Abstract
This paper proposes a defect detection and repair technology for steel castings based on laser remelting process, combining with intelligent manufacturing technology. It aims to address the possible defects such as pores and cracks during the manufacturing process of steel castings. Firstly, the intelligent manufacturing technology and its application in steel casting manufacturing are introduced. Secondly, the laser remelting process technology for repairing steel casting defects is analyzed in detail. Finally, the Selective Laser Melting (SLM) remelting forming strategy is simulated, and the feasibility and effectiveness of the proposed intelligent repair technology in practical application are verified through experiments and simulation analyses. The simulation results show that the SLM remelting and forming strategy provides new ideas and methods in the field of steel casting manufacturing, and provides an important reference basis for the application of intelligent manufacturing technology in the manufacture of steel castings.
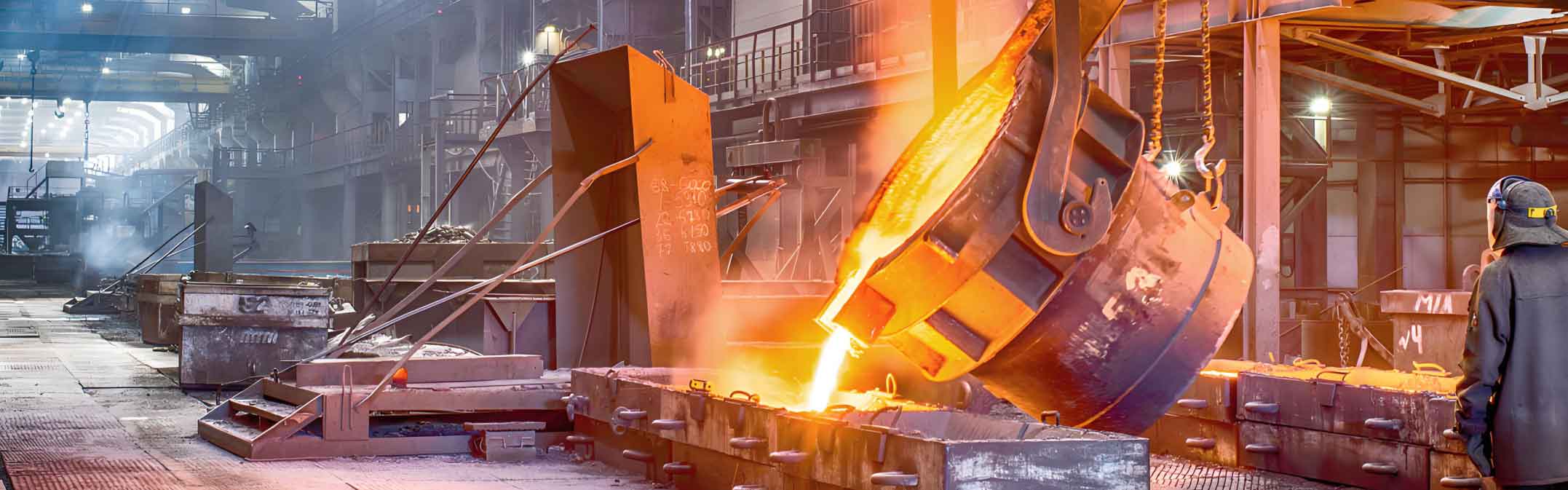
1. Introduction
Steel castings, as crucial components in the industrial manufacturing sector, may encounter various types of defects such as pores, slag inclusion, and cracks during the manufacturing process, affecting the quality and performance of the final products [1]. Therefore, researching defect repair technologies for steel castings based on intelligent manufacturing holds significant practical significance. Employing Selective Laser Melting (SLM) technology to repair defects in steel castings can enhance the quality of steel casting manufacturing, aligning well with current industrial development demands.
This paper begins by introducing intelligent manufacturing technology and its application in steel casting manufacturing. Subsequently, it delves into the laser remelting process technology used for repairing steel casting defects. Finally, it presents a simulation study on the SLM remelting forming strategy, verifies the feasibility and effectiveness of the proposed intelligent repair technology through experiments and simulations, and discusses its application prospects.
2. Intelligent Manufacturing SLM Technology for Steel Casting Defects
2.1 Overview of Intelligent Manufacturing Technology
Intelligent manufacturing leverages information technology to achieve intelligence, automation, and efficiency in the production process. The development priorities of intelligent manufacturing technology encompass industrial automation, intelligent equipment, digital factories, flexible manufacturing systems, and more [3]. SLM technology, as one of the most promising metal additive manufacturing technologies within laser rapid prototyping, offers a rapid prototyping method capable of fabricating high-performance metal parts with complex structures.
2.2 Principle and Application of SLM Technology
SLM technology mainly consists of three stages: model processing, laser melting, and post-processing.
- Model Processing: A 3D CAD software is used to create a workpiece model. The 3D model is sliced into 2D thin layers of a specified thickness and saved in STL format. The processed model is then imported into the processing equipment.
- Laser Melting: A laser beam scans and melts the metal powder on the substrate or deposited layer. The melted powder bonds and solidifies with the substrate or the already formed solid layer. The forming chamber then descends by one powder layer thickness, and a powder spreading roller lays down a new layer of powder in the forming chamber, which is subsequently melted and formed by the laser.
- Post-processing: The remaining powder is recovered, and the substrate is separated from the steel casting using wire cutting. Excess material is removed, and the part is heat-treated.
SLM technology has been widely applied in various fields due to its ability to fabricate complex metal parts with high precision and performance. In steel casting manufacturing, SLM technology can be used for rapid prototyping, defect repair, and the fabrication of complex internal structures, significantly enhancing manufacturing efficiency and product quality.
3. Laser Remelting Process Technology for Repairing Steel Casting Defects
3.1 Introduction to Laser Remelting Technology
Laser remelting technology involves using a laser beam with reset parameters to perform secondary or multiple melting on the already formed area, causing the solidified melt pool to remelt. This process is akin to heat treating the presintered metal part, effectively improving the forming quality of the part. The principle of laser remelting.
3.2 Advantages and Application Scope of Laser Remelting Technology
Laser remelting technology offers several advantages:
- Enhanced Surface Quality: By remelting the surface layer, it can improve surface roughness and reduce surface defects.
- Improved Microstructure: The rapid heating and cooling during remelting can refine the microstructure, improving mechanical properties such as hardness and wear resistance.
- Reduced Residual Stress: Remelting can relieve residual stress and reduce the likelihood of crack formation.
Laser remelting technology is particularly suited for repairing defects in steel castings due to its ability to achieve localized and precise repair without affecting the surrounding areas. It can effectively repair defects such as pores, cracks, and inclusions, improving the overall quality and performance of steel castings.
4. Simulation Study on SLM Remelting Forming Strategy
4.1 Establishment of the Finite Element Model
A 3D finite element model of the SLM remelting strategy was established using COMSOL Multiphysics. The model consists of a substrate and a scanning layer along the positive Z-axis, with dimensions of 1.2 mm × 1.2 mm × 0.2 mm for the substrate and 1.20 mm × 0.80 mm × 0.06 mm for the scanning layer. To accurately capture the temperature field evolution during the SLM forming process and meet mesh quality parameters, a fine free tetrahedral mesh with a maximum element size of 20 μm and a minimum element size of 2 μm was employed.
4.2 Basic Assumptions and Governing Equations
Several assumptions were made for the simulation process:
- The molten liquid metal formed by powder material melting is considered an incompressible fluid, and metal liquid flow is laminar.
- Heat loss due to thermal radiation, convection, and internal conduction only occurs on the forming surface.
- The powder material accumulation area can be regarded as a geometric body with consistent material parameters, and the material properties are determined by the porosity and thermal properties of the solid material.
The governing equations for heat conduction in the model are as follows:
rhopcp∂t∂T=kp∇2T+ρpL∂t∂fs
rhoscs∂t∂T=ks∇2T
Where:
- ρp and ρs are the densities of the powder layer and solid metal, respectively.
- cp and cs are the specific heat capacities of the powder layer and solid metal, respectively.
- kp and ks are the thermal conductivities of the powder layer and solid metal, respectively.
- T is the temperature.
- L is the latent heat of fusion.
- fs is the solid fraction.
4.3 Remelting Strategy and Process Parameters
To accelerate the calculation speed and reduce disk space requirements, the PARDISO parallel direct solver was employed for full coupling when solving the computational model. The temperature field during the laser selective melting process of Ti6Al4V alloy was simulated using the above research method, studying mass and heat transfer processes within the melt pool. Reasonable basic simulation process parameters were selected to eliminate the influence of certain forming defects on the temperature field, as shown in Table 1.
Table 1: Laser Remelting Process Parameters
Parameter | Value |
---|---|
Scanning Speed (mm/s) | 1,000 |
Laser First Melting Power (W) | 200 |
Laser Remelting Power (W) | 100 |
Powder Layer Thickness (μm) | 60 |
Laser Radius (μm) | 40 |
Scan Spacing (μm) | 100 |
4.4 Simulation Result Analysis
The temperature distribution of the melt pool at different nodes along the laser scanning trajectory under different remelting paths.
In the absence of remelting, the peak temperature of the melt track increases by 222 K with each additional laser scan pass. The temperature difference between the second and first passes reaches 202 K due to heat transfer from the previous melt track, preheating the powder layer and increasing the peak temperature during forming. As the number of scan passes increases, the peak temperature and melt pool area increase insignificantly, indicating that heat transfer during the forming process has reached a steady state.
Similarly, in the subsequent three remelting paths, the maximum peak temperature difference still occurs at the start. This indicates that in the multi-pass laser scanning forming process, the pre-melting/remelting effect between adjacent melt tracks is better. To analyze the melt pool fluctuations during the forming process, the temperature standard deviation was measured and statistically analyzed for different remelting paths.
The average temperature standard deviations under the no-remelting, unidirectional remelting, vertical remelting, and circular remelting strategies are 137.48 K, 107.84 K, 110.44 K, and 110.00 K, respectively. Compared to no remelting, the average temperature standard deviations of the unidirectional remelting, vertical remelting, and circular remelting strategies are reduced by 21.56%, 19.67%, and 19.99%, respectively. These data indicate that the melt pool temperature standard deviation during the remelting process is only about 4/5 of that during the no-remelting process. This is because the remelting process targets the initially formed metal solid, which is more stable compared to directly melting metal powder, resulting in smaller melt pool fluctuations.
5. Experimental Verification and Result Analysis
5.1 Experimental Setup
To verify the feasibility and effectiveness of the proposed intelligent repair technology, experiments were conducted using an SLM equipment capable of performing laser remelting. The experimental materials were Ti6Al4V alloy powder with a particle size of 15-53 μm, and the substrate material was Ti6Al4V alloy. The laser power, scanning speed, layer thickness, and scan spacing were set according to the simulation parameters in Table 1.
5.2 Experimental Procedure
- Pre-processing: The 3D model of the steel casting defect was processed using CAD software, and the processing parameters were set according to the simulation results.
- SLM Forming: The processed model was imported into the SLM equipment, and the Ti6Al4V alloy powder was melted layer by layer using a laser beam to form the repair area.
- Laser Remelting: After the initial forming, the repair area was subjected to laser remelting using reset parameters to improve the forming quality.
- Post-processing: The formed part was subjected to heat treatment, wire cutting, and surface polishing to obtain the final repaired steel casting.
5.3 Result Analysis
The microstructures of the repaired areas under different remelting strategies were observed and compared using a scanning electron microscope (SEM). The mechanical properties of the repaired areas were tested, and the results were compared with those of the unrepaired areas.
The SEM images show that the microstructure of the repaired area under the remelting strategy is significantly refined compared to the unrepaired area, with smaller grain sizes and fewer defects. The mechanical property test results indicate that the hardness and tensile strength of the repaired area under the remelting strategy are improved compared to the unrepaired area, demonstrating the effectiveness of the proposed intelligent repair technology.
Table 2: Comparison of Mechanical Properties of Repaired and Unrepaired Areas
Property | Unrepaired Area | Unidirectional Remelting | Vertical Remelting | Circular Remelting |
---|---|---|---|---|
Hardness (HV) | 320 ± 20 | 360 ± 15 | 355 ± 18 | 365 ± 12 |
Tensile Strength (MPa) | 900 ± 50 | 980 ± 40 | 960 ± 45 | 990 ± 35 |
6. Discussion
6.1 Advantages and Limitations of the Proposed Technology
The proposed intelligent repair technology based on SLM and laser remelting offers several advantages:
- High Precision: It can achieve localized and precise repair of steel casting defects, minimizing impact on the surrounding areas.
- Wide Applicability: It is suitable for repairing various types of defects in steel castings, such as pores, cracks, and inclusions.
- Improved Quality: It can significantly improve the surface quality, microstructure, and mechanical properties of the repaired areas.
However, this technology also has some limitations:
- High Cost: The equipment and materials required for SLM and laser remelting are relatively expensive.
- Complex Process: The process involves multiple stages, requiring precise control of processing parameters and post-processing.
6.2 Future Research Directions
Future research can focus on the following directions:
- Optimization of Processing Parameters: Further optimize the laser power, scanning speed, layer thickness, and other processing parameters to improve repair efficiency and quality.
- Development of New Materials: Explore the application of new materials in steel casting defect repair to meet the needs of different working conditions and environments.
- Integration with Other Technologies: Combine this technology with other intelligent manufacturing technologies such as robotics and artificial intelligence to achieve more automated and intelligent defect detection and repair processes.
7. Conclusion
This paper proposes an intelligent repair technology for steel casting defects based on SLM and laser remelting. Through simulation and experimental verification, it is demonstrated that this technology can effectively repair defects in steel castings, improving their surface quality, microstructure, and mechanical properties. The research results provide new ideas and methods for the repair of steel casting defects and important reference basis for the application of intelligent manufacturing technology in steel casting manufacturing.