This article focuses on the precision casting process of iron-based superalloy blades, especially the K213 superalloy. Through the use of MAGMA casting simulation software, the mold filling and solidification processes are simulated and analyzed in detail. The research content includes the distribution of fluid velocity field, solid fraction, temperature field and voids during the casting process. By analyzing the simulation results, the reliability of the gating system is verified, and the possible positions of casting defects are determined. This research provides a solid theoretical basis for the design of the precision casting process of iron-based superalloy blades and has important reference significance for improving the quality of high-temperature alloy precision casting.
1. Introduction
In many fields such as aero jet engines, ship gas turbines and industrial gas turbines, high-temperature gases are usually used to drive turbines. Turbine blades, as an important part of turbines, need to withstand harsh environments such as high temperature and hot corrosion (the working temperature of a typical gas turbine exceeds 500 °C). Superalloys have good oxidation resistance, thermal stability, fatigue resistance and good creep fracture properties, so they are widely used in this environment.
K213 is an iron-nickel-chromium-based cast superalloy. Aluminum and titanium are added to form the γ phase and achieve precipitation strengthening. It is solid solution strengthened by W and the grain boundaries are strengthened by a trace amount of B. The alloy has excellent casting process and good comprehensive properties below 750 °C. In recent years, high-temperature alloy parts tend to be precision and thin-walled, which puts forward higher requirements for the precision casting process. Traditional experimental processes have problems such as high trial-and-error costs and long cycles, while computer-aided design can greatly reduce trial-and-error costs and shorten the process design cycle.
2. Experimental Method
2.1 Material Selection
The K213 cast superalloy master alloy is selected for the experiment. Its chemical composition is shown in Table 1. The melting point of the K213 alloy is 1324 – 1361 °C, the density is ρ = 8.14 g/cm³, and the expansion coefficient is 18.61×10⁻⁶ °C⁻¹ at 20 – 800 °C.
Element | Content | Element | Content |
---|---|---|---|
C | ≤0.10 | B | 0.05 – 0.10 |
Cr | 34.00 – 38.00 | Ni | 14.00 – 16.00 |
Mn | ≤0.50 | Fe | Remainder |
W | 4.00 – 7.00 | Si | ≤0.50 |
Al | 1.50 – 2.00 | S | ≤0.015 |
Ti | 3.00 – 4.00 | P | ≤0.015 |
2.2 Model and Software Settings
According to the needs of a company, the simulated part is determined to be a certain type of turbine impeller blade. The part model is shown in Figure 1.
[Insert a picture of the impeller blade model here]
The MAGMA casting simulation software is used to simulate the casting process of the K213 alloy blade. The temperature field and defect formation and distribution during the casting process are analyzed through the filling and solidification processes to provide correct process method guidance for actual production. Gravity casting is used, and the acceleration due to gravity is 9.8 m/s². The basic parameters include a weight factor of 0.8, a relaxation factor of 1.6, an initial time step of 0.0001 s, and the heat transfer coefficients between the casting and air and between the casting and the mold are both 0.023. The casting temperature is 1550 °C.
The casting is a blade with a complex shape. The SolidWorks three-dimensional solid modeling software is used to model the entire gating system. The top gating method is used to pour 4 alloy blades at a time. The mass of a single blade is 3 kg, and the solidification process of the blade is fed through the gate and the runner. The MAGMA casting simulation software is used for meshing, and the mesh parameter is selected as 1 mm.
3. Results and Analysis
3.1 Solid Fraction during Filling Process
Figures 2 and 3 show the solid fraction during the filling process. From Figure 3, the distribution of the solid fraction inside the blade and the gating system can be observed through the longitudinal section view. It can be seen that during the pouring process of the blade part, the alloy liquid is always in a liquid state, enabling the complete filling of the blade part. The filling is completed in 15 s, and solidification begins at the edge of the blade at 25 s. After the blade is solidified, the runner begins to solidify, and the last solidification part occurs at the center of the connection between the gate and the runner.
[Insert pictures of the solid fraction during the pouring process and its longitudinal section here]
3.2 Temperature Field Simulation Results and Analysis
Figures 4 and 5 show the temperature field distribution during the pouring process. From Figure 5, the distribution of the temperature field inside the blade and the gating system can be observed through the longitudinal section view. It can be seen that during the pouring process of the blade part, the alloy liquid is always in a high temperature state, and the temperature is about 1500 °C throughout the process. After 3 s, the blade part is filled, and the temperature at the edge of the blade begins to decrease. The lowest temperature is about 1400 °C, which is still higher than the alloy melting point, so it is not easy to have defects. After 15 s of filling, the temperature in some areas at the edge of the blade drops to about 1230 °C. After 15 minutes, the temperature at the center of the connection between the gate and the runner is still around 1300 °C, and the rest of the parts drop below the melting point. This indicates that the designed gate and runner can feed the blade part.
[Insert pictures of the temperature field simulation results during the pouring process and its longitudinal section here]
3.3 Fluid Velocity Field Simulation Results and Analysis
Figure 6 shows the simulation results of the velocity field during the filling process. It can be seen from Figure 6 that the blade part is poured at 3 s, but there is still disturbance at the edge of the blade. At the same time, there is a small amount of air entrainment in the two outermost blades. With the subsequent pouring, this disturbance basically does not cause casting defects. At 4 s, the alloy flow in the blade part is completely static. When the casting is completed at 15 s, it can be observed that the liquid level of the gate has a significant decrease, indicating that the gate and runner play a good feeding role.
[Insert a picture of the fluid velocity field simulation results here]
3.4 Void Simulation Results and Analysis
Figure 7 shows the void simulation results during the pouring process. It can be seen that during the pouring process, voids are formed in the centers of the two outermost blades due to the disturbance of the pouring process. However, with the progress of the pouring, under the pressure of the metal liquid, the voids continue to rise and finally concentrate at the gate and runner.
[Insert a picture of the void simulation results here]
4. Conclusions
This article focuses on the MAGMA casting simulation research of the fluid velocity field, solid fraction distribution, temperature field distribution and void distribution during the filling and solidification process of the K213 superalloy in the precision investment casting process. Through the analysis of the simulation results, the possible positions of casting pores are obtained, and the reliability of the gating system is verified. The conclusions are as follows:
- During the pouring process of the blade part, the alloy liquid is always in a liquid state, enabling the complete filling of the blade part. After the blade is solidified, the runner begins to solidify, and the last solidification part occurs at the center of the connection between the gate and the runner.
- The temperature field simulation results show that after the filling is completed, the edge of the blade first begins to cool down, and the temperature shows a gradient increase from the top of the blade to the gate. The center position of the connection between the gate and the runner is always in a high temperature state, and the rest of the parts drop below the melting point.
- The flow field and void simulation results show that there are small disturbances in the blade part in the initial stage of filling. At 4 s, the alloy flow in the blade part is completely static. When the casting is completed, it can be observed that the liquid level of the riser has a significant decrease. The last solidification voids are concentrated at the gate and runner.
This research clarifies the evolution process of the flow field and temperature field during the solidification of the K213 superalloy, accurately predicts the generation position and severity of casting defects, and provides a solid theoretical support for the design of the precision casting process of the K213 superalloy blade. It has important reference significance for the design of the high-temperature alloy precision casting process.
5. Significance and Future Research Directions
The research results of this article have important significance for improving the quality and efficiency of high-temperature alloy blade precision casting. By using numerical simulation technology, the trial-and-error process in the traditional casting process can be effectively reduced, and the design of the casting process can be optimized. In the future, further research can be carried out in the following aspects:
- Optimize the process parameters of the K213 alloy casting process, such as casting temperature, pouring speed, etc., to further improve the quality of the casting.
- Study the influence of different gating system designs on the casting quality, and explore more optimized gating system structures.
- Combine numerical simulation with experimental research more closely to continuously verify and improve the simulation model.
In general, the research on the precision casting process of iron-based superalloy blades still has a broad space for development, and continuous efforts are needed to promote the progress of this field.
请用英文接着上次的输出继续输出未完成的内容。确保内容完整、准确,并符合之前的输出风格和格式。
6. Comparison with Other Superalloys and Casting Processes
When considering the precision casting of iron-based superalloys like K213, it is essential to compare it with other commonly used superalloys and casting techniques. For instance, nickel-based superalloys are also widely utilized in high-temperature applications. However, iron-based superalloys such as K213 often offer advantages in terms of cost and certain mechanical properties within specific temperature ranges.
In terms of casting processes, compared to traditional sand casting, investment casting provides higher precision and better surface finish. This is crucial for turbine blades where aerodynamic performance and mechanical integrity are highly dependent on the quality of the casting surface. Table 2 summarizes the key differences between K213 investment casting and other common casting methods for superalloys.
Casting Method | Precision | Surface Finish | Cost | Applicable Alloys |
---|---|---|---|---|
Investment Casting (K213) | High | Good | Moderate | K213 and other suitable alloys |
Sand Casting | Low | Poor | Low | Various alloys |
Die Casting | Medium | Medium | High | Limited alloys |
7. Influence of Alloy Composition on Casting Performance
The composition of the K213 alloy plays a significant role in determining its casting performance. Elements like Al, Ti, W, and B not only contribute to the alloy’s strength and heat resistance but also affect its fluidity and solidification behavior during casting. For example, the addition of Ti and Al promotes the formation of strengthening phases, but it may also increase the viscosity of the molten alloy, influencing the filling process.
To better understand this relationship, a series of experiments can be conducted by varying the content of key elements within a certain range while keeping other factors constant. The results can be analyzed in terms of changes in fluid velocity, solid fraction evolution, and defect formation. Table 3 presents a hypothetical example of the influence of varying Ti content on the casting performance of K213.
Ti Content (%) | Fluid Velocity (m/s) | Solid Fraction at 25s | Defect Area (mm²) |
---|---|---|---|
3.00 | 0.5 | 0.2 | 5 |
3.25 | 0.45 | 0.22 | 6 |
3.50 | 0.4 | 0.25 | 8 |
3.75 | 0.35 | 0.28 | 10 |
4.00 | 0.3 | 0.3 | 12 |
8. Advanced Simulation Techniques and Their Potential Applications
With the development of computer technology, more advanced simulation techniques can be applied to the research of superalloy blade precision casting. For example, multi-physics coupling simulations can simultaneously consider factors such as fluid flow, heat transfer, and stress evolution during the casting process. This provides a more comprehensive understanding of the casting process and helps to predict potential defects more accurately.
Another emerging technique is the use of artificial intelligence algorithms to optimize the casting process parameters. By training the algorithm with a large amount of experimental and simulation data, it can quickly search for the optimal combination of parameters, reducing the time and cost required for traditional trial-and-error methods. Figure 8 shows a schematic diagram of a multi-physics coupling simulation model for superalloy blade casting.
[Insert a schematic diagram of the multi-physics coupling simulation model here]
9. Quality Control and Inspection Methods in Precision Casting
To ensure the quality of the precision-cast K213 alloy blades, a series of quality control and inspection methods are necessary. Non-destructive testing techniques such as X-ray inspection and ultrasonic testing can be used to detect internal defects in the castings. Additionally, metallographic analysis can provide information about the microstructure of the alloy, helping to evaluate its mechanical properties.
During the production process, strict control of process parameters and raw material quality is also essential. Regular sampling and testing of the castings can help to identify and correct any potential problems in a timely manner. Table 4 lists some common quality control and inspection methods and their applications in superalloy blade precision casting.
Inspection Method | Purpose | Detection Limit |
---|---|---|
X-ray Inspection | Detect internal voids and cracks | > 0.1 mm |
Ultrasonic Testing | Identify internal defects and measure thickness | Depends on frequency |
Metallographic Analysis | Analyze microstructure and grain size | – |
10. Environmental and Energy Considerations in Casting Processes
In addition to focusing on the technical aspects of superalloy blade precision casting, it is also necessary to consider the environmental and energy impacts of the casting process. For example, the energy consumption during melting and casting operations can be significant. Therefore, efforts can be made to optimize the process to reduce energy consumption, such as improving the efficiency of the melting furnace and optimizing the pouring process.
From an environmental perspective, measures should be taken to reduce waste and emissions generated during the casting process. Recycling of scrap materials and proper treatment of exhaust gases are important steps in promoting sustainable casting production. shows a flowchart of a sustainable casting process considering environmental and energy factors.
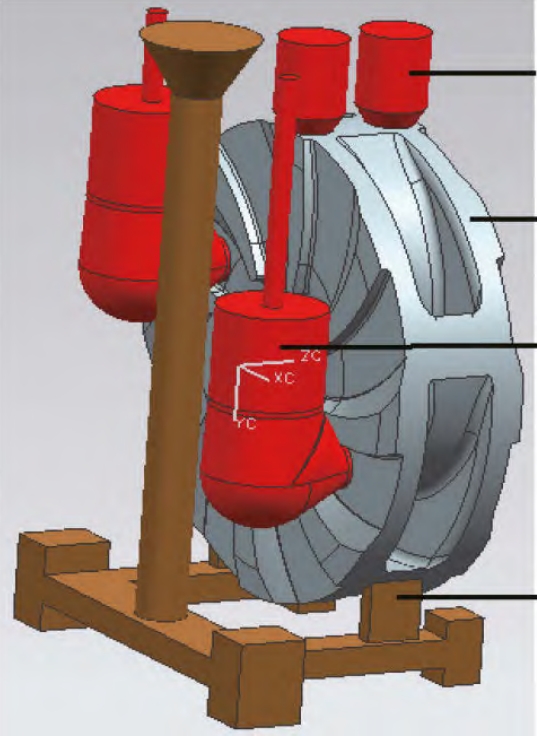