As shown in the figure, the steel casting after riser removal and the casting before delivery are shown. This steel casting has only undergone shot blasting treatment. From the perspective of appearance, through process improvement and the application of 3D sand molding technology, the heat dissipation rib plate of the steel casting is well formed, and the rib plate is formed in one time without any cracks, with uniform wall thickness, and without defects. At the same time, the overall size of the steel casting is well controlled, and the parting surface cracks are small, greatly reducing the workload of later cleaning.
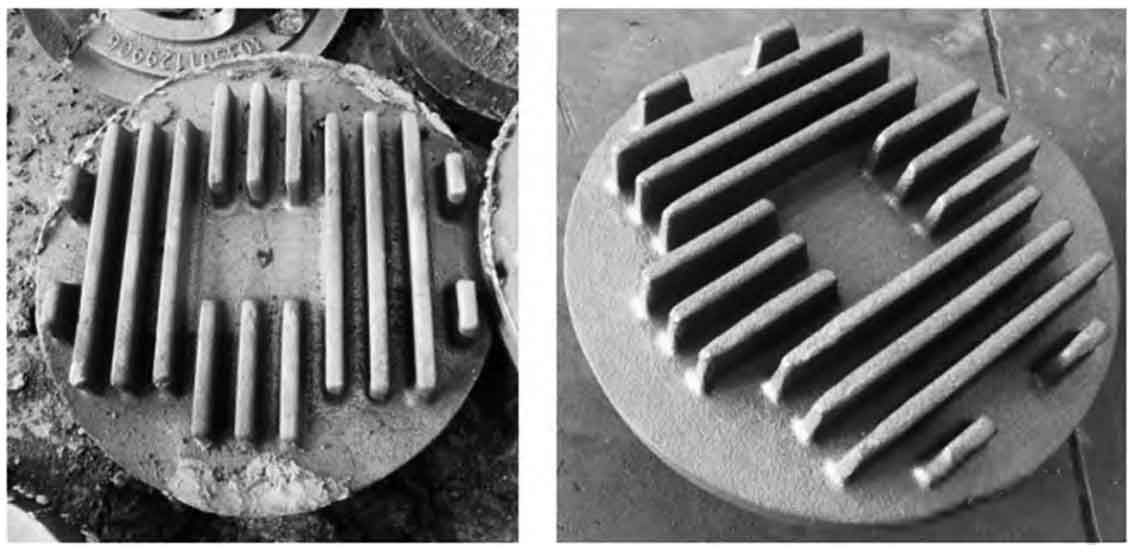
Upon inspection, the internal quality of the steel castings meets the customer’s non-destructive testing requirements, and the chemical composition and mechanical properties meet the customer’s specifications. During the subsequent cleaning, the steel castings have few cracks, and the internal parts of the product are free of shrinkage cavities and porosity. The mechanical properties are excellent, and the product has passed the production verification.
Through the analysis of the product structure and the auxiliary simulation of CAE simulation software, while fully utilizing the advantages of 3D printing technology, selecting reasonable product pouring positions, parting surfaces, sand mold parting methods, and pouring temperatures, the rib plates and important structures of the product are all in the same sand mold, with simple production process operation, stable size, and good appearance quality assurance. After production verification, this product has passed the first production and met customer requirements in all aspects. The surface of the product has small seams, excellent rib plate molding, and no defects such as cold shuts and lack of flesh. At the same time, it also effectively ensures the appearance quality of steel castings, reduces cleaning workload, greatly saves production costs, and greatly improves the quality of steel castings.