After determining the optimal process parameter group, reset the process parameters according to the optimized process for numerical simulation. The optimized results of shrinkage porosity and porosity are compared with the results of traditional schemes, as shown in Figure 1. From the figure, it can be seen that the maximum shrinkage porosity after optimizing the pouring system and adjusting process parameters is 2.29%.
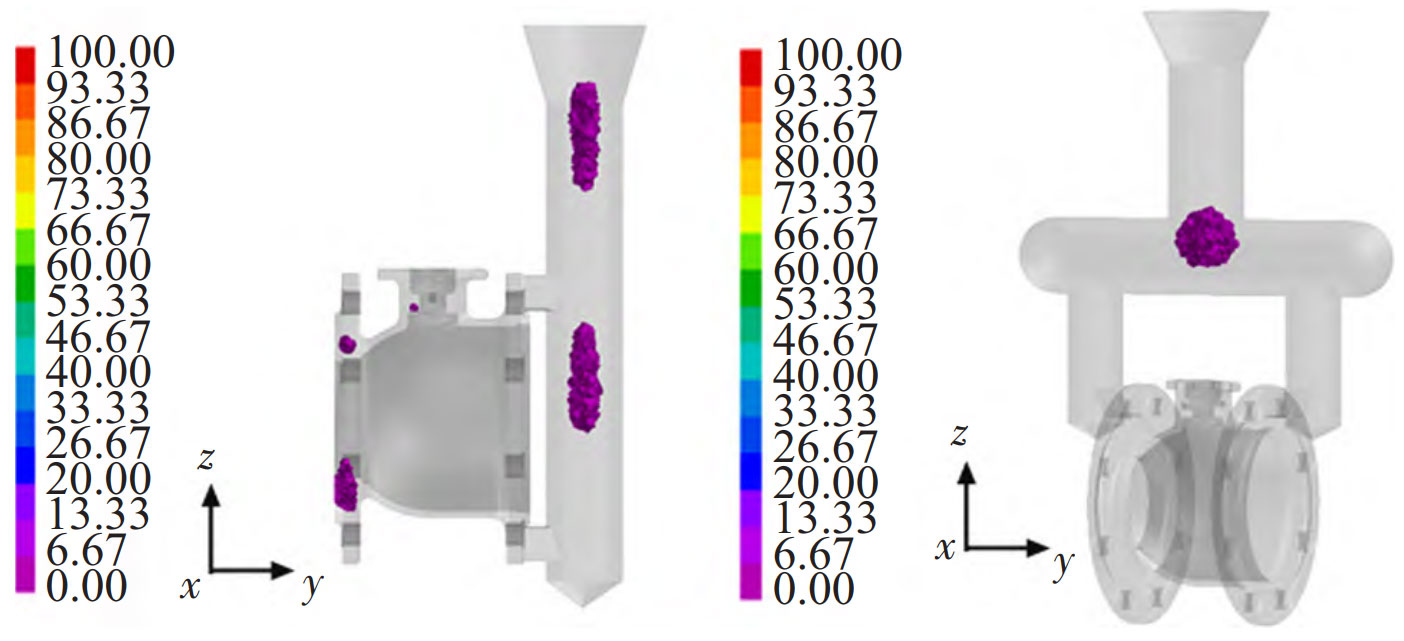
Figure 2 shows the 304 stainless steel ball valve investment casting produced using the optimized plan. After inspection, the shrinkage defects at the corners of the ball valve body and flange have disappeared, and the overall molding quality of the investment casting is good.

(1) ProCAST software was used for numerical simulation of investment casting, and shrinkage porosity and porosity analysis was conducted on 304 stainless steel ball valve parts. The results show that under traditional molding conditions, the shrinkage and porosity of investment castings are more severe, and the shrinkage cavities at the outer wall of the valve body and flange corners seriously affect the molding quality.
(2) By analyzing the shrinkage problem of investment castings under traditional processes, the cause of shrinkage was identified. The structure and size of the pouring system were changed to optimize the investment casting of the ball valve, and the optimization effect was obvious. At the same time, an orthogonal experiment was designed to adjust the process parameters, and a set of process parameters suitable for the pouring system was found, namely, the pouring temperature of 1550 ℃, the pouring speed of 1.0 kg/s, and the shell preheating temperature of 1150 ℃. Under these process parameters, the maximum shrinkage porosity of the investment casting was 2.29%. After actual production verification, the defects at the outer wall of the ball valve body and the flange corner have disappeared.