1.M7C3 eutectic carbide: when the CR / C ratio is greater than 3.5, high hardness eutectic carbide (Fe, Cr) 7C3 (M7C3) (HV 1300 ~ 1800) will be formed in isolated states such as strip shape, rod shape and hexagonal shape. Under the condition of high stress, the eutectic carbide M7C3 can protect the matrix. Relevant research shows that during heat treatment, eutectic carbides of high chromium cast iron will form core-shell carbides as shown in Figure 1 during cooling, which will have a beneficial impact on wear resistance. This is because the structure composed of high hardness carbide M7C3 in the core, medium hardness carbide M23C6 (HV 1000 ~ 1100) in the shell and low hardness matrix will reduce the overall hardness and the interface stress between carbide and matrix.
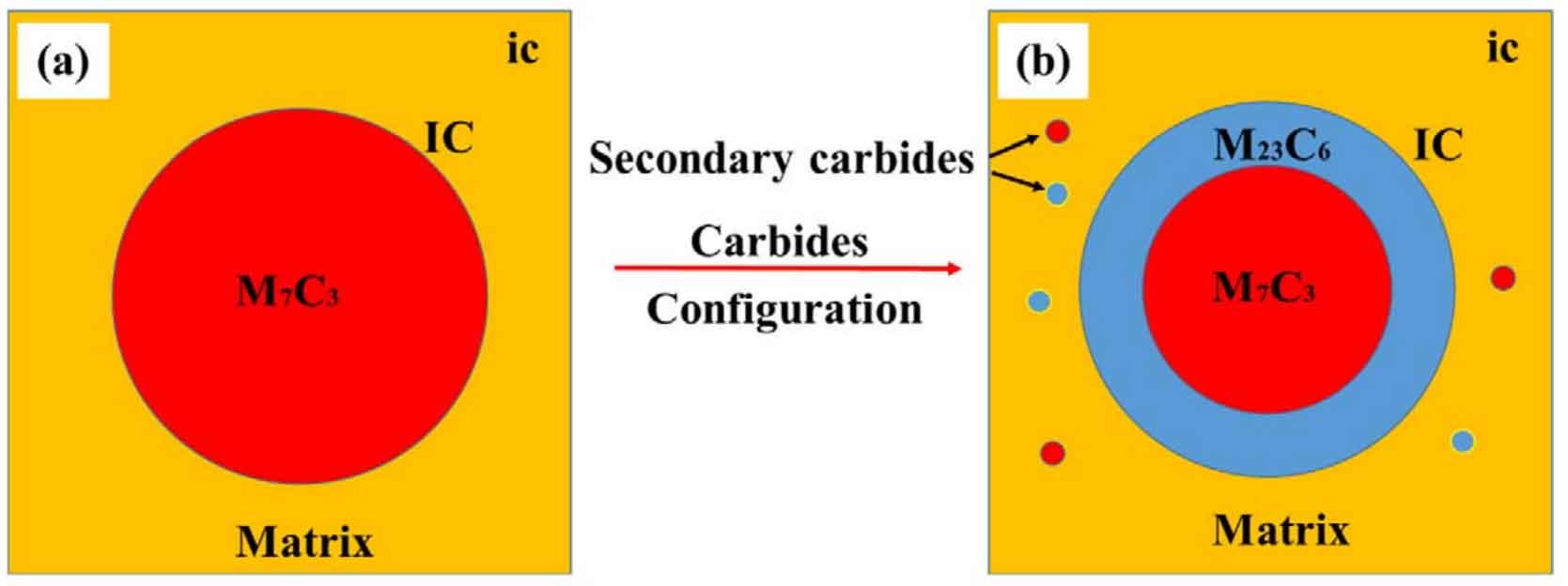
(b) formation of core-shell structured carbide by thermal treatment.
Notes ic means “inner composition”, IC represents “Interface composition”
In addition, the eutectic carbide M7C3 has directionality, and M7C3 carbides in different directions have different properties:
(1) The microhardness of transverse M7C3 carbide (HV 1700 ~ 1900) is higher than that of longitudinal M7C3 carbide (HV 1400), and both transverse and longitudinal microhardness will increase with the increase of Cr content;
(2) The wear resistance of transverse M7C3 carbide is higher than that of longitudinal M7C3 carbide. Fig. 2 (a) and Fig. 2 (b) M7C3 carbides in different directions. Under the condition of high stress wear, M7C3 carbides have the following common fracture types: (a) under the action of bending tensile stress, cracks are formed on the back of carbides whose long axis is perpendicular to the wear surface; (b) Under the action of tangential friction tensile stress, cracks are formed behind abrasive particles; (c) Cracks are formed at the front and rear surfaces perpendicular to the carbide.
2.M3c Carbide: m3c carbide is also directional. M3c carbides have similar fracture toughness values in transverse and longitudinal directions. Transverse carbides (HV 1425) have higher hardness and elastic modulus than longitudinal carbides (HV 935). Under the action of low stress, the wear resistance of transverse carbides is similar to that of longitudinal carbides. However, under the action of high stress, the wear resistance of transverse m3c carbide is better than that of longitudinal m3c carbide. Figure 3 (a, b) shows m3c carbides in different directions.
The orientation of carbides relative to the wear surface is one of the main characteristics affecting the wear properties of cast iron. Dogan et al. Found that under the condition of high stress wear, when the carbide is different from the wear surface and wear direction, the influence of carbide on wear will also be different:
(a) When the long axis direction of carbide is parallel to the wear surface, its wear resistance is higher than that perpendicular to the wear surface;
(b) When there is no preferred orientation of carbide relative to the wear surface, its wear performance is similar to that the long axis direction of carbide is perpendicular to the wear surface;
(c) When the long axis of carbide is parallel to the wear surface and perpendicular to the wear direction, it has the best wear performance.
The conclusions of Coronado J and Heino are slightly different from those of Dogan. Coronado J and others found that the wear resistance of M7C3 carbide perpendicular to the wear surface is better than that of M7C3 carbide and parallel to the wear surface, and the elastic modulus of longitudinal M7C3 carbide perpendicular to the edge of carbide is higher than that parallel to the edge of carbide, so the crack can expand more easily along the edge parallel to M7C3 carbide. Heino et al. Found:
(a) The long and thin carbides are perpendicular to the wear surface, which can avoid the abrasive scraping the wear surface for a long distance, so as to improve the wear resistance;
(d) When the carbide is parallel to the wear surface, the boundary area between the carbide and the matrix (as shown in Figure 4) is a high stress area, and the carbide is easy to crack; In addition, the boundary between carbide and matrix is also affected by high stress, which leads to the easy loosening of carbide;
(c) When the carbide is neither parallel nor perpendicular to the wear surface, the carbide will open to the surface after cracking, and the carbide will be replaced by abrasive; Depending on the carbide mesh, this replacement may take place over a long distance, adversely affecting the wear resistance.