Pig iron is one of the main raw materials of gray cast iron. Figure (a) shows the metallography of pig iron raw material, which contains a large amount of large graphite; Figure (b) shows the metallography of gray cast iron produced with pig iron as the main raw material, which contains a large amount of coarsened large graphite, which is mainly caused by the heredity of graphite in pig iron. The existence of this kind of graphite is very harmful to the mechanical properties of gray cast iron, and the gray cast iron cylinder with more such graphite can not meet the requirements. In order to avoid the genetic influence of pig iron, the use of pig iron should be reduced as much as possible in the production of cast iron.
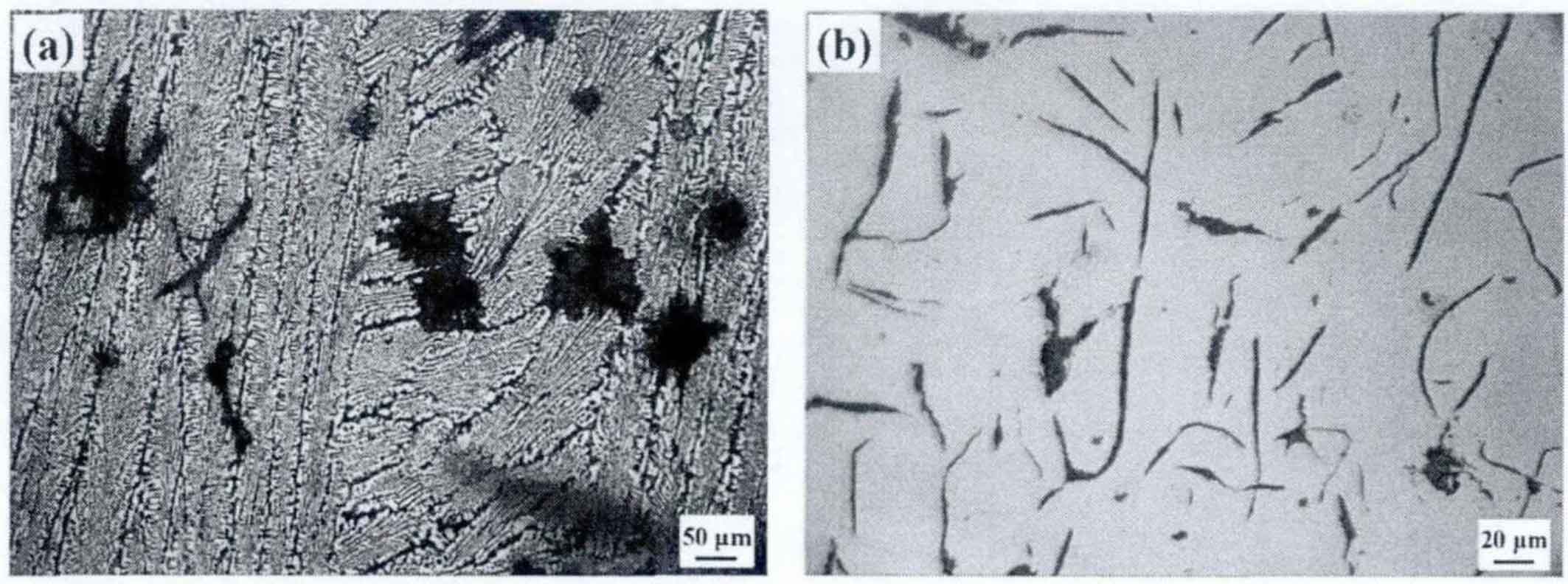
It can be seen from the research that the heredity of tin in the returned material and the high content of Ti in the scrap will make the size and content of tin in gray cast iron larger. Therefore, low-iron scrap (Ti ≤ 0.03%) is used, and the addition ratio of scrap to recycled material is improved to control the molten iron quality of gray cast iron.
The raw materials of grey cast iron are also smelted in 60 (k) kW, 8t / h medium frequency induction furnace. In the process of filling, in order to prevent carbon burning and protect the furnace lining, the feeding sequence of raw materials is as follows: return charge – Scrap – carburizing agent. The outlet water temperature and pouring temperature of molten iron are also controlled at 1510 ± 30 ° C and 1435 ± 15 ° C. the inoculation treatment is primary in ladle inoculation + secondary flow inoculation. Before pouring, the content of C and other elements shall be measured by thermal analyzer and direct reading spectrometer to ensure the composition of molten iron before pouring.
On the premise of controlling the chemical composition of grey cast iron, the amount of scrap added to the main raw materials of grey cast iron (scrap /. Its main component is graphite fossil oil coke, which has high solubility and fast melting rate.