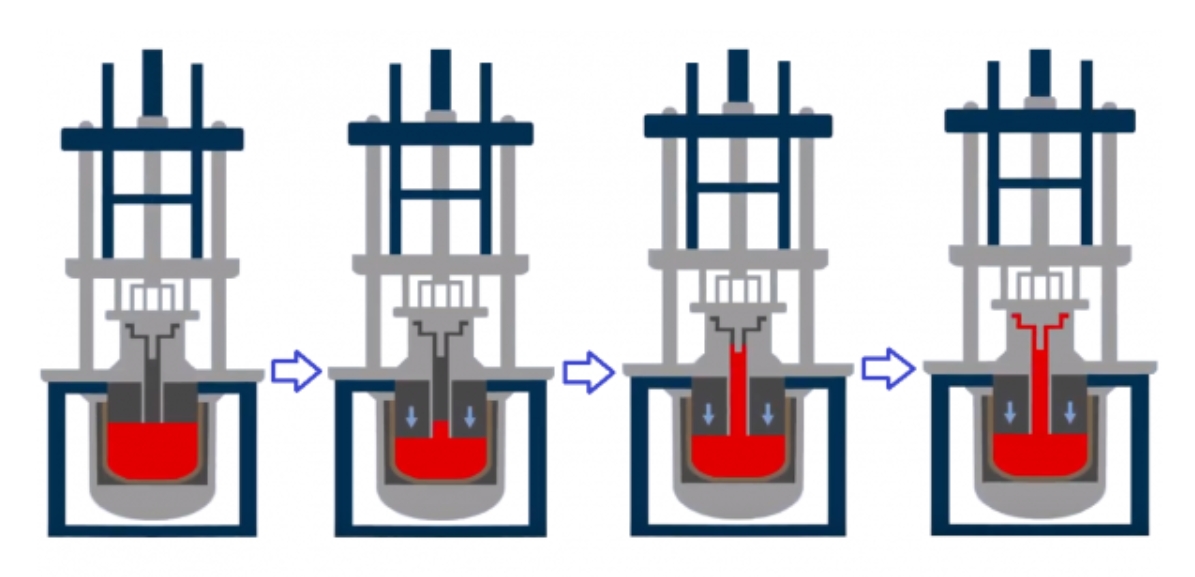
1. Casting Defect in Cylinder Head of Low Pressure Casting
1.1 Introduction
With the development of the automotive engine industry and the requirement of vehicle lightweight, aluminum alloys are widely used in the automotive and engine industries. However, due to the complex structure and process of aluminum alloy cylinder heads, casting defects are prone to occur, such as pinhole defects in low pressure casting aluminum alloy cylinder head castings. This article analyzes the causes and prevention of pinhole defects in aluminum alloy cylinder head castings.
1.2 The Formation of Pinholes in Cast Aluminum Alloys
Pinholes in aluminum alloys are caused by the gas (99%H2) dissolved in the aluminum melt escaping and not completely precipitating out of the casting during solidification. The solubility of hydrogen in aluminum alloys increases with the increase of alloy liquid temperature and decreases with the decrease of temperature. When the hydrogen content exceeds its solubility during cooling and solidification, hydrogen bubbles will be precipitated. If the supersaturated hydrogen bubbles cannot converge or precipitate in time, they will form fine and dispersed pores, that is, pinholes. In addition, if the crystallization temperature range of the aluminum alloy is large, a dendritic structure will be formed, and the residual aluminum liquid in the dendritic crystal gap may form a vacuum during further cooling and contraction, resulting in the precipitation of hydrogen and the formation of pinholes.
1.2.1 The Relationship between Pinhole Formation and Environmental Humidity
In general production conditions, when aluminum alloys are melted and poured in an atmosphere with high relative humidity, the pinhole defects in the castings are particularly serious. This is why there are fewer pinhole defects in aluminum alloy castings in dry seasons than in rainy and humid seasons, and it is also the main reason for the high proportion of pinhole defects in aluminum alloy castings in Chongqing.
1.2.2 The Relationship between Pinhole Formation and Crystal Structure
For aluminum alloys, if the crystallization temperature range is large, a reticular pinhole structure will be formed. This is because, under general casting production conditions, the casting has a wide solidification temperature range, which makes the aluminum alloy easy to form a developed dendritic crystal. In the later stage of solidification, the residual aluminum liquid in the dendritic crystal gap may be isolated from each other and exist in a nearly closed small space. Due to the small external atmospheric pressure and alloy liquid static pressure acting on them, when the residual aluminum liquid further cools and contracts, a certain degree of vacuum can be formed, so that the supersaturated hydrogen in the alloy precipitates and forms pinholes.
1.3 Evaluation of Pinhole Degree in Cast Aluminum Alloys
The number and size of holes in the machined surface of cast aluminum alloys within are called the pinhole degree. Pinholes mainly affect the density and mechanical properties of the casting. Therefore, in the production practice of aluminum alloy castings, it is very important to study the influence of porosity grade on mechanical properties and control the pinhole grade to ensure the quality of aluminum alloy castings. According to the “Visual Evaluation Method for Pinhole Degree of Aluminum Alloy Castings”, the pinhole degree is divided into 5 levels, and the reference images are shown in the following table:
Severity | Reference Image | Number and Size of Holes within |
---|---|---|
1 | None | No visible holes on the inspected surface |
2 | Few | Not more than 10, of which 8 are not more than 0.1mm and 2 are not more than 0.2mm |
3 | Moderate | Not more than 15, of which 12 are not more than 0.3mm and 3 are not more than 0.5mm |
4 | Many | Not more than 20, of which 14 are not more than 0.5mm and 6 are not more than 1.0mm |
5 | Severe | Not more than 25, of which 15 are not more than 0.5mm, 7 are not more than 1.0mm, and 3 are not more than 1.5mm |
1.4 Prevention of Pinhole Defects in Cast Aluminum Alloys
1.4.1 Sources and Precipitation of Hydrogen Forming Pinholes
The formation of pores in aluminum alloys is due to the absorption of gas during the melting process of aluminum alloys. The gas sources mainly include refractory materials, metal charge, flux, and tools in contact with the gas. In addition, the chemical bond hydrogen in the newly built furnace lining, furnace refractory materials, and crucibles needs to be released from the binder after several days or weeks of use. The furnace gas composition is determined by the fuel type and air volume. For example, the furnace gas composition of an ordinary gas furnace is mainly CO2, SO2, and H2, while the furnace gas composition of most electric furnaces used by smelting manufacturers is mainly H2. Therefore, the gas absorption amount and porosity degree of aluminum alloys are different when using different smelting furnaces.
In the production practice of aluminum alloys, hydrogen is the main cause of pore formation in aluminum alloys. It is the most harmful gas and has the largest solubility in aluminum alloys. The sources of hydrogen are usually the reaction between aluminum and water vapor, and the water vapor mainly comes from the moisture in the furnace gas, the adsorbed moisture on equipment and tools, the crystal water of some materials, and the moisture decomposed from aluminum rust. Therefore, to solve the problem of pinholes, it is necessary to prevent the aluminum melt from absorbing gas and strengthen the degassing of the aluminum melt.
1.4.2 Main Measures to Prevent the Formation of Pinholes in Aluminum Alloy Castings
- Drying principle: Preheat the furnace charge, melting equipment, and tools. Before use, clean the surface of the crucible, ingot mold, and melting tools, apply protective coatings, and preheat them to remove adsorbed moisture and other chemical substances.
- Rapid melting: Strive to achieve rapid melting during aluminum alloy melting to shorten the residence time at high temperatures and prevent high-temperature gas absorption. Once an abnormality occurs during the production process, contact the on-site technical personnel in time and take decisive measures to deal with it. The maximum alloy temperature generally does not exceed 760°C.
- Refining process: Remove the gas in the aluminum alloy by using a necessary refining process. The main method of degassing is to introduce nitrogen or inert gas into the aluminum alloy to create a large amount of gas. According to the partial pressure principle, the hydrogen atoms dissolved in the aluminum liquid diffuse into the bubbles. When the bubbles float to the surface of the aluminum liquid, they burst and the hydrogen escapes into the atmosphere, achieving the purpose of degassing.
- Mobile adjustable angle degassing machine: Use a mobile adjustable angle degassing machine to refine and degas the aluminum liquid in the holding furnace of the casting machine, which can effectively reduce the gas content and oxide inclusions in the aluminum liquid in the holding furnace of the casting machine and significantly improve the quality of the aluminum alloy cylinder head casting.
- Casting process degassing: Adopt a series of improvement measures for the aluminum alloy cylinder head mold and casting process, such as using the gap of the parting surface or cavity part combination surface for exhaust, opening exhaust grooves, setting exhaust holes and using ejector pins for exhaust, setting exhaust plugs and regularly cleaning and replacing them, increasing the aluminum liquid temperature and low-pressure casting holding pressure to make the bottom pinholes converge at the casting gate and reduce the internal pinholes of the casting. A total of about 20 rounds of process tests were carried out and the reasonable casting process was finally determined.
- Gas drying and filtration: Ensure that the gas in contact with the aluminum alloy liquid surface is dry by using a multi-stage air drying and filtration device. Since the water vapor in the air is an important carrier of hydrogen, an oil-water separator is usually used to remove water vapor in the production process, and a multi-stage filtration device is usually used for gas drying treatment during low-pressure casting. In order to solve the problem of aluminum alloy bottom pinholes, an air drying and filtration device is added outside the workshop building.
2. Conclusion
This article analyzes the main factors of pore formation in aluminum alloy cylinder head castings and takes a series of corresponding preventive measures for the aluminum alloy cylinder head products of the company in actual production. As a result, the bottom pinhole defects of the castings are effectively prevented, high-quality castings are obtained, the casting quality is significantly improved, and the production cost is greatly reduced.