1. Introduction
The spindle box is a crucial component in various machine tools as it houses the spindle and its associated complex transmission parts. It directly affects the machining accuracy and stability of the machine tool. Given its importance, high-quality casting of the spindle box is essential, especially ensuring that the shaft barrel, which supports the spindle rotation, is free from any casting defects. This research focuses on optimizing the casting process of the machine tool spindle box using ProCAST software.
1.1 Background of the Research
In the field of machine tool manufacturing, the quality of the spindle box significantly impacts the overall performance of the machine. Traditional casting methods often face challenges such as ensuring proper filling of the mold and preventing defects like shrinkage and porosity. With the advancement of numerical simulation techniques, it has become possible to analyze and optimize the casting process more accurately. ProCAST, a powerful software for casting simulation, provides a platform to study the flow and temperature fields during the casting process, enabling engineers to make informed decisions and improve the casting quality.
1.2 Objectives of the Study
The primary objectives of this research are as follows:
- To design an appropriate casting process for the machine tool spindle box considering its complex structure and high-quality requirements.
- To analyze the flow field and temperature field during the casting process using ProCAST software.
- To optimize the casting process by identifying and addressing potential defects such as flow irregularities, shrinkage, and porosity.
2. Part Analysis
2.1 Dimensions and Weight
The machine tool spindle box casting has a maximum outer dimension of 475 mm × 369 mm × 350 mm and a total weight of 101.16 kg, classifying it as a medium-sized casting.
2.2 Wall Thickness Variation
The wall thickness of the casting varies significantly. The maximum wall thickness exceeds 60 mm, while the minimum is only 10.5 mm. This large variation in wall thickness poses a challenge in achieving a defect-free casting, as it can lead to issues such as shrinkage and cracking during the solidification process.
2.3 Material Properties
The spindle box is made of HT300, an important casting material. Its chemical composition affects its casting properties. The carbon equivalent of HT300 is approximately 3.558%, classifying it as a hypoeutectic cast iron with a eutectic degree of around 0.82. This material has relatively poor fluidity, and during solidification, it only contracts, increasing the tendency for shrinkage and porosity. The following table summarizes the chemical composition of HT300:
Component | C | Si | Mn | P | Fe |
---|---|---|---|---|---|
Content | 2.90 – 3.20 | 1.40 – 1.70 | 0.80 – 1.00 | <0.15 | Remainder |
3. Casting Process Design
3.1 Pouring Position and Parting Surface
- Pouring Position: Considering the large wall thickness variation, sequential solidification is preferred. Based on the structure of the spindle box, a specific pouring position is selected as shown in Figure 2. This position is chosen to facilitate the formation of a proper solidification sequence.
- Parting Surface: The parting surface is selected on the upper surface of the shaft barrel square hole. This surface is the largest cross-section of the casting and requires the least use of loose pieces, making the molding process more convenient.
3.2 Design of the Pouring System
- Pouring System Type: A semi-closed bottom pouring system is adopted. The gate ratio is ∑A_straight : ∑A_cross : ∑A_inner = 1.1 : 1.5 : 1. This type of pouring system is chosen for its ability to ensure a smooth filling process and avoid impacts and splashes.
- Inner Runner Options: Two options for the inner runner are considered, namely the side inner runner and the bottom inner runner. The following table shows the dimensions of the runners for each option:
Option Number | Straight Runner | Cross Runner | Inner Runner | D | ||
---|---|---|---|---|---|---|
Number of Pieces | Diameter (mm) | Number of Pieces | Diameter (mm) | Diameter (mm) | ||
1 | 1 | 30 | 2 | 25 | 2 | 20 |
2 | 4 | 15 | 1 | 25 | 1 | 15 |
4. Numerical Simulation and Optimization
4.1 Flow Field Simulation
- Side Inner Runner: The simulation of the side inner runner shows that during the initial filling stage, a rotation phenomenon occurs. The metal liquid fills the bottom in a rotating state, which is likely to introduce defects such as gas entrainment and slag inclusion. Additionally, two streams of metal liquid flow along the sides of the cavity and meet at the bottom of the shaft barrel, forming a weld mark. In the later filling stage, the filling is relatively stable.
- Bottom Inner Runner: For the bottom inner runner, due to its vertical installation, a fountain phenomenon occurs when the metal liquid enters the cavity. This can lead to defects such as pores. However, the filling of the support seat is relatively fast and the liquid levels at the far and near ends are basically the same, avoiding significant disturbances caused by the liquid level difference. The later filling is also relatively stable.
4.2 Runner Optimization
- Cause of the Problem: The rapid flow rate of the bottom inner runner is due to the large pressure head when the metal liquid first enters the cavity. The height difference from the top of the straight runner to the bottom of the casting is nearly 470 mm, causing the metal liquid to gain a high speed under the influence of gravity and resulting in the fountain phenomenon.
- Solution: A buffer runner is introduced in the straight runner. The cross-sectional area of the buffer runner is 1.3 times that of the straight runner to ensure a good buffering effect. It is placed at the parting surface for convenience in molding and slag blocking. This design effectively reduces the speed of the metal liquid entering the cavity, as shown in the following figure. The flow rate of the metal liquid entering the cavity is reduced to about 0.49 m/s, which is approximately 50% slower than before optimization, and the height of the metal liquid spray is also significantly reduced, achieving a flat spreading state.
4.3 Temperature Field Simulation and Optimization
- Before Optimization: The simulation of the temperature field before optimization shows that there is a collapse at the top of the shaft barrel, indicating insufficient self-compensation. The temperatures at the top and four ends of the side wall of the shaft barrel are relatively high, and due to the wall thickness difference, the solidification is slow. Shrinkage and porosity are mainly found in these positions.
- After Optimization: After optimization, four risers and 25 chilled irons are used. The risers are calculated based on the structure size of the spindle box, and the chilled irons are placed at the hot spots such as the shaft barrel and side wall. The temperature distribution of the casting shows a decreasing trend from top to bottom, with the highest temperature in the risers. Shrinkage and porosity are concentrated in the pouring and riser systems, and almost no such defects are found in the casting, demonstrating the effectiveness of the optimization.
5. Conclusion
The casting process of the machine tool spindle box requires careful consideration of various factors due to its complex structure and high-quality requirements. The following are the key findings and conclusions of this research:
- The semi-closed bottom pouring system is an appropriate choice for the spindle box casting, considering its wall thickness variation and the need for sequential solidification.
- The flow field simulation using ProCAST reveals that the side inner runner can cause metal liquid rotation and associated defects, while the bottom inner runner can lead to fountain phenomena and pores. The introduction of a buffer runner in the straight runner effectively addresses the issue of rapid flow in the bottom inner runner and ensures a smooth filling process.
- The temperature field simulation shows that the spindle box has many hot spots and HT300 has insufficient self-compensation. The use of risers and chilled irons can achieve a good sequential solidification and avoid shrinkage and porosity defects.
Overall, this research provides valuable insights and guidelines for the casting process of machine tool spindle boxes, enabling the production of high-quality castings.
6. Detailed Analysis of Each Step
6.1 In-depth Look at Part Analysis
The detailed examination of the machine tool spindle box part is crucial for understanding its casting requirements. The significant variation in wall thickness, from a minimum of 10.5 mm to a maximum exceeding 60 mm, demands a casting process that can handle the differential cooling rates. This variation not only affects the solidification process but also has implications for the potential formation of defects.
The material choice of HT300 further complicates the process. Its hypoeutectic nature and relatively poor fluidity mean that special attention must be paid to ensure proper filling of the mold. The chemical composition of HT300, as detailed in the previous section, influences its mechanical and casting properties. For example, the carbon content within the specified range affects the hardness and strength of the final casting.
6.2 Pouring Position and Parting Surface Selection Rationale
The selection of the pouring position and parting surface is a strategic decision in the casting process. The chosen pouring position, as depicted in Figure 2, is designed to promote sequential solidification. This is essential given the large wall thickness differences in the spindle box. By carefully considering the flow of the molten metal and the heat dissipation during solidification, this position allows for a more controlled and efficient casting process.
The parting surface on the upper surface of the shaft barrel square hole offers several advantages. It simplifies the molding process as it requires fewer loose pieces. This not only reduces the complexity of the mold but also improves the accuracy and repeatability of the casting. Additionally, it provides a natural boundary for the separation of the two halves of the mold, facilitating the removal of the casting after solidification.
6.3 Pouring System Design Considerations
The semi-closed bottom pouring system with a specific gate ratio (∑A_straight : ∑A_cross : ∑A_inner = 1.1 : 1.5 : 1) is selected based on multiple factors. The semi-closed nature helps in controlling the flow rate of the molten metal, preventing excessive turbulence and splashing. The bottom pouring aspect ensures a more even distribution of the metal within the mold cavity, reducing the likelihood of air entrapment and other defects.
The consideration of different inner runner options, namely the side inner runner and the bottom inner runner, is a key part of the design process. Each option has its own set of advantages and disadvantages, as revealed by the flow field simulation. The side inner runner’s rotation phenomenon during the initial filling stage can lead to a host of problems, including gas entrainment and slag inclusion. On the other hand, the bottom inner runner’s fountain phenomenon, although it has some benefits in terms of maintaining a relatively even liquid level in certain areas, also poses the risk of pore formation.
7. Numerical Simulation Insights
7.1 Flow Field Simulation Revelations
The flow field simulation using ProCAST provides a detailed understanding of the behavior of the molten metal during the filling process. For the side inner runner, the rotation phenomenon is a significant concern. This rotation not only disrupts the smooth flow of the metal but also causes the metal to mix with air and slag in an uncontrolled manner. The formation of weld marks at the bottom of the shaft barrel where the two streams of metal meet further highlights the potential for defects in the final casting.
The bottom inner runner’s fountain phenomenon is another critical aspect. The high pressure head causing the metal to spray upwards can lead to the entrapment of air bubbles, resulting in pores in the casting. However, the relatively even filling of the support seat area shows that there are some positive aspects to this runner design as well. The comparison between the two inner runner options clearly indicates that both have their own challenges and that a more optimized solution is required.
7.2 Runner Optimization Impact
The introduction of the buffer runner in the straight runner has a profound impact on the casting process. By reducing the speed of the metal liquid entering the cavity, it effectively addresses the fountain phenomenon associated with the bottom inner runner. The carefully calculated cross-sectional area of the buffer runner, which is 1.3 times that of the straight runner, ensures an optimal buffering effect.
This optimization not only improves the quality of the initial filling but also has a cascading effect on the overall casting quality. The reduced flow rate and the more controlled entry of the metal into the cavity lead to a more even distribution of the metal within the mold, reducing the likelihood of defects such as porosity and slag inclusion. The visual representation of the optimized flow, with the metal liquid entering the cavity at a slower and more controlled rate, as shown in the relevant figures, provides clear evidence of the effectiveness of this optimization.
7.3 Temperature Field Simulation and Optimization Outcomes
The temperature field simulation before and after optimization offers valuable insights into the solidification process of the spindle box casting. Before optimization, the presence of a collapse at the top of the shaft barrel and the concentration of shrinkage and porosity in certain areas indicate that the self-compensation mechanism of the material is insufficient. The higher temperatures at the top and side wall ends, due to the wall thickness differences, slow down the solidification process and contribute to the formation of defects.
After optimization, the use of risers and chilled irons significantly alters the temperature distribution. The risers, carefully sized and positioned based on the spindle box structure, act as reservoirs of molten metal, providing additional material for compensation during solidification. The chilled irons, placed at the hot spots such as the shaft barrel and side wall, accelerate the cooling rate in these areas, promoting a more uniform solidification. The resulting temperature distribution, with a decreasing trend from top to bottom and the highest temperature in the risers, shows that the optimization has been successful in achieving a more controlled and defect-free solidification process.
8. Practical Implications and Future Directions
8.1 Implications for Machine Tool Spindle Box Casting Industry
The findings of this research have significant implications for the machine tool spindle box casting industry. The optimized casting process, with its carefully designed pouring system, flow field and temperature field control, can lead to a substantial improvement in the quality of spindle box castings. This, in turn, can enhance the performance and reliability of machine tools, as the spindle box is a critical component.
Manufacturers can expect reduced rejection rates and increased productivity by implementing the proposed casting process. The ability to predict and prevent defects such as shrinkage, porosity, and flow irregularities through numerical simulation means that resources can be more effectively allocated, reducing waste and costs. Additionally, the improved understanding of the casting process can lead to more innovative designs and better utilization of materials, further enhancing the competitiveness of the industry.
8.2 Future Research Directions
While this research has made significant progress in optimizing the casting process of machine tool spindle boxes, there are still several areas that warrant further investigation. One potential area of future research could be the exploration of alternative materials or material combinations that could offer better casting properties while maintaining or improving the mechanical performance of the spindle box.
Another direction could be the refinement of the numerical simulation models. Although ProCAST has provided valuable insights, there may be room for improvement in accurately predicting certain phenomena, such as the interaction between the molten metal and the mold interface under more complex conditions. Additionally, the study of the long-term performance and durability of spindle box castings under different operating conditions could provide valuable information for further optimizing the casting process.
In conclusion, this research on the casting process of machine tool spindle boxes based on ProCAST has made important contributions to the understanding and optimization of this critical manufacturing process. The detailed analysis of the part, the design of the casting process, and the numerical simulation and optimization have provided a comprehensive framework for producing high-quality spindle box castings. The practical implications for the industry and the identified future research directions offer a roadmap for further development and improvement in this field.
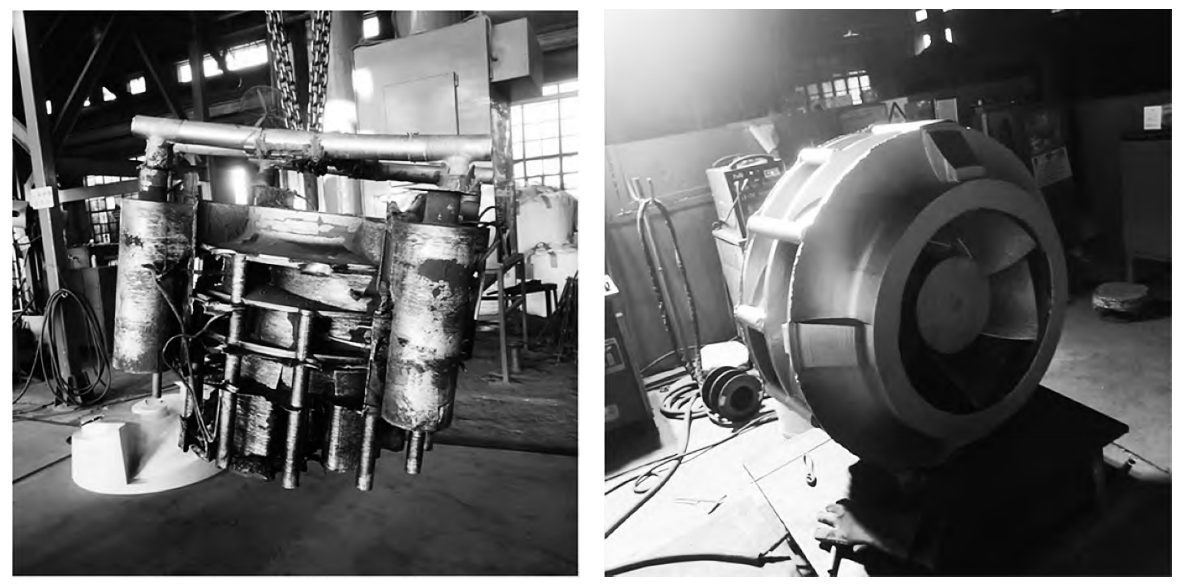