The feeding riser must be large enough to supply additional liquid metal during liquid shrinkage until the temperature drops below the solid phase line and the parts begin to solidify. In the same way, the modulus can be used to evaluate the shrinkage of riser,
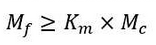
MC is the modulus of casting, MF is the modulus of riser, KM is a constant, which is obtained by experimental method and depends on the thermal conditions of pouring process and solidification characteristics of different alloys. The empirical values of constant km for different alloys are as follows:
(1) The hypoeutectic gray cast iron is 0.6-1.0
(2) The ductile iron is 0.8-1.1
(3) Malleable cast iron is 1.2-1.4
(4) The steel is 1.2-1.4
(5) Copper alloy is 1.2-1.4
(6) The aluminum alloy is 0.8-1.1
It is also related to the cold / hot riser, alloy composition, melting process, pouring time and mold quality.
The riser is not a product and has no value. Therefore, considering the economy of the riser, the riser with appropriate volume should be selected. Under the condition of the same modulus, the volume of the spherical riser is the smallest. According to the shape of different risers, different feeding metal utilization rates can be obtained. Figure 1 shows the feeding metal utilization rates of different riser shapes.
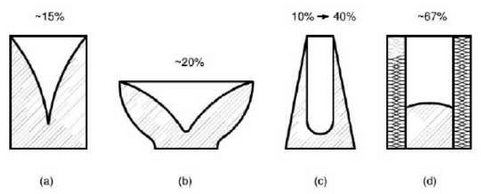
According to the parting surface design of brake caliper parts and the position of riser arrangement, we choose cylindrical riser. The filling ratio of liquid metal increases with the increase of riser modulus. In order to facilitate calculation, we choose 15%. We can see that different alloys have different shrinkage percentage, and the minimum volume of riser can be calculated by the following formula:
15% × riser volume (or weight) ≥ alloy shrinkage% × pouring volume (or weight)
or
Riser volume (or weight) ≥ alloy shrinkage factor × pouring volume (or weight)
In addition, the upper edge of the riser must be higher than the casting, otherwise there is not enough pressure to feed the molten iron into the casting for feeding, and even the phenomenon of reverse feeding of the riser may occur.