Introduction
Vermicular graphite cast iron (VGI), known for its unique properties, is increasingly used in automotive industries, especially in manufacturing cylinder blocks. With improved tensile strength, elasticity, and fatigue resistance compared to traditional gray cast iron, graphite cast iron is favored for producing heavy-duty components in both passenger and commercial vehicles. This paper aims to explore the production process, mechanical properties, and technological innovations applied in the production of a 16L vermicular graphite cast iron cylinder block.
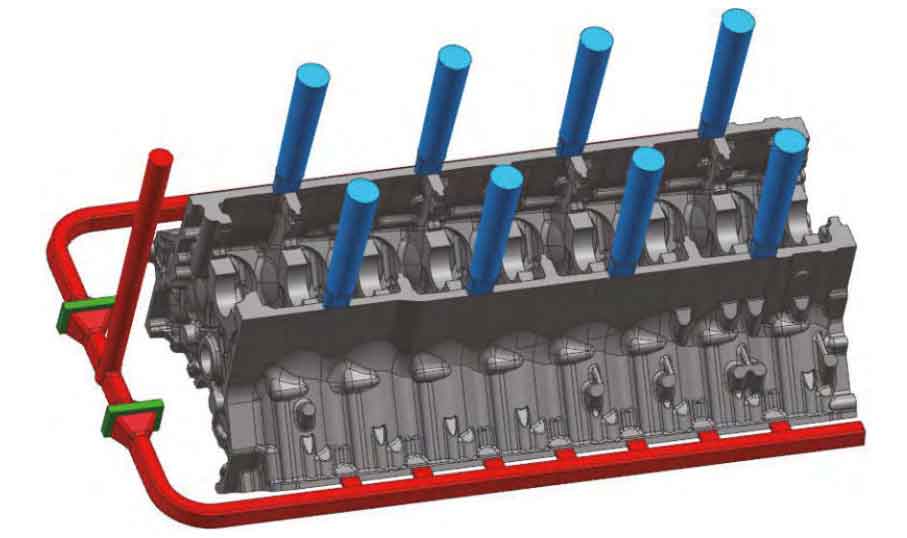
1. Chemical Composition Control
Chemical composition is a critical factor in the production of graphite cast iron cylinder blocks. Proper control ensures that the mechanical properties meet the required specifications. The essential elements in graphite cast iron and their controlled values are summarized in Table 1.
Table 1: Chemical Composition Requirements for Graphite Cast Iron Cylinder Block
Element | Value (%) |
---|---|
Carbon (C) | 3.7 – 3.9 |
Silicon (Si) | 1.9 – 2.1 |
Manganese (Mn) | 0.2 – 0.4 |
Phosphorus (P) | ≤ 0.03 |
Sulfur (S) | 0.01 – 0.02 |
Chromium (Cr) | ≤ 0.08 |
Copper (Cu) | 1.2 – 1.3 |
Tin (Sn) | 0.09 – 0.11 |
Proper levels of carbon and silicon help prevent defects such as shrinkage or white spots. Silicon content must be carefully regulated, as excessive silicon leads to an increase in graphite balls, while low silicon content makes machining difficult. Manganese and copper are essential for improving hardness, while sulfur and phosphorus contents are minimized to prevent negative effects on casting properties.
2. Melting Process
The melting process involves using an intermediate frequency furnace to heat iron liquid to a temperature between 1540°C and 1550°C. The furnace charge includes 20-30% recycled material mixed with 70-80% packed scrap steel. The packed steel must have stable chemical composition, low sulfur content, and consistent size to ensure homogeneity. Table 2 provides details of furnace charge composition.
Table 2: Furnace Charge Composition
Material | Percentage (%) |
---|---|
Recycled material | 20 – 30 |
Packed scrap steel | 70 – 80 |
A high-temperature graphitized carburant with low sulfur content (less than 0.03%) is used, along with silicon carbide for pretreatment. These materials increase nucleation capacity and ensure high purity.
3. Vermicularization and Inoculation Treatment
After melting, the iron liquid is subjected to a vermicularization and inoculation treatment to achieve the desired vermicular graphite structure. The vermicularizing treatment is performed at a temperature between 1480°C and 1490°C, followed by automatic inoculation. The temperature control and addition of magnesium are critical for maintaining high vermicularity rates, as summarized in Table 3.
Table 3: Treatment Parameters for Vermicularization
Parameter | Value |
---|---|
Vermicularization temperature | 1480°C – 1490°C |
Inoculation temperature | 1420°C – 1440°C |
Magnesium content | 0.015% – 0.02% |
4. Mechanical Properties of Graphite Cast Iron Cylinder Block
To ensure the high quality of the graphite cast iron cylinder block, various mechanical properties such as tensile strength, hardness, and vermicularity are tested. The results of these tests are shown in Table 4.
Table 4: Mechanical Properties of Graphite Cast Iron Cylinder Block
Property | Value |
---|---|
Tensile strength | ≥ 420 MPa |
Hardness | 230 – 260 HBW |
Vermicularity | ≥ 80% |
Typical metallurgical structures are also analyzed to evaluate the microstructure of the cylinder block. The figures below depict the vermicular graphite iron structures at different vermicularity rates.
5. Shrinkage and Porosity Control
Shrinkage and porosity are common issues encountered during the casting of graphite cast iron components. Initial trials revealed shrinkage defects near the oil channels (Figure 3). Through optimizing the carbon content and increasing carbon equivalent levels, these defects were significantly reduced. Maintaining a carbon equivalent between 4.45% and 4.55% and adding a carburant based on furnace holding time helped mitigate shrinkage.
6. Conclusion
In summary, the production process of a 16L vermicular graphite iron cylinder block involves precise chemical control, careful melting and treatment procedures, and diligent mechanical testing to ensure optimal performance. The vermicular graphite structure enhances the strength and durability of the cylinder block, making it ideal for high-performance applications in automotive engines.