Abstract
With the growing global demand for mineral resources, enhancing the performance of ore crushers has become a critical focus in mining and metallurgical industries. Gyratory crushers, as primary crushing equipment, play a pivotal role in processing hard ores. The wear-resistant lining plate, a core component directly interacting with ores, significantly impacts crushing efficiency, operational costs, and equipment longevity. This paper reviews recent advancements in wear-resistant lining plate materials, cavity optimization techniques, and the integration of intelligent technologies. Key topics include alloy design, heat treatment, surface engineering, discrete element method (DEM) simulations, and sensor-based wear monitoring. By synthesizing global research, this article aims to provide actionable insights for improving crusher performance and durability.
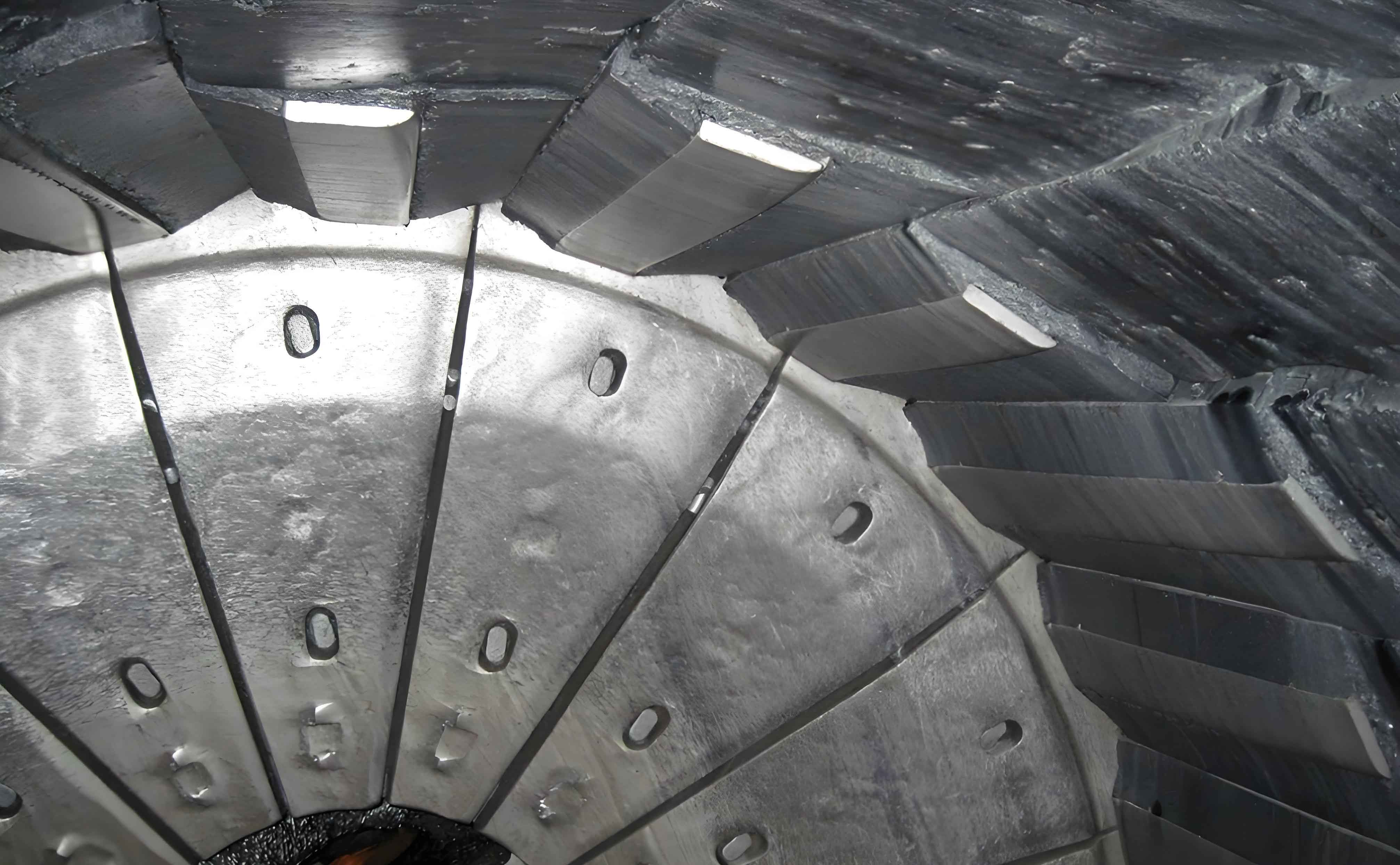
1. Introduction
The mining industry faces escalating challenges in balancing productivity, cost-efficiency, and sustainability. Copper ore, a cornerstone of industrial applications, requires efficient crushing to meet downstream processing demands. Gyratory crushers, characterized by high throughput and large feed openings, are indispensable for primary ore reduction. However, severe wear of the wear-resistant lining plate—comprising the fixed concave (mantle) and moving cone (concave)—remains a persistent issue. Frequent replacements due to wear disrupt production, incurring downtime and maintenance costs.
This article explores cutting-edge solutions to enhance the wear resistance of lining plates and optimize crusher cavities. By integrating material science innovations, computational modeling, and smart technologies, we aim to address these challenges systematically.
2. Working Conditions and Wear Mechanisms of Wear-Resistant Lining Plates
2.1 Structure of Gyratory Crushers
A gyratory crusher consists of an eccentrically rotating cone (mantle) and a stationary concave. The crushing cavity formed between these components subjects ores to compressive forces, fracturing them into smaller fragments. The wear-resistant lining plate, affixed to both cones, endures abrasive, impact, and fatigue wear during operation.
2.2 Wear Mechanisms
Wear mechanisms affecting wear-resistant lining plates include:
- Abrasive Wear: Dominant mechanism caused by hard ore particles sliding or embedding into the plate surface.
- Impact Wear: High-stress collisions between ores and plates.
- Fatigue Wear: Cyclic loading leading to crack propagation.
- Corrosion Wear: Chemical reactions in humid or acidic environments.
Plastic Deformation Wear is identified as the primary failure mode. Under compressive stress, ore particles induce repeated plastic deformation, forming micro-cracks and eventual material spalling.
3. Material Optimization for Wear-Resistant Lining Plates
3.1 High Manganese Steel (HMS)
HMS remains the most widely used material due to its exceptional work-hardening capability. Under impact, the surface hardens while retaining ductility. However, its performance declines under low-stress conditions.
3.1.1 Compositional Adjustments
- Carbon (C) and Manganese (Mn):
- Increasing C content enhances hardness but reduces ductility.
- Mn stabilizes austenite, improving toughness and work-hardening capacity.
- Ultra-high Mn steels (e.g., Mn > 18%) exhibit superior wear resistance.
Table 1: Effect of Mn and C on HMS Properties
Parameter | High C (>1.2%) | High Mn (>18%) |
---|---|---|
Hardness | Increased | Moderate |
Ductility | Reduced | Improved |
Wear Resistance | Moderate | High |
3.1.2 Alloying Elements
- Ti, V, Nb: Form hard carbides (TiC, V2C, NbC) to inhibit micro-cutting.
- Cerium (Ce): Enhances grain refinement and fatigue resistance.
Equation 1: Carbide formation in alloyed HMS
Fe+Ti+C→TiC+Austenite MatrixFe+Ti+C→TiC+Austenite Matrix
3.1.3 Heat Treatment
- Solution Treatment: 1050–1100°C for carbide dissolution.
- Quenching: Rapid cooling to retain austenitic structure.
- Aging: 250–450°C to precipitate secondary carbides.
3.1.4 Surface Engineering
- Shot Peening: Introduces compressive stress, refining surface grains to nano-scale.
- Laser Cladding: Deposits Fe-WC coatings to enhance hardness .
3.2 Low-Alloy Wear-Resistant Steels
Low-alloy steels (Table 2) combine high hardness (HRC 50–55) with moderate toughness, outperforming HMS under low-impact conditions.
Table 2: Typical Low-Alloy Wear-Resistant Steels
Alloy System | Key Elements | Hardness (HRC) | Application |
---|---|---|---|
Cr-Si-Mo | Cr: 3.8–4.2%, Mo: 0.9–1.1% | 50–55 | Non-host machinery |
Cr-Mn-Si-Mo-V | V: 0.04–0.3% | 50–55 | Mining components |
Si-Mn-Mo-B-Re | Re: 0.04–0.15% | 55 | Drill bits |
3.2.1 Heat Treatment Optimization
- Quenching: 860–980°C followed by water or brine cooling.
- Tempering: 200–250°C to balance hardness and toughness.
Equation 2: Hardness vs. Tempering Temperature
H=H0−k⋅TH=H0−k⋅T
Where H0H0 = initial hardness, kk = material constant, TT = tempering temperature.
3.3 Emerging Materials
- Metal Matrix Composites (MMCs): TiC- or WC-reinforced steels show promise but require improved toughness.
- Nacre-Inspired Composites: Bio-mimetic designs combining ceramic layers with ductile matrices.
4. Cavity Optimization Techniques
4.1 Geometric Analysis
Cavity shape directly influences ore flow, wear distribution, and product size. Optimization methods include:
Table 3: Cavity Optimization Approaches
Method | Description | Advantages | Limitations |
---|---|---|---|
Geometric Modeling | Multi-segment curve fitting | Cost-effective | Limited real-world data |
DEM Simulation | Particle-level dynamics analysis | High accuracy | Computational cost |
Industrial Trials | Field measurements and adjustments | Real-world validation | Time-consuming |
4.1.1 DEM-Based Simulations
Discrete Element Method (DEM) models predict ore motion and wear patterns . For example, optimizing the mantle’s spherical protrusions increased throughput by 20%.
Equation 3: DEM force calculation
Fij=knδn+γnvn+ktδt+γtvtFij=knδn+γnvn+ktδt+γtvt
Where kn,ktkn,kt = normal/tangential stiffness, γn,γtγn,γt = damping coefficients.
4.2 Intelligent Wear Monitoring
- 3D Laser Scanning: Captures real-time lining plate thickness.
- Ultrasonic Sensors: Detect subsurface cracks.
- AI Algorithms: Predict wear rates using historical data.
5. Conclusion and Future Perspectives
The optimization of wear-resistant lining plates and crusher cavities is pivotal for sustainable mining operations. Key advancements include:
- Material Innovations: Alloy design and surface engineering to enhance wear resistance.
- Cavity Design: DEM simulations and geometric modeling for efficient ore flow.
- Smart Technologies: Real-time wear monitoring and predictive maintenance.
Future research should focus on:
- Developing tougher MMCs for high-impact environments.
- Integrating digital twins for real-time crusher optimization.
- Expanding AI-driven wear prediction models.
By embracing these strategies, the mining industry can achieve higher productivity, reduced downtime, and lower environmental impact.