Steel castings manufacturers play a crucial role in meeting industry demands by incorporating quality assurance practices and embracing innovation. Here are some ways in which steel castings manufacturers ensure the highest quality and stay at the forefront of the industry:
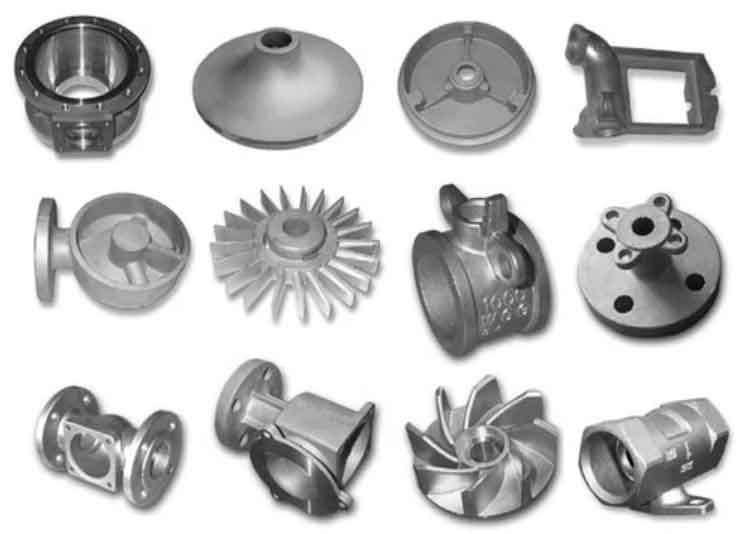
- Advanced Technology and Equipment: Leading steel castings manufacturers invest in state-of-the-art technology and modern equipment for various stages of the manufacturing process. This includes advanced simulation software for mold filling analysis, automated molding machines, and sophisticated non-destructive testing equipment for quality inspection.
- Quality Management Systems: Implementing robust quality management systems, such as ISO 9001, ensures that the manufacturing process adheres to strict quality standards. These systems cover every stage, from raw material selection to final inspection, and help identify and address any issues in real-time.
- Metallurgical Expertise: Manufacturers employ metallurgical experts who possess in-depth knowledge of steel properties and the behavior of various steel alloys. This expertise allows them to recommend the most suitable steel grade for each specific application, optimizing the final product’s performance.
- Testing and Inspection: Steel castings manufacturers conduct extensive testing and inspection procedures to verify the integrity and quality of each casting. Non-destructive testing methods, such as ultrasonic testing, X-ray examination, and magnetic particle inspection, are commonly employed to detect any internal defects.
- Continuous Improvement: Embracing a culture of continuous improvement is crucial for steel castings manufacturers. They regularly assess their processes, identify areas for enhancement, and implement new techniques and technologies to enhance productivity, efficiency, and overall quality.
- Research and Development: Leading manufacturers invest in research and development to explore innovative casting techniques, materials, and process optimization. This enables them to develop new solutions, reduce production costs, and enhance the mechanical properties of the castings.
- Collaboration with Customers: Working closely with customers is essential to understand their specific needs and requirements. Manufacturers collaborate with their clients to design tailor-made steel castings that meet precise specifications and perform optimally in the intended applications.
- Sustainability Initiatives: Many steel castings manufacturers focus on sustainable practices, such as recycling and reducing energy consumption. They also explore eco-friendly alternatives for the manufacturing process, making them more environmentally responsible.
- Certifications and Compliance: Obtaining relevant certifications, such as API, ASTM, or ASME, demonstrates a manufacturer’s commitment to quality and compliance with industry standards. These certifications build trust with customers and enhance their confidence in the products.
- Employee Training and Skill Development: Manufacturers invest in training and skill development programs to ensure their workforce remains knowledgeable about the latest technologies and industry trends. A well-trained workforce enhances the overall efficiency and quality of the manufacturing process.
By combining quality assurance practices with innovative approaches, steel castings manufacturers can consistently deliver high-quality products that meet the stringent demands of various industries and contribute to advancements in engineering and technology.