1. Analysis of saddle structure
Taking the thin-walled saddle as the research object, the three-dimensional model is shown in Figure 1. The overall dimensions are 755 mmx580 mmx322 mm, with an average late thickness of 10 mm and a maximum wall thickness of 30 mm. The overall gross defect mass of the casting is about 63 kg, and the finished product mass is 60.3 kg. Its structure is symmetrically distributed. The saddle material is OT700-6. Except for Fe, the rest are made of CSi Mn, SP_ Mg_ The composition of elements such as Ce. Cr. Cu. Mo, and the mass percentage of each chemical element are shown in Table 1. The liquidus temperature of OT 700 is 1186 C, and the solidus temperature is 1149 C.
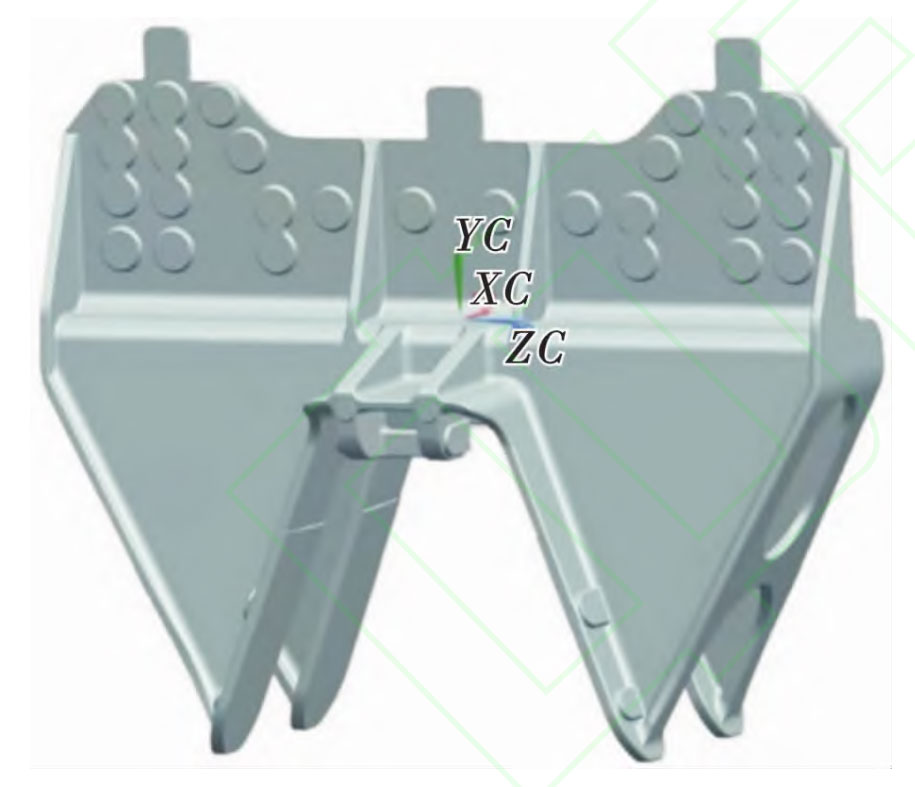
C | Si | Mn | S | P | Mg | Cu | Mo | Ce | Cr |
3.5 | 1.9 | 0.4 | 0.01 | 0.05 | 0.035 | 0.5 | 0.15 | 0.006 | 0.1 |
2. Initial Process Plan
The saddle studied in this article is a large thin-walled casting, which is difficult to place a riser. Therefore, a non riser pouring process is adopted. Due to the complex structure of the saddle, considering the principles of smooth filling process and sequential solidification, the injection method is mainly based on bottom injection and also includes layered injection. The casting adopts a closed gating system, and the cross-sectional ratio of each component in the gating system is selected to be 1.90:1.65:1.00 in Zu: Z, with a gating time of 14 seconds and an inner gate with a flow resistance section. To ensure rapid filling of the metal cavity and achieve balanced solidification, 6 internal gates, 1 circular transverse gate, and 1 vertical gate are set up. Due to the large size and large exhaust volume of the saddle, this article chooses exhaust holes as the exhaust channel. Three exhaust holes are designed on the casting cavity, and four exhaust holes are designed at the edge of the sand core, which can effectively reduce the occurrence of porosity defects. The three-dimensional model of the pouring system is shown in Figure 2.

3. Setting of initial scheme preprocessing parameters
Convert the 3D models of the gating system and castings into. stl format, and then perform mesh generation and parameter settings in the Anycasting software AnyPRE module. To ensure computational accuracy, a non-uniform and grid format is used, generating approximately 25 million grids. Based on actual production experience, it is planned to set the process parameters, with a pouring temperature of 1380-1390 C. As the saddle is a thin-walled component, the pouring speed should not be set too slowly, with an initial setting of 0.4 m/s. The initial temperature of the mold and sand is set to 25 “C, and the interfacial heat transfer coefficient between the casting and the mold is a variable. The values are shown in Table 2. The interfacial heat transfer coefficient between the molten metal, mold, core, and air is 41.87 W/(m -. K). The heat dissipation method is air cooling.
Temperature/° C | 1 | 600 | 1149 | 1186 |
Heat transfer coefficient/(W/m ^ -2K ^ 3) | 300 | 500 | 600 | 800 |