Semi solid processing is a new technology with rapid development at present. Due to the high quality characteristics of squeeze casting products, semi-solid squeeze casting (or semi-solid forging) has attracted the attention of the industry, and has some development in recent years.
The new process of unrc semi-solid rheocasting developed by Yubu company of Japan is combined with VSC and HVSC squeeze casting machines produced by Yubu company of Japan to form a whole semi-solid squeeze casting production line.
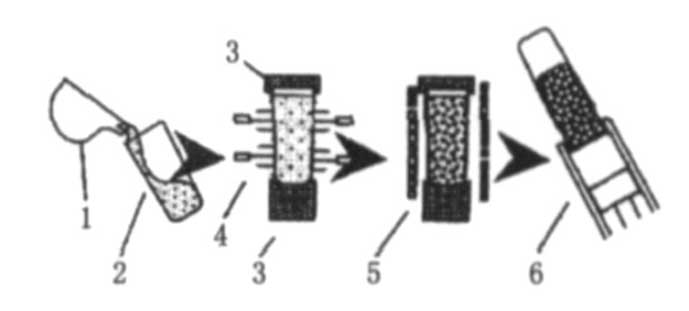
This process is suitable for the production of cast aluminum alloy, deformed aluminum alloy and magnesium alloy castings. Its mechanical properties are slightly higher than that of squeeze casting, and its production cost is lower than that of squeeze casting. It is a low-cost semi-solid process.
Based on the dxhv and DxV squeeze casting machines designed and manufactured by Toshiba company of Japan, a cooling and temperature control system is added to the squeeze cylinder, so that the liquid metal input by the electromagnetic pump through the pipeline is cooled and temperature controlled in the squeeze cylinder, and then the semi-solid metal is extruded and filled by the punch and solidified under pressure. This equipment realizes the whole production process of semi-solid squeeze casting without adding other devices. The A356 and A357 Alloy Automobile parts developed by this process have good performance and have been used in Nissan automobile.
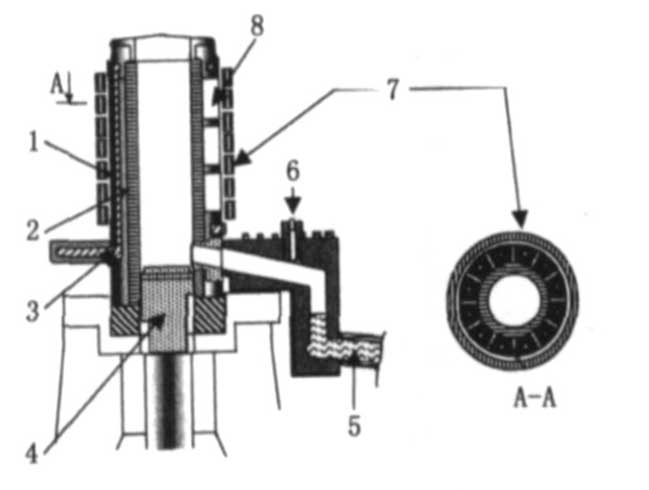
In general, the semi-solid slurry (Billet) prepared by various methods can be used to form parts by squeeze casting process. At present, the semi-solid extrusion casting aluminum alloy products researched and developed at home and abroad include A356 aluminum hub, A357 automobile knuckle, ZL117 high silicon aluminum piston, Y112 automobile intermediate shaft plug and air compressor aluminum piston, swashplate, connecting rod, etc.