Qi Jiyu found that the material, derusting method, thickness and metal liquid temperature of the diaphragm may affect the bonding quality of the composite layer. When the separator is treated by pickling and drying, the high chromium cast iron and carbon steel on both sides of the separator have no casting defects, and the dense structure is formed in the interface area. The reason is that the derusting clapboard acts as an internal chill, and the metal liquid near the clapboard forms a dense fine-grained structure layer due to chilling. About 0.2-0.5mm thick diaphragms are dissolved by the liquid metal on both sides and form a uniform fusion transition layer with them. The factors affecting the thickness reduction of diaphragm are mainly the casting thickness, liquid weight, casting material and temperature, among which temperature and material are the most key factors. The melting of diaphragm increases with the increase of temperature and carbon content. The thickness of the diaphragm must be controlled more accurately. Too thick diaphragm leads to rapid heat dissipation and cannot form metallurgical combination, which is easy to produce cold diaphragm. Too thin diaphragm is very easy to burn through and deform by high-temperature liquid metal, which is not conducive to the effective and high-quality combination of the two metals. Qi Jiyu et al. Obtained the empirical formula of diaphragm thickness by linear regression method through many tests, The formula is applicable to the lining plate of ball mill with weight of 50-150kg and wall thickness of 35-90mm.
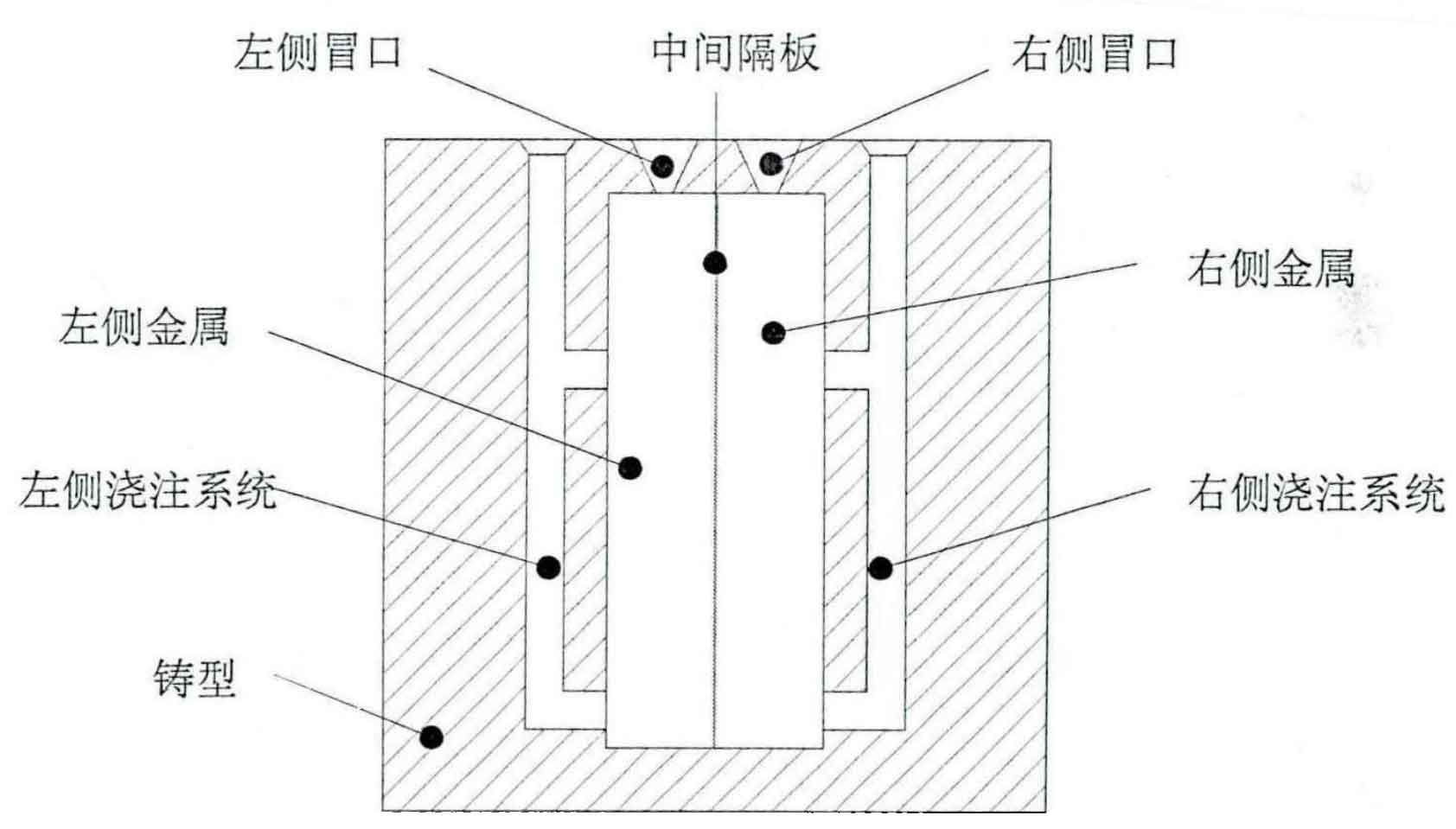
Xiang Yungui uses high chromium cast iron with mass fraction of 2.4% – 2.8% C, 12% – 14% Cr, < 1% Mn, 0.4% – 0.8% Si, 0.4% – 0.6% Mo and 0.5% – 1% Cu as wear-resistant layer to compound with 25 steel, and uses 20 steel as diaphragm and horizontal and vertical cast bimetallic composite liner. The bending strength is 1060mpa, the deflection is 5.2mm and the impact toughness is 31.6j/cm2. stay Φ The 3700×8500 mill is installed and put into trial use. The bimetallic liner is safe to use, and there is no fracture, which is better than
The wear resistance of ZGMn13 lining plate is increased by 3 times. The study on the microstructure of the composite interface shows that the poured high-temperature liquid metal melts a certain thickness of separator to realize metallurgical bonding, the physical and chemical adsorption layers on the separator disappear, and the impurities and oxides with low density float with the liquid surface, so as to ensure that a clean and uniform interface transition zone is formed between the separator, steel and high chromium cast iron.
An Jiangying further studied: driven by the temperature field and concentration field, the carbon atoms in the high chromium cast iron diffuse into the diaphragm, but the carbon content in the transition zone can not reach the level of cast iron, so the transition zone should be a typical high carbon steel structure. It is difficult to see carbides under ordinary light microscope, but small carbides can be observed by electron microscope. Due to the carburizing effect of the diaphragm, the gradient composites of high carbon steel and medium carbon steel are formed along the interface area of high complex cast iron to carbon steel. The research conclusion is that the transition of composition on the composite interface determines the gradual change of microstructure and properties of castings, so the flat cast and vertical cast bimetallic composite wear-resistant castings have good bonding strength.
The research shows that the advantages of the horizontal and vertical pouring process are as follows: first, the blocking effect of the middle diaphragm greatly reduces the mixing probability between carbon steel and high chromium cast iron; Second, because the stepped gating system is adopted, the temperature field distribution in the process is conducive to the formation of sequential solidification of castings, resulting in good feeding effect and greatly reduced shrinkage cavity and porosity; In addition, the metal liquid level rises slowly, so that the bonding interface between the diaphragm and the two metals is not easy to appear non-metallic inclusions and entrapment pores, and the casting structure is more compact; Third, by reasonably designing the shape of the middle diaphragm, the bonding area and bonding force can be increased, and the thickness of the wear-resistant part of the casting can be uniform. The disadvantages of this process are: the diaphragm treatment process is complex; Component segregation occurs during the solidification of liner materials, resulting in uneven wear resistance of the working surface of liner.