Solid liquid segregation is a typical semi-solid defect in thick wall products. It refers to the uneven distribution of solid phase and liquid phase in semi-solid forming products. The uneven distribution of a-AI grains and eutectic phases in different regions of a sample can be observed under the micro electron microscope.
Researchers from the University of uzzburg, Germany, observed the process of solid-liquid separation in semi-solid slurry of al-ge32 alloy by using X-ray micro perspective technology, as shown in Fig. 1. The bright spot in the film is solid phase, and the black area is liquid phase. The solid-liquid separation will eventually lead to solid-liquid segregation. It is worth noting that al-ge32 alloy and alsi7 alloy have similar solid fraction and crystal structure.
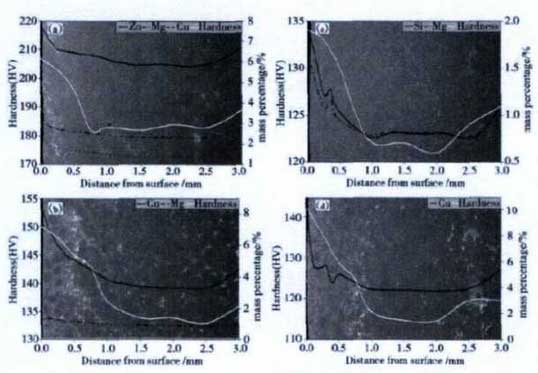
Guo Lijun et al. Studied the influence of process parameters on Si segregation in aluminum alloy during squeeze casting. The results show that pouring temperature, pressure, cooling rate and extrusion speed all have effects on Si segregation, and pouring temperature is the most significant factor. The increasing of pouring temperature will lead to the decrease of Si segregation. The segregation degree of high cooling rate mold is smaller than that of low cooling rate mold.
The researchers in South Africa studied the solid-liquid segregation in the outer layer of 7075 aluminum alloy, 2024 aluminum alloy, 6082 aluminum alloy and A201 aluminum alloy castings, as shown in Figure 2. The results show that the liquid segregation on the surface of ssm-hpdc alloy under as cast and T6 conditions results in significant differences in the properties between the casting surface and the casting body.
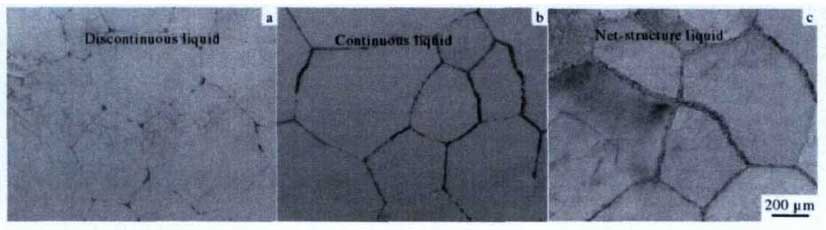
In addition, researchers from Pusan National University of Korea studied the effects of gate design and process parameters on solid-liquid segregation and mechanical properties of A356 aluminum alloy semi-solid die casting. The movement of solid particles in semi-solid slurry of aluminum copper alloy during compression was also studied by using X-ray. It was observed that the rearrangement of grains, such as translation and rotation, led to local expansion, and the resulting liquid rich in copper flowed into the expanded voids to form a local liquid component increase, resulting in solid-liquid segregation.
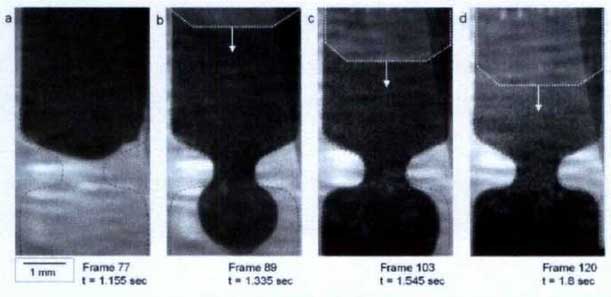
Some domestic scholars have studied the segregation of titanium alloy during semi-solid forging. The results show that slurry temperature is an important factor affecting the liquid distribution in semi-solid forging. The continuous increase of temperature leads to continuous precipitation of liquid phase at the grain boundary, as shown in Fig. 3. Finally, under the action of pressure, there are more liquid phases in the center of the casting. Compared with the layered casting process proposed by Li Jun and Wang Junge, the solid-liquid segregation in the casting can be effectively reduced. Jianbo, Wei Shenghui and others studied the influence of process parameters on the microstructure uniformity of 7075 aluminum alloy semi-solid casting and forging, as shown in Fig. 4. The experiment shows that the increase of alloy temperature will lead to the segregation of liquid phase. At the same time, in the semi-solid casting process, the flow front is mainly composed of liquid phase, which results in solid-liquid segregation in the last part of mold filling.