In the production practice, the shrinkage modulus method is mainly used to design the process riser to complete the feeding of cylinder block iron castings. The shrinkage modulus method follows the equilibrium solidification theory and considers that the shrinkage process of iron castings is a part of the solidification process. From the perspective of modulus, the modulus corresponding to the solidification time of iron castings is called the solidification modulus MC of iron castings, and the shrinkage time of iron castings is called the shrinkage modulus MP of iron castings. The shrinkage modulus MP and solidification modulus MC of castings meet the requirements
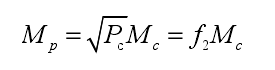
Where:
PC — contraction time fraction
F2 — shrinkage modulus coefficient
The solidification modulus MC is the overall modulus of the cylinder block cast iron, which is defined as
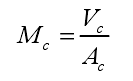
Where:
VC — casting volume (cm3)
AC — casting heat dissipation area (cm2)
The feeding condition of cylinder body iron castings is that the riser modulus of iron castings is greater than the solidification modulus of iron castings, i.e. Mr < MC. According to the equilibrium solidification theory, it is expressed as follows

Where:
VF — feeding liquid volume (cm3)
VP — safe liquid volume for forming feeding pressure (cm3)
F1 — riser balance coefficient, 1F = 1.2
F3 — feeding pressure coefficient, or safety factor, 3F = 1.1
In the actual casting production, the form of riser is mainly divided into square riser and cylindrical riser, and more concise calculation method can be used. For a square riser, if the length of the bottom edge of the riser is a and the height of the riser is h, then
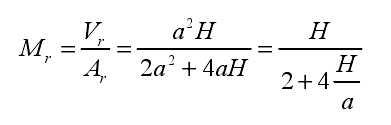
Where:
VR — riser volume of casting (cm3)
Ar — heat dissipation area of casting riser (cm2)
For the cylindrical riser, if the riser bottom edge length is r, the diameter is D, and the riser height is h, then there is
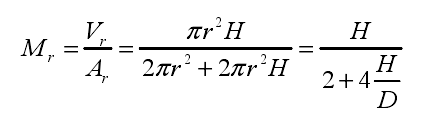
If the riser height diameter ratio (for square risers, the ratio of riser height to riser bottom length) is β, then there is
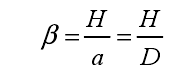
According to the formula, the shape of riser can be ignored
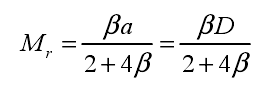
After using the shrinkage modulus method to design, it is necessary to check the riser size by using the feeding liquid quantity method to check whether the feeding liquid metal amount of the riser is enough. Namely
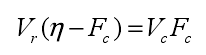
Where:
η — feeding efficiency of riser, generally taken as η = 0.17
FC — shrinkage ratio
VC — casting volume (cm3)
For gray cast iron, according to the relevant literature, the mathematical model of its shrinkage is as follows
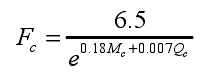
Where:
QC — quality perimeter quotient of iron castings (kg / cm3)
The quality perimeter quotient is defined as the ratio of the mass of the cast iron to the cubic power of its modulus
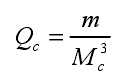
Where m — mass of cast iron (kg)
The shrinkage modulus method fully considers the characteristics of cylinder block iron castings in cooling and solidification stages, and refines the mathematical model that the shrinkage time of iron castings is less than its solidification time. The riser calculated by shrinkage modulus method is smaller than that calculated by other methods. This is mainly because shrinkage modulus method can not only fully feed but also avoid adverse effects such as thermal interference of riser, considering comprehensively solidification time and volume shrinkage of iron castings.