Drawing is to adjust the taper of the mold or casting surface so that the mold and product can be demoulded smoothly from the mold. The minimum draft angle of the model mainly depends on the height of the model. It is generally believed that the higher the height is, the smaller the draft angle is required. The draft angle is also affected by the model material, surface finish, model characteristics, sand quality and compaction pressure. The experience of increasing draft angle for disa line mold is as follows: use positive draft as much as possible, that is, the product size will increase after increasing the draft angle, and the angle can be selected according to the following table. The purpose is that the far end dimension deviation is not more than 1 mm. Fig. 1 defines the recommended value of draft angle for product features at different heights.
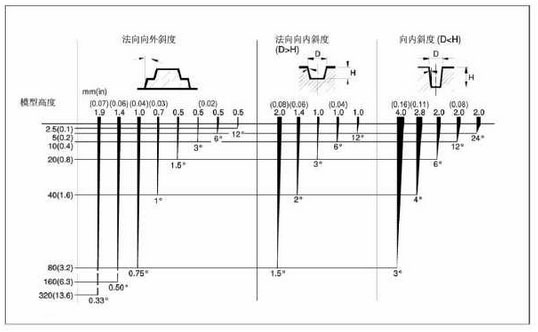
Due to the vertical parting characteristics of disa line, it is easy to see the phenomenon of sand shooting not solid inside the deep pit on the mold plate, which leads to the reduction of sand mold strength and the casting defects such as box expansion or mechanical sand sticking. Therefore, the selection of the main parting surface is very important. The main parting surface should choose the plane close to the geometric center of the part as far as possible to ensure the uniform distribution of the features on both sides of the parting surface. If the inevitable surface parting occurs, the area and draft of the deep cavity area should be enlarged as much as possible, and the fillet of the transition surface should also be enlarged as much as possible, so as to provide help for the filling and demoulding of molding sand. Figure 2 shows the parting surface design of the brake caliper casting.
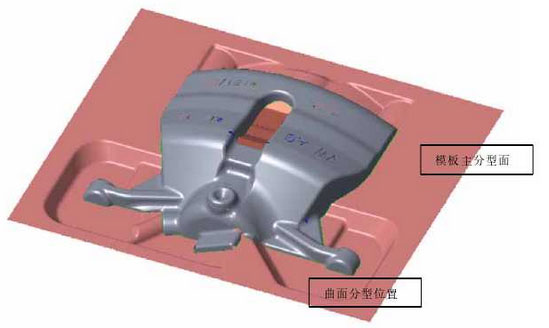