1. Introduction
In the realm of modern manufacturing, the production of complex components like cylinder heads has always been a challenging task. Cylinder heads, being integral parts of internal combustion engines, demand high precision and reliability. The traditional casting methods, while having served the industry for decades, are increasingly facing limitations in meeting the evolving requirements of quality, efficiency, and design flexibility. This has led to the exploration and adoption of innovative technologies, with 3D printing emerging as a game-changer in the field of cylinder head casting production.
1.1 Background of Cylinder Head Casting
Cylinder heads are crucial components that house the combustion chambers and facilitate the intake and exhaust of gases in an engine. Their complex geometries, which include internal passages for coolant and oil, as well as threaded holes and valve seats, make the casting process a complex and intricate operation. The need for high strength, good heat dissipation, and tight tolerances further compounds the manufacturing challenges.
1.2 Challenges in Traditional Casting Methods
Traditional casting techniques for cylinder heads often involve multiple steps, including pattern making, molding, core making, and assembly. These processes are time-consuming and labor-intensive, leading to longer production cycles. Moreover, the need for complex parting lines and the use of multiple cores can result in dimensional inaccuracies and the formation of defects such as porosity and shrinkage cavities. Additionally, any design modifications require significant retooling, increasing costs and production lead times.
1.3 Emergence of 3D Printing in Casting Industry
The advent of 3D printing technology has opened up new possibilities in casting production. By enabling the direct fabrication of complex geometries from digital models, 3D printing offers a more streamlined and flexible approach. In the context of cylinder head casting, it allows for the creation of intricate internal structures and customized designs without the constraints of traditional tooling. This has the potential to not only improve the quality of the final product but also reduce production costs and time-to-market.
2. 3D Printing Technology Overview
2.1 History and Development of 3D Printing
The roots of 3D printing can be traced back to the early concepts of additive manufacturing in the 19th century. However, it was not until the 1980s that the technology began to take shape with the development of the first commercial 3D printers. Since then, continuous advancements in materials, hardware, and software have expanded the capabilities and applications of 3D printing across various industries.
2.2 Working Principles of 3D Printing
3D printing operates on the principle of additive manufacturing, where objects are built layer by layer. In the case of casting applications, powder-based materials such as metal or sand are used. The process begins with spreading a thin layer of powder on a build platform. A binder, which can be a liquid adhesive or a reactive agent, is then selectively deposited onto the powder bed according to the digital model. This causes the powder particles to bond together, forming a solid layer. The build platform is then lowered, and a new layer of powder is spread and bonded, repeating the process until the entire object is complete.
2.3 Types of 3D Printing Technologies in Casting
- Binder Jetting: This is the most commonly used 3D printing technology in casting. It offers high resolution and the ability to print complex geometries. In binder jetting, a liquid binder is jetted onto a powder bed to selectively bond the powder particles, creating the desired shape. The unbound powder can be easily removed after printing, leaving behind a solid object.
- Selective Laser Sintering (SLS): SLS uses a high-power laser to sinter powdered materials, typically polymers or metals, into a solid structure. The laser selectively fuses the powder particles by heating them above their melting point. This process allows for the production of strong and durable parts with good mechanical properties.
- Direct Metal Laser Sintering (DMLS): A variation of SLS, DMLS is specifically designed for printing metal parts. It enables the fabrication of high-quality metal components with complex geometries and excellent mechanical properties. DMLS is widely used in the aerospace, automotive, and medical industries.
2.4 Materials Used in 3D Printing for Casting
- Sand: For casting applications, silica sand is a commonly used material in 3D printing. It provides good dimensional stability and can withstand the high temperatures of the casting process. Coated sands, which have a resin binder applied to the surface, offer improved strength and surface finish.
- Metal Powders: Various metal powders, such as aluminum, titanium, and steel, are used in 3D printing for casting metal parts. These powders are carefully formulated to ensure proper sintering and mechanical properties. Alloy powders can also be used to achieve specific material characteristics, such as increased strength or corrosion resistance.
2.5 Advantages and Limitations of 3D Printing in Casting
- Advantages:
- Design Freedom: 3D printing allows for the creation of highly complex geometries that are difficult or impossible to achieve with traditional casting methods. This enables the optimization of component performance, such as improved coolant flow in cylinder heads.
- Reduced Lead Times: By eliminating the need for tooling and reducing the number of manufacturing steps, 3D printing can significantly shorten production cycles. This is especially beneficial for prototyping and small-batch production.
- Cost Savings: In certain cases, 3D printing can reduce costs by eliminating the need for expensive molds and tooling. It also minimizes material waste, as only the required amount of powder is used.
- Customization: The ability to easily modify digital models makes 3D printing ideal for producing customized cylinder heads to meet specific customer requirements.
- Limitations:
- High Equipment Cost: The initial investment in 3D printing equipment can be substantial, which may be a barrier for small and medium-sized enterprises.
- Limited Build Volume: The size of the parts that can be printed is currently limited by the build volume of the 3D printer. This restricts the application of 3D printing for large cylinder heads.
- Post-Processing Requirements: Printed parts often require post-processing, such as sintering, infiltration, or machining, to achieve the desired mechanical properties and surface finish. This adds additional time and cost to the production process.
3. 3D Printing in Cylinder Head Casting Production: A Case Study
3.1 Product Information and Requirements
- Cylinder Head Specifications: The cylinder head in question has dimensions of 615 mm × 420 mm × 290 mm, with a minimum wall thickness ranging from 8 to 10 mm and local thicker sections. It is made of RuT350, a nodular cast iron known for its good strength and heat resistance.
- Complex Internal Structures: The internal structure of the cylinder head is highly intricate, featuring coolant passages, oil galleries, and valve seats. These structures require precise manufacturing to ensure proper engine performance.
3.2 3D Printing Production Process
3.2.1 Scheme Planning
- Flexibility in Process Design: The 3DP (Three-Dimensional Printing) process offers the advantage of not being constrained by traditional casting considerations such as parting and draft angles. This allows for greater flexibility in designing the casting process. Multiple possible process schemes can be evaluated, taking into account factors such as the product’s structural characteristics and casting requirements.
- Selection of Optimal Pouring System: Through detailed casting process analysis and the use of three-dimensional drawing software, a digital model of the casting is created. Different pouring system designs are simulated and compared to determine the most suitable option. In this case, a top gating system was chosen due to its advantages in providing smooth filling, facilitating feeding, and ease of operation.
3.2.2 Virtual Design
- Simulation and Optimization: Using advanced simulation software like Magma and ProCAST, the flow and temperature fields during the filling and solidification of the casting are analyzed. This enables the optimization of the pouring system and the determination of the final feeding scheme. Key casting process parameters, such as the ratio of the gating system and the flow velocity at the ingate, are calculated and adjusted based on the simulation results. The three-dimensional casting process drawing is then completed, and the analysis results are used to validate and further improve the casting process.
3.2.3 Sand Mold Design and Printing
- Integration of Complex Structures: The three-dimensional drawing software is utilized to design the sand mold, taking into account the characteristics of the 3D printing technology, the printing range of the equipment, and the product structure. The goal is to minimize the number of sand cores while ensuring proper moldability and cleanability. The cylinder head casting and its gating and riser system can be formed by three 3D printed sand molds, which are assembled to create a complete mold.
- Printing and Surface Treatment: The designed sand cores are produced using 3D printing. After printing, the surface loose sand is removed, and the sand core surface is coated with a water-based coating with a Baume degree of 42 – 44. The coated sand cores are then dried in a drying kiln at approximately 140 °C. Once dried and inspected for quality, the sand cores are assembled for casting. For relatively small cylinder head castings (< 1000 kg), direct screw clamping of the sand mold can be used for casting without the need for a flask.
3.2.4 Casting and Cleaning
- Pouring and Cooling: After assembly, the mold is ready for pouring. The molten metal is poured into the mold, and the casting is allowed to cool. The cooling time is carefully controlled to ensure proper solidification and minimize the formation of defects.
- Cleaning and Finishing: Once cooled, the casting is removed from the mold (knocked out). The resulting casting has a complete shape, clear contours, and minimal flash. It is then subjected to shot blasting to remove surface impurities and a small amount of precision chiseling to achieve the final dimensions and surface finish.
3.3 Quality and Performance Evaluation
- Dimensional Accuracy: The use of 3D printing significantly improves the dimensional accuracy of the cylinder head casting. Compared to traditional casting methods, the dimensional error is reduced by over 75%, ensuring a better fit and performance of the component in the engine assembly.
- Surface Quality: The printed sand molds result in a smoother surface finish of the casting, reducing the need for extensive machining and finishing operations. This not only saves time and cost but also improves the overall quality of the part.
- Internal Structure Integrity: The simulation and optimization of the casting process using 3D printing techniques ensure that the internal structures, such as coolant passages and valve seats, are free from defects and have the correct dimensions. This is crucial for the proper functioning of the cylinder head in the engine.
3.4 Comparison with Traditional Casting Methods
- Production Cycle: Traditional casting methods for cylinder heads involve a series of time-consuming steps, including pattern making, molding, core making, and assembly. The overall production cycle can take up to 60 days. In contrast, the 3D printing production process, which mainly consists of sand core printing and assembly pouring, can significantly reduce the production time to just 7 days.
- Labor Intensity and Skill Requirements: Traditional casting requires a high level of manual labor and skilled workers for tasks such as mold making and core assembly. 3D printing reduces the need for extensive manual intervention, lowering the labor intensity and skill requirements. This makes the production process more accessible and less dependent on highly skilled labor.
- Material Usage and Waste: Traditional casting often results in a significant amount of material waste due to the need for parting lines and the complexity of the mold. 3D printing, on the other hand, uses only the required amount of powder material, minimizing waste and reducing material costs.
- Product Quality and Consistency: The precision and repeatability of 3D printing ensure a higher level of product quality and consistency compared to traditional casting methods. The reduced number of sand cores and the elimination of parting lines result in fewer defects and better dimensional accuracy.
4. Benefits and Implications of 3D Printing in Cylinder Head Casting
4.1 Enhanced Design Capabilities
- Complex Geometries and Internal Structures: 3D printing enables the creation of highly complex geometries and internal structures that are not possible with traditional casting methods. This allows for the optimization of fluid flow, heat transfer, and mechanical performance in cylinder heads. For example, intricate coolant passages can be designed to improve engine cooling efficiency, leading to better overall engine performance and reliability.
- Design Iteration and Customization: The digital nature of 3D printing makes it easy to modify and iterate designs. This is especially beneficial for cylinder head manufacturers who need to customize products for different engine applications or customer requirements. Customized cylinder heads can be designed and produced quickly, reducing the time and cost associated with traditional design changes.
4.2 Improved Production Efficiency
- Reduced Lead Times: The streamlined production process of 3D printing, which eliminates the need for tooling and reduces the number of manufacturing steps, significantly shortens the production lead time. This enables faster prototyping and product development, allowing manufacturers to respond more quickly to market demands.
- Increased Productivity: With the ability to print multiple sand cores simultaneously and the reduced need for manual labor in certain production steps, 3D printing can increase overall productivity. This is particularly advantageous for high-volume production of cylinder heads, where small improvements in productivity can have a significant impact on overall output.
4.3 Cost Savings
- Tooling and Equipment Costs: Traditional casting requires the production of expensive molds and tooling, which can be a significant investment. 3D printing eliminates the need for these traditional tooling, reducing the initial capital investment. Although the cost of 3D printing equipment is relatively high, the long-term savings in tooling costs can make it a more cost-effective option, especially for small and medium-sized production runs.
- Material and Labor Costs: The reduction in material waste and the lower labor requirements in 3D printing contribute to cost savings. By using only the necessary amount of powder material, manufacturers can reduce material costs. Additionally, the decreased need for skilled labor in certain production steps can lower labor costs and make the production process more efficient.
4.4 Quality and Performance Improvements
- Dimensional Accuracy and Consistency: The high precision of 3D printing ensures excellent dimensional accuracy and consistency in cylinder head castings. This results in better fit and assembly with other engine components, reducing the need for post-machining and improving overall engine performance. The consistent quality of printed parts also leads to fewer rejects and higher overall product quality.
- Mechanical Properties: The ability to control the microstructure and density of printed parts can lead to improved mechanical properties. In the case of cylinder heads, this can result in increased strength, better heat resistance, and enhanced durability, ensuring reliable engine operation under various conditions.
4.5 Environmental Sustainability
- Reduced Material Waste: Traditional casting methods often generate a significant amount of waste material due to the need for machining and the limitations of traditional mold-making processes. 3D printing minimizes material waste by using only the required amount of powder, reducing the environmental impact associated with material disposal.
- Energy Efficiency: The additive manufacturing process of 3D printing can be more energy-efficient compared to traditional casting, which often requires large amounts of energy for melting and pouring metal. The reduction in energy consumption contributes to a lower carbon footprint and a more sustainable manufacturing process.
5. Challenges and Future Perspectives
5.1 Current Challenges in 3D Printing for Cylinder Head Casting
- Equipment and Material Costs: The high cost of 3D printing equipment and specialized materials remains a significant barrier to widespread adoption. This limits the access of small and medium-sized enterprises to this technology, despite its potential benefits.
- Limited Build Volume and Speed: The current limitations in build volume and printing speed of 3D printers restrict the production of large-sized cylinder heads and can lead to longer production times for high-volume production. Overcoming these limitations is crucial for the technology to be more widely applicable in the automotive and other industries.
- Post-Processing Requirements: Printed parts often require extensive post-processing, such as sintering, infiltration, and machining, to achieve the desired mechanical properties and surface finish. These additional steps add complexity and cost to the production process and need to be optimized to make 3D printing more competitive with traditional casting methods.
- Quality Control and Standardization: Ensuring consistent quality and reliability of 3D printed cylinder heads is a challenge. The lack of standardized testing and quality control procedures for 3D printed parts makes it difficult to meet the strict requirements of the automotive industry. Developing robust quality control methods and industry standards is essential for the wider acceptance of 3D printed components.
5.2 Research and Development Trends
- Advanced Materials: Ongoing research is focused on developing new materials with improved properties for 3D printing. This includes the development of high-strength alloys, heat-resistant materials, and composite powders that can better meet the demanding requirements of cylinder head applications. The goal is to enhance the mechanical and thermal performance of printed parts without sacrificing manufacturability.
- Multi-Material Printing: The ability to print multiple materials in a single part is an area of active research. This would enable the integration of different functional materials in cylinder heads, such as wear-resistant coatings for valve seats or heat-conductive materials for improved heat dissipation. Multi-material printing could further optimize the performance and durability of cylinder head components.
- Process Optimization and Automation: Research efforts are directed towards optimizing the 3D printing process to increase printing speed, improve dimensional accuracy, and reduce post-processing requirements. Automation of the entire production process, from design to post-processing, is also being explored to enhance productivity and reduce human error. This includes the development of intelligent software for process control and optimization.
5.3 Future Outlook and Potential Impact on the Casting Industry
- Widespread Adoption and Industry Transformation: As the technology continues to mature and costs decrease, 3D printing is expected to be more widely adopted in the casting industry. This will lead to a significant transformation of traditional casting processes, with increased design flexibility, shorter production cycles, and improved product quality. The automotive, aerospace, and other industries that rely heavily on high-quality castings will be among the first to benefit from this technological shift.
- New Business Models and Supply Chain Dynamics: The rise of 3D printing in casting may give birth to new business models, such as on-demand manufacturing and distributed production. Manufacturers may be able to produce customized cylinder heads closer to the point of use, reducing inventory costs and supply chain complexity. Additionally, the ability to share digital designs and collaborate more easily in the 3D printing ecosystem could lead to new partnerships and business opportunities.
- Skills and Workforce Requirements: The increasing use of 3D printing in casting will require a new set of skills in the workforce. Workers will need to be proficient in digital design software, 3D printing operation and maintenance, and post-processing techniques. Training programs and educational curricula will need to be updated to equip the workforce with these new skills. Additionally, there will be a growing demand for engineers and technicians who can optimize 3D printing processes for casting applications, ensuring high-quality and efficient production.
- The traditional skills of pattern makers and mold makers may become less in demand, but their expertise in casting principles and materials could be valuable in the design and optimization of 3D printed molds and cores. The workforce will also need to adapt to the more automated and data-driven nature of 3D printing production. This includes understanding how to monitor and control the printing process using sensors and data analytics to ensure consistent quality.
- In conclusion, 3D printing has the potential to revolutionize the production of cylinder heads and the casting industry as a whole. While there are still challenges to overcome, the future looks promising with continued research and development efforts. As the technology advances and becomes more accessible, it will bring about significant improvements in product quality, production efficiency, and cost savings, ultimately benefiting the automotive and other industries that rely on these critical components. The transformation will not only be technological but also impact business models, supply chains, and the skills required of the workforce. It is an exciting time for the casting industry as it embraces this new era of additive manufacturing.
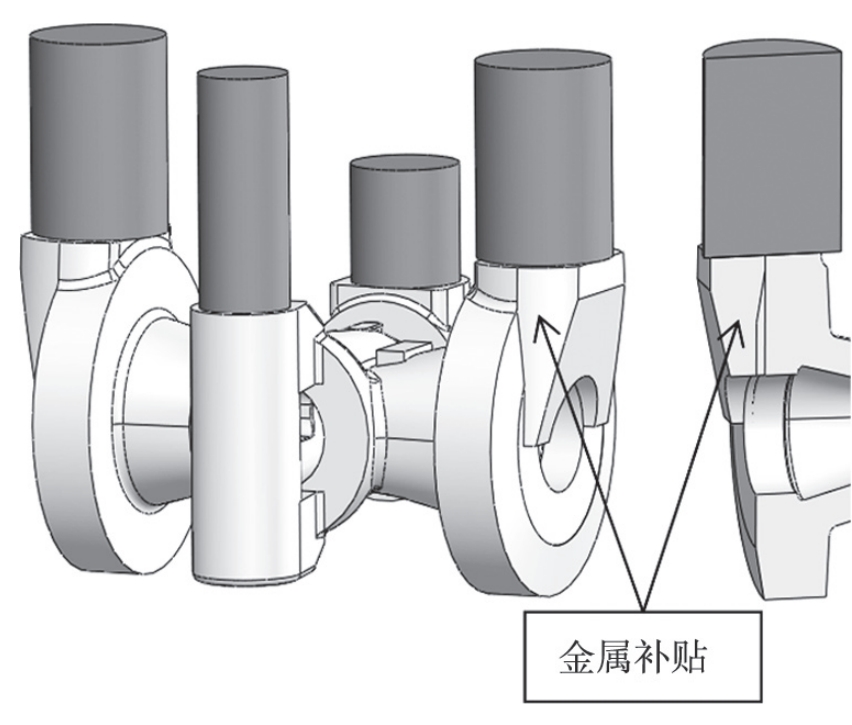