Quality assurance is a crucial aspect of Lost Foam Casting (LFC) manufacturing to ensure excellence at every step of the process. LFC is a casting method that involves creating a foam pattern of the desired part, coating it with a refractory material, and then pouring molten metal into the mold. To maintain high-quality standards, the following steps can be taken:
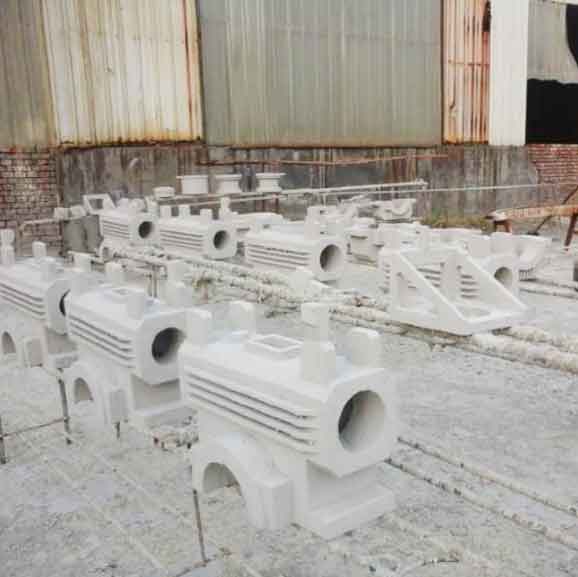
- Design and Engineering: Start with a well-designed part and ensure the engineering specifications are accurate. This includes considering factors like dimensional tolerances, material properties, and part functionality. Utilize computer-aided design (CAD) and simulation tools to optimize the design and predict any potential issues.
- Material Selection: Choose high-quality materials for the foam patterns and refractory coatings. The foam should have uniform cell structure and density, and the refractory material should have good thermal stability and mechanical strength. Conduct material testing and analysis to ensure they meet the required specifications.
- Process Control: Implement robust process controls to maintain consistency and repeatability. This includes monitoring parameters such as foam density, coating thickness, sand compaction, and pouring temperature. Use sensors, gauges, and automated systems to measure and control these variables.
- Foam Pattern Production: Ensure precise manufacturing of foam patterns. Use high-quality molds and CNC machining techniques to achieve accurate dimensions and surface finishes. Perform regular inspections to identify any defects or imperfections in the foam patterns.
- Coating Application: Apply the refractory coating evenly and uniformly onto the foam patterns. Control variables such as coating thickness, drying time, and coating composition to achieve the desired properties. Inspect the coated patterns for any defects like cracks or uneven coating distribution.
- Mold Assembly: Assemble the coated foam patterns into the mold without causing any damage. Ensure proper alignment and secure the patterns to prevent movement during casting. Inspect the assembled mold for any gaps, misalignment, or other issues that could affect the casting quality.
- Molten Metal Pouring: Maintain strict control over the pouring process. Monitor the metal temperature, pouring rate, and flow dynamics. Prevent any impurities from entering the mold by using appropriate filtration techniques. Employ non-destructive testing methods like X-ray or ultrasound to detect any defects in the cast part.
- Cooling and Solidification: Control the cooling process to ensure proper solidification without any shrinkage or distortion. Implement cooling systems and time the process accurately. Use thermal analysis techniques to optimize the cooling parameters and predict potential defects.
- Finishing and Inspection: After the casting has solidified and cooled, remove the foam residues and perform necessary finishing operations. Inspect the cast part for any surface defects, dimensional accuracy, and structural integrity. Utilize techniques like visual inspection, dimensional measurements, and non-destructive testing to verify the quality.
- Continuous Improvement: Implement a continuous improvement process to address any quality issues and optimize the manufacturing process. Analyze data, collect feedback from inspections and tests, and identify areas for improvement. Make necessary adjustments to the process, equipment, or materials to enhance quality and efficiency.
By following these steps and maintaining a strong focus on quality assurance, Lost Foam Casting manufacturers can ensure excellence at every step of the process, resulting in high-quality castings that meet the desired specifications.