One of the main purposes of low-pressure casting technology is to solve the contradiction between filling and feeding of the traditional gravity casting pouring system. Because the liquid metal fills the mold from the bottom to the top, the initial application of this technology is limited to light alloys such as aluminum alloy. Aluminum alloy has low density, low melting point, large demand for castings and wide sources of aluminum materials, so it has realized large-scale engineering application.
The Chinese patent cn 1483848a discloses a low-pressure cast aluminum alloy for the cylinder head of micro automobile engine. Its main chemical composition is Si, Cu and Mg, especially Cu and Mg are well controlled, and its harmful impurity elements are strictly controlled. After modification, modification and T6 heat treatment, the tensile strength of the alloy is higher than 300 MPa, and the Brinell hardness value Hb is 110. The alloy has sufficient strength and rigidity, It can meet the requirements of low pressure casting process and machining process of micro automobile engine cylinder head. Li Bin of Tsinghua University, etc. established the nucleation model of ZL114A aluminum alloy by low-pressure casting on the basis of a large number of experimental data statistical analysis. The main components of ZL114A aluminum alloy are al 7% (mass fraction), Si 0.5% (mass fraction), Mg, and the relevant thermodynamic and kinetic parameters were obtained, The macro solidification and microstructure evolution of the aluminum alloy were simulated by the improved cellular automata coupled with the finite difference method. Under the condition of fully considering the relevant solidification characteristic parameters, the change rule of the eutectic structure content of the aluminum alloy was obtained, and the simulation value was compared with the experimental value. The results show that the simulation and experiment are in good agreement.
Choong do Lee of Renhe University of technology in South Korea made A356 aluminum alloy (composition is shown in Table 2) by low-pressure casting, and obtained the parts with dense microstructure. The limit cycle times of resistance to cyclic fatigue failure were greatly increased compared with the traditional casting method (the cycle times of T6 heat-treated low-pressure cast aluminum alloy hub under 200MPa stress can reach 0.5 × 105).
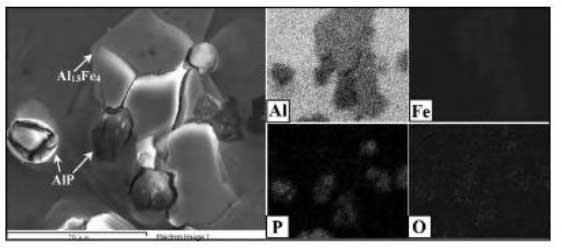
The D.M. maijer research team of the University of British Columbia in Canada has been focusing on the industrial application and development of computer numerical simulation technology in low-pressure casting aluminum alloy parts. Recently, they used numerical simulation technology to predict and analyze the defects of macro porosity, micro porosity and oxide film in the process of low-pressure casting aluminum alloy parts for automobile hub, and combined with the simulation results, they discussed how to optimize the actual low-pressure casting process parameters to reduce these defects and the overall performance of aluminum alloy parts. The results of numerical simulation show that the casting defects of aluminum alloy parts of automobile wheel hub mainly depend on the filling process and heat conduction process of liquid metal in the process of low pressure casting. During the filling process, the uncertainty of the gas movement track in the mold cavity is the main reason why the numerical simulation results of the filling process are difficult to match the actual low-pressure casting process, D. On the basis of considering the influence of gas inside the cavity on the filling process, the research team of M. maijer used the numerical simulation technology to optimize the pressure parameters of the filling process to obtain the flawless A356 aluminum alloy hub model, which was verified by experiments.
The State Key Laboratory of solidification technology of Northwest University of technology in China has carried out a systematic study on the low pressure casting process. Hao Qitang et al. Used ZL114A aluminum alloy as raw material to cast different thickness plate parts on the self-made low-pressure casting equipment, and studied the filling and solidification characteristics in the low-pressure casting process. The results showed that the actual filling speed of low-pressure casting was less than the theoretical given speed, and the more complex the mold cavity structure, the smaller the casting cross-sectional area, the greater the filling obstruction to the liquid metal, The slower the filling speed is, the better the resistance coefficient should be. The experimental results of different thick plates show that the whole filling process is stable without fluctuation and the occurrence of oxidation inclusions and air entrainment can be effectively reduced under the filling speed of 40mm / s. The solidification structure analysis shows that the casting has no defects and excellent microstructure and properties under this filling speed. The main reason is that on the one hand, the filling process of alloy liquid is sequential, on the other hand, the filling time of low-pressure casting is longer than that of gravity casting, which is conducive to the exhaust of air in the cavity. Li Jianfeng et al. [28] studied the solidification characteristics and filling rules of A357 Alloy under the condition of low pressure casting. The experimental results show that when the filling pressure is increased to 30 kPa and the rising liquid of the alloy liquid is stable and full of the cavity, the high-quality macromorphology, fine grain structure and excellent mechanical properties of the casting can be obtained. Through analysis, the flow law of liquid metal filling cavity is obtained: under the action of certain pressure, the liquid flow entering the cavity tends to maintain its movement direction and momentum, so as to form the undercurrent throughout the filled area. During the movement, the undercurrent constantly exchanges momentum with the surrounding medium, which results in the expansion of the undercurrent, the average flow velocity gradually decreases, and at the same time, eddy current movement occurs on both sides, When the undercurrent reaches the liquid surface, its velocity is still greater than zero, and the free liquid surface is convex, which results in the transverse flow area under the action of static pressure difference.
Huazhong University of science and technology has been developing the CAE software of low-pressure casting process numerical simulation for a long time, and applying the principle of numerical simulation to the continuous research on the filling and solidification process of low-pressure casting. Liao dunming, et al. Simulated the filling and solidification process of low-pressure casting by using the low-pressure module of Huazhu CAE, and the results were in good agreement with the reality. The practical application also showed that the low-pressure casting CAE can effectively evaluate the rationality of low-pressure casting process design. The basic principle of its simulation filling process is based on the incompressible unsteady flow of liquid metal with free surface viscosity. The mathematical description of its motion state needs to use momentum conservation equation, mass conservation equation and energy conservation equation. The movement of free surface is determined by solving volume function equation with SOLA-VOF method. The numerical simulation of two low-pressure castings, aluminum alloy volute and aluminum alloy hub, is carried out and compared with the actual situation. The results show that the two are consistent. Through the numerical simulation, the design of the gating system of low-pressure casting can be effectively improved and the casting quality can be improved.