(1) The simulation analysis diagram of scheme I is the simulation result of solidification process of scheme I. It can be seen from the diagram that the total solidification time of the casting is about 313 min, that is to say, when the solidification time reaches 313 min, all the metals in the liquid state will become solid, forming the casting. It can be seen from the solidification process that the solidification of the spokes of the big gear is faster, because the size of these positions is smaller, and the solidification time is shorter in the whole solidification process of the casting. At the early stage of solidification, these positions start to solidify, and the solidification is very fast. After continuous solidification of the casting for 100 min, all the spokes of the gear wheel are basically solidified, and only the gear wheel rim is not solidified. In addition, it can be seen from Fig. 3B that the display color of all risers is very light, especially the center of the riser. From the color bar beside, the lighter the color is, the longer the solidification time is, so the longest solidification time of the riser, which meets the requirements of casting solidification. It can also be seen from Fig. 3C that all risers can meet the feeding requirements during casting solidification. However, after defect prediction, it is found that there are defects in the spokes of the big gear (the junction of spokes and each sprue), as shown in Figure D.
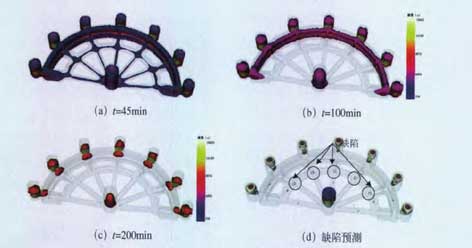
From the simulation results of scheme 1, it can be seen that the gating system can basically meet the casting of the casting, especially the feeding system, and the evenly distributed risers can achieve the purpose of feeding according to the design idea. However, there are still defects in the casting. From the location of the defects, it can be analyzed that the casting defects in this location are due to the insufficient feeding capacity of the internal sprue. However, in practice, it is not possible to design the runner very much, but according to the actual situation of the casting. So, the key to solve this problem is to increase the feeding capacity of the internal sprue. For this reason, we optimized the pouring system, that is, to increase the feeding capacity of the internal sprue, that is to say, to find a way to extend the solidification time of the internal sprue. Therefore, we changed the internal sprue in the pouring system into the thermal insulation sprue, that is, to form the pouring system with refractory materials, so as to achieve the purpose of thermal insulation of the liquid metal. As shown in Figure 4, the scheme of adding thermal insulation material to the pouring system.
(2) The simulation analysis diagram of scheme II shows the simulation results of solidification process of scheme II. From the simulation results, it can be seen that the basic solidification process of the casting has not changed, and the total solidification time is basically the same as that of scheme I. It can be seen that the effect of the gating system plus heat preservation on the solidification of other parts of the casting is not significant, only prolonging the solidification time of the gating system. It can be seen from Fig. B that the solidification time of the internal sprue is prolonged in scheme II due to the addition of thermal insulation materials when the solidification time is 100min. It can be seen from figure d that the gating system with thermal insulation material can supply the liquid metal needed for solidification at the spokes of the big gear. Therefore, the solidification simulation results show that there are almost no defects in the casting, indicating that the improvement of the process has indeed played an optimization role.
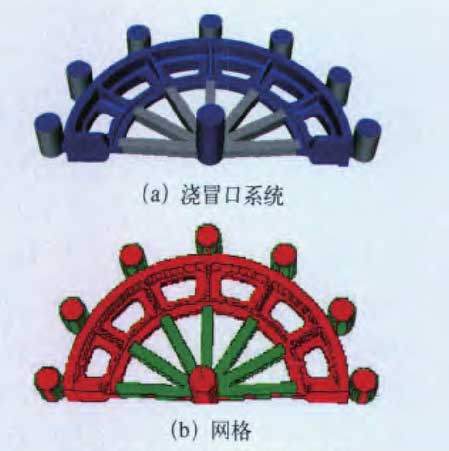
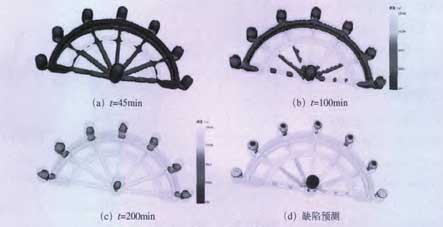
(1) The feeding system and pouring system of large cast steel gear in rotary kiln are designed by using casting simulation software. Scheme one can basically meet the requirements of casting solidification. However, due to the insufficient feeding capacity of the pouring system, a small amount of defects appear at the junction of the inner runner and the spoke.
(2) By designing the inner runner as a gating system with heat preservation effect, the defects in scheme I are effectively reduced, and the method can meet the feeding requirements of the casting during solidification.