Introduction
Sand casting, as a time-honored metal forming technique, has been widely applied in various industries such as machinery manufacturing, automotive, aerospace, and other heavy industries due to its low cost and high adaptability to complex shapes. However, manufacturing complex structural components using sand casting poses several challenges, primarily in controlling cast quality and optimizing the casting process. Recent advancements in Computer Aided Engineering (CAE) technology, particularly the application of casting process simulation software, have offered new opportunities for improving the sand casting process design of complex structural components.
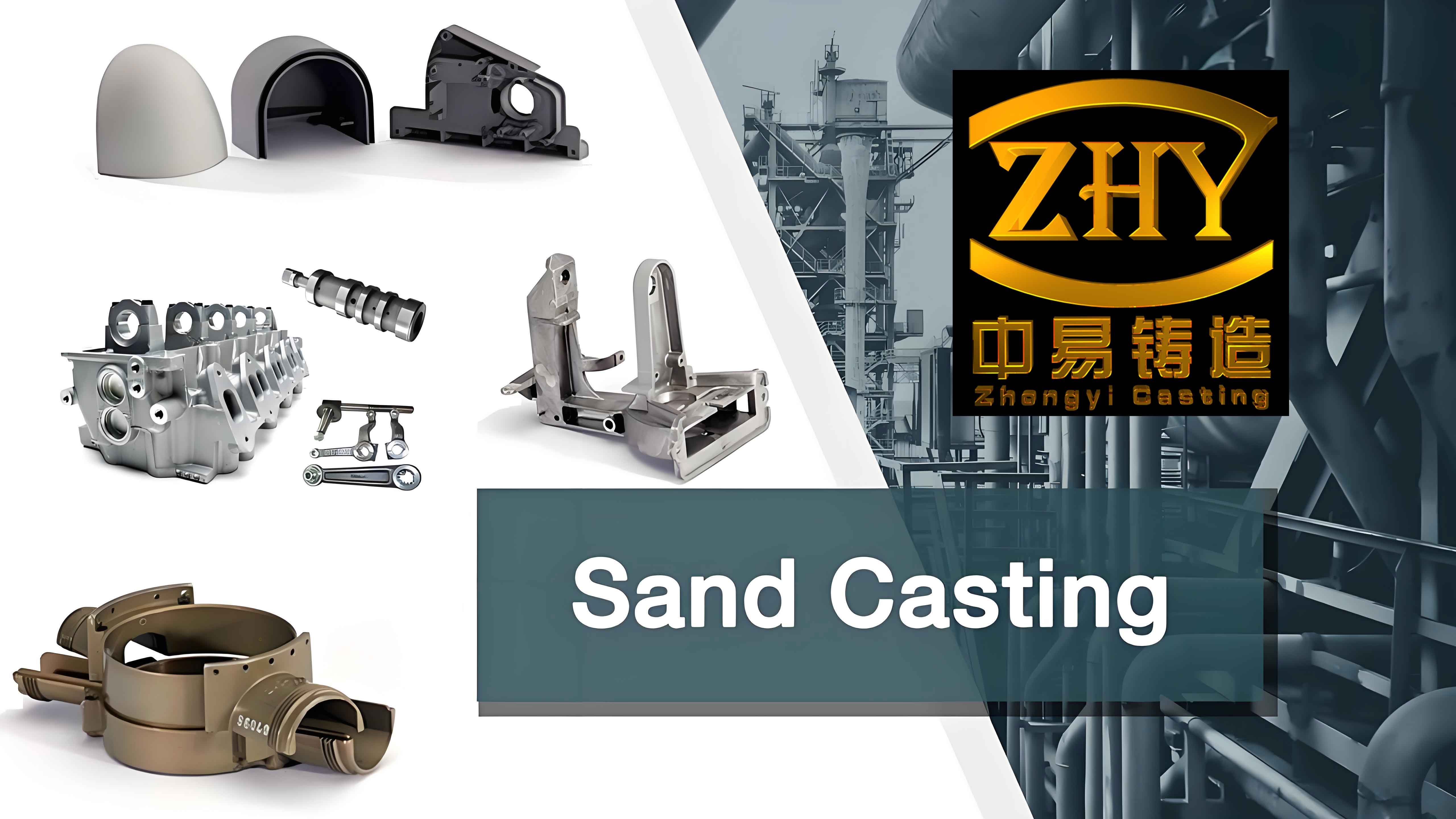
This article delves into the process design and simulation analysis of sand casting for complex structural components. We will discuss key aspects such as pouring position selection, parting surface determination, gating system design, and simulation-based optimization measures. The objective is to enhance the quality and efficiency of the sand casting process for complex components.
1. Sand Casting Process Design for Complex Structural Components
1.1 Introduction to Sand Casting
Sand casting is a metal casting process that utilizes sand as the molding material to create a mold cavity into which molten metal is poured to form the desired shape upon solidification. This process offers several advantages, including cost-effectiveness, flexibility, and adaptability to complex geometries. However, challenges such as porosity, inclusions, and shrinkage defects often arise, necessitating careful process design and optimization.
1.2 Key Considerations in Process Design
1.2.1 Selection of Furan Resin Self-hardening Sand
The use of furan resin self-hardening sand is a popular choice for sand casting, as it significantly reduces surface defects and enhances the overall density of the castings. The sand mixture typically comprises silica sand, furan resin binder, and a curing agent. The hardening process is triggered by the chemical reaction between the resin and curing agent, resulting in a strong, durable mold.
1.2.2 Dimensional Tolerances and Material Properties
For complex structural components, the selection of dimensional tolerances and material properties is crucial. A common dimensional tolerance grade for sand castings is CT11, which accounts for the free shrinkage of the casting during cooling. The mass tolerance (MT10) is typically set at ±4% of the casting weight to accommodate minor variations in production. Additionally, the material’s shrinkage rate (e.g., 0.9% for HT250 gray iron) must be carefully considered to prevent cracks or deformations during cooling.
1.3 Pouring Position Selection and Parting Surface Determination
1.3.1 Pouring Position Selection
The pouring position significantly influences the quality of the casting. For complex structural components, it is essential to select a pouring position that promotes efficient metal flow and minimizes defects. For instance, positioning the dovetail guide surfaces downward and large planar surfaces upward can leverage gravity to facilitate metal flow and prevent entrapped air or slag, thereby improving crystallization quality.
1.3.2 Parting Surface Determination
The parting surface, or mold line, separates the mold into two or more sections for easy removal of the casting. For complex components, the parting surface should be carefully selected to minimize core printing, ensure proper gating, and facilitate casting removal. Commonly, the parting surface is chosen along natural break lines or planes of symmetry to optimize the casting process.
1.4 Gating System Design
The gating system is a vital component of the sand casting process, as it governs the flow of molten metal into the mold cavity. A well-designed gating system ensures even filling, reduces turbulence, and facilitates effective feeding to prevent shrinkage defects.
1.4.1 Ingate Design
The ingate, or pouring sprue, connects the ladle or pouring basin to the mold cavity. Its design must balance metal flow velocity, turbulence minimization, and adequate feeding. A common approach for complex components is to use a stepped or inclined ingate design that gradually fills the mold cavity from bottom to top.
Ingate Type | Description | Advantages |
---|---|---|
Stepped Ingate | Gradually tapers to control flow velocity and reduce turbulence. | Even filling, reduced turbulence, improved feeding. |
Inclined Ingate | Angled to promote laminar flow and facilitate gas escape. | Minimizes entrapped air, reduces porosity. |
1.4.2 Runner and Riser Design
Runners distribute molten metal from the ingate to the mold cavity, while risers provide additional metal to compensate for shrinkage during solidification. Riser placement is critical, often located above critical sections or thick-walled areas to ensure adequate feeding.
Component | Function | Design Considerations |
---|---|---|
Runner | Metal distribution | Even distribution, minimal turbulence, appropriate cross-section. |
Riser | Shrinkage compensation | Strategic placement, sufficient size, and volume to compensate for shrinkage. |
2. Simulation Analysis for Complex Structural Components
2.1 Introduction to Simulation Analysis
Simulation analysis plays a pivotal role in optimizing the sand casting process for complex structural components. By leveraging casting simulation software (e.g., AnyCAST, ProCAST, MAGMASOFT), engineers can visualize and analyze the filling and solidification phases, identify potential defects, and make data-driven design modifications.
2.2 Preliminary Simulation Analysis
2.2.1 Filling Simulation
Filling simulation reveals the flow path, velocity, and temperature distribution of molten metal within the mold cavity. This information is crucial for identifying regions prone to turbulence, cold shuts, and entrapped gas.
Simulation Parameter | Description | Importance |
---|---|---|
Flow Velocity | Speed of metal flow | Identifies regions prone to turbulence. |
Temperature Distribution | Temperature variations during filling | Assesses the risk of cold shuts. |
Gas Entrapment | Potential regions for gas entrapment | Predicts porosity and blowholes. |
2.2.2 Solidification Simulation
Solidification simulation provides insights into the cooling phase, including temperature gradients, solidification rates, and shrinkage tendencies. This data is essential for evaluating thermal stress development and predicting shrinkage defects.
Simulation Parameter | Description | Importance |
---|---|---|
Temperature Gradients | Variations in cooling rates | Affects microstructure and mechanical properties. |
Solidification Sequence | Order of solidification | Ensures adequate feeding and minimizes shrinkage defects. |
Shrinkage Tendencies | Regions prone to shrinkage porosity | Guides riser placement and size optimization. |
2.3 Process Optimization Measures
Based on simulation results, several optimization measures can be implemented to enhance casting quality and process efficiency.
2.3.1 Gating System Modification
Redesigning the gating system, including ingates, runners, and risers, can improve metal flow and feeding efficiency. Adjustments to ingate position, size, and shape can mitigate turbulence and promote even filling.
Optimization Measure | Description | Benefit |
---|---|---|
Ingate Repositioning | Moving ingate to improve flow dynamics. | Enhances filling quality, reduces turbulence. |
Runner Reconfiguration | Adjusting runner cross-sections and angles. | Ensures even metal distribution, minimizes turbulence. |
Riser Optimization | Strategic placement and sizing of risers. | Provides adequate feeding, prevents shrinkage defects. |
2.3.2 Riser Addition and Optimization
Adding or modifying risers can effectively capture slag and gas during pouring and provide additional metal to compensate for shrinkage. Optimal riser placement and sizing are crucial to prevent internal defects in large or thick-walled castings.
Riser Optimization Aspect | Description | Benefit |
---|---|---|
Placement | Strategic location above critical sections. | Ensures adequate feeding, prevents shrinkage defects. |
Size and Volume | Sufficient size to compensate for shrinkage. | Minimizes internal porosity, enhances cast integrity. |
2.3.3 Use of Chills
Chills accelerate cooling in specific regions, refining microstructures and enhancing mechanical properties. Placement of chills in thick or complex areas can reduce internal stresses and prevent hot tearing.
Chill Application | Description | Benefit |
---|---|---|
Strategic Placement | In thick or hotspots. | Accelerates cooling, reduces porosity, and hot tearing. |
Material Selection | High thermal conductivity materials. | Enhances cooling efficiency, refines microstructure. |
2.3.4 Optimization of Solidification Sequence
Controlling the solidification sequence ensures that critical sections solidify first, improving overall cast integrity. This can be achieved by adjusting pouring temperature, pouring rate, and cooling conditions.
Optimization Strategy | Description | Benefit |
---|---|---|
Pouring Temperature | Adjusting to optimize filling and feeding. | Ensures even filling, minimizes turbulence. |
Pouring Rate | Managing flow velocity. | Prevents entrapped air and slag. |
Cooling Conditions | Modifying cooling rates and environments. | Controls thermal stress, minimizes cracking. |
3. Case Study: Optimization of a Complex Aerospace Component
3.1 Initial Process Design
A hypothetical complex aerospace component with intricate internal passages and thin-walled sections was selected for analysis. The initial process design involved a conventional gating system with a single ingate and runners. However, simulation analysis revealed significant turbulence and potential cold shuts in specific regions.
3.2 Simulation Results and Optimization
3.2.1 Filling Simulation
The filling simulation highlighted regions with high turbulence and potential cold shuts. Based on these findings, the ingate position was adjusted, and additional runners were introduced to distribute metal more evenly.
3.2.2 Solidification Simulation
Solidification simulation identified hotspots and shrinkage tendencies . To address these issues, strategic risers were added above critical sections, and chills were placed in thick-walled areas.
3.3 Process Optimization and Validation
After implementing the optimization measures, a revised simulation was conducted to verify the effectiveness of the changes. The results demonstrated significantly improved filling and solidification characteristics, with reduced turbulence, even metal distribution, and minimized shrinkage tendencies.
3.4 Final Casting Results
The optimized process was then implemented in production, resulting in castings with excellent surface finish, minimal defects, and enhanced mechanical properties. Non-destructive testing (NDT) and dimensional inspections further validated the quality of the final castings.
4. Conclusion
The integration of modern numerical simulation techniques into traditional sand casting processes for complex structural components has significantly enhanced casting quality and process efficiency. By leveraging simulation software, engineers can identify potential defects, optimize gating systems, and fine-tune process parameters. This approach not only reduces the number of trial castings but also accelerates the development cycle, leading to cost savings and improved competitiveness.