The simulation results show that the safety height of riser is 11.15cm, which is 8.15cm higher than the minimum safety height of 3cm. At the same time, because the process parameters in the actual production process are dynamic values rather than a constant value set by the simulation software, there is always a certain error range between the test results and the production results.
In order to improve the fault tolerance rate of the process scheme and ensure the quality of steel castings, the riser safety height is set to 5cm, that is, the optimized riser height is reduced by 6cm compared with the original scheme. At this time, the process yield is increased from 55% to 60%, but it is still low.
In order to continue to improve the feeding distance and feeding effect of risers, external cold irons were set at the bottom and side of the casting respectively to speed up the local cooling rate and strengthen the sequential solidification conditions. The external cooling iron can be divided into direct external cooling iron and indirect external cooling iron. Because there is a coating shell on the outside of EPC mold, the external cold iron can not directly contact with the casting. However, the influence of coating shell on the interface heat transfer is ignored in this simulation scheme, and the material of cold iron is carbon steel.
For the thickness of external cooling iron, when the thickness increases, the heat capacity increases and the chilling effect will be enhanced. However, when the thickness increases to a certain value, the solidification rate of molten steel will not increase any more. In production practice, the diameter of hot spot circle of steel castings with the thickness of external chill 0.3 ~ 0.8 times is generally taken.
According to the above design principles, a 270mm long, 120mm wide and 150mm thick external cold iron is set at the bottom of the casting according to the above design principles; two pieces of external cooling iron with length of 110mm, width of 100mm and thickness of 50mm are set on both sides of the long side. Because the cold iron increases the feeding distance of the riser, the size of the new round riser is 200 mm × 300 mm × 300 mm, and the process yield is increased to 65%.
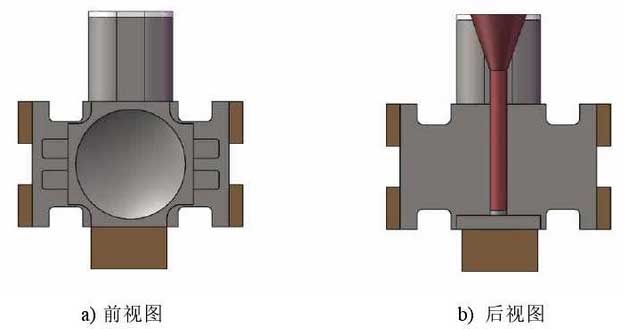