1. Temperature analysis during the filling process
The filling process results of the two casting methods by the casting products manufacturers are shown in Figures 1 and 2. In the initial filling stage of the top injection system, the metal liquid is directly injected into the mold cavity through the sprue, and under the action of gravity, it produces a significant impact on the mold cavity; When the filling time reaches 9.93 seconds, due to the complex internal structure of the coal mining machine rocker arm shell castings produced by the casting products manufacturers, multiple liquid flows collide and converge in the mold cavity, resulting in poor filling stability; At the bottom of the coal mining machine rocker arm shell castings produced by casting products manufacturers, due to the thin wall thickness of the end faces on both sides of the motor hole, the flow rate of the molten metal is slowed down, making it difficult to fill the mold; When the time reaches 35.26 seconds, the metal liquid begins to fill the upper surface riser; At 49.63 seconds, the metal liquid has filled the entire shell mold. The temperature at which the casting products manufacturers produces the coal mining machine rocker arm shell casting is above the liquidus line. The casting products manufacturers can smoothly fill the coal mining machine rocker arm shell casting.
During the initial filling stage of the bottom injection system, a portion of the molten metal is injected from the bottom of the mold cavity, while another portion is injected from the middle of the mold cavity through the transverse runner. When the filling time reaches 9.86 seconds, due to the height difference, the molten metal injected from the middle converges towards the bottom. In the middle stage of filling, the metal liquid level inside the mold cavity rises steadily and has good stability. In the later stage of filling, when the time reaches 34.67 seconds, the metal liquid begins to fill the upper surface riser. At 50.35 seconds, the metal liquid fills the entire shell mold, and the casting products manufacturers produces a coal mining machine rocker arm shell casting with a temperature above the liquidus line.
The bottom pouring system improves the filling efficiency by simultaneously injecting two horizontal pouring channels at the middle bottom. The bottom pouring is conducive to the discharge of gas in the mold cavity, and the filling process is stable, effectively reducing the probability of defects such as insufficient pouring, curling, and inclusions. The overall filling effect is good.
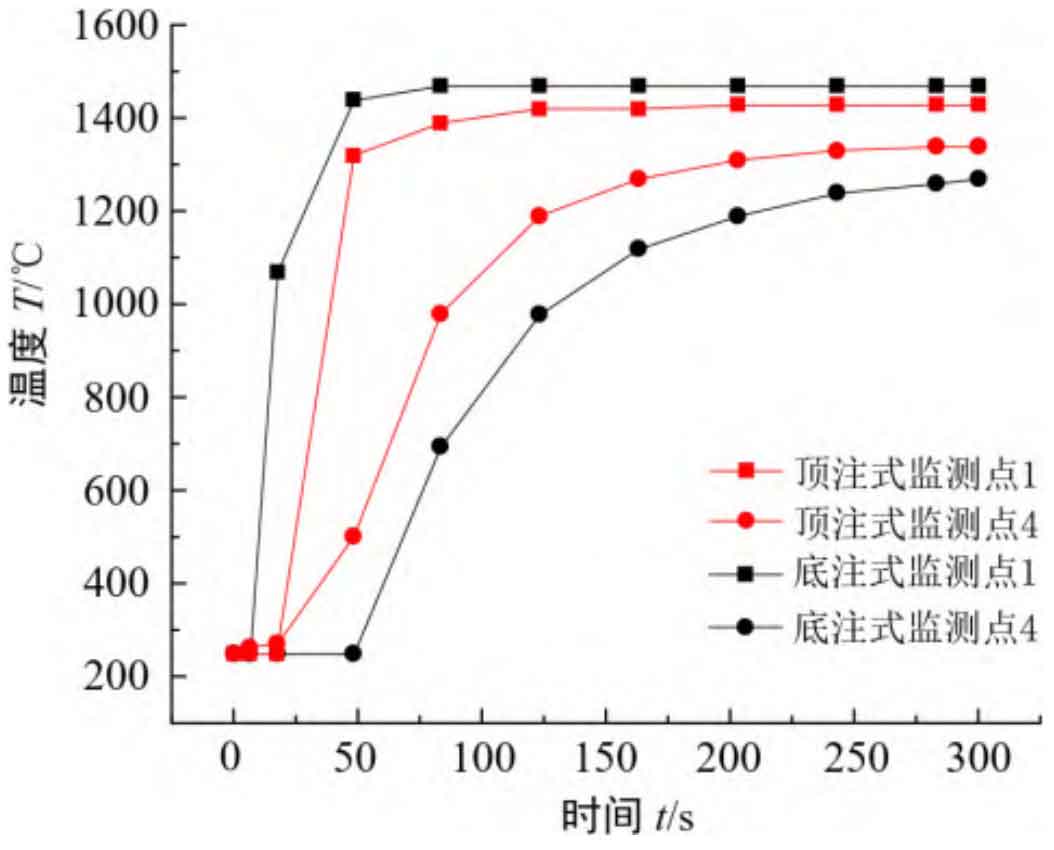
The rocker arm shell mold will experience drastic temperature changes after contact with the molten metal. Monitoring points 1 and 4 at the same position as the shell are selected in the inner cavity of the mold for observation in both pouring methods. The temperature variation curve of the monitoring points during the metal liquid filling stage is shown in Figure 3. Monitoring point 1 first came into contact with the molten metal, and then the temperature rapidly increased. At 48 seconds, the temperature approached its peak. At this time, the temperature of top injection monitoring point 1 was 1320 ℃, and the temperature of bottom injection monitoring point 1 was 1440 ℃. After 48 seconds, the temperature growth trend gradually slowed down. Monitoring point 4 is the final filling position of the metal liquid, and the temperature starts to rise relatively late without a sudden upward trend. When the time reaches 300 seconds, the temperature of top injection monitoring point 4 is 1340 ℃, and the temperature of bottom injection monitoring point 4 is 1270 ℃. By comparing the filling temperature, it can be seen that the bottom injection system has a larger temperature difference during the filling process compared to the top injection system.
2. Solid phase fraction analysis during solidification process
Through numerical simulation of the solidification process of the coal mining machine rocker arm shell castings produced by casting products manufacturers, the solidification field sections of the coal mining machine rocker arm shell castings produced by casting products manufacturers with a solid phase ratio of 50% and 90% are shown in Figures 4 and 5. The solidification methods of the coal mining machine rocker arm shell castings produced by casting products manufacturers are basically the same under the two pouring methods.
When the solid phase ratio reaches 50%, the shell casting of the shearer rocker arm produced by the casting products manufacturers is in the solidification shrinkage stage, and the shell solidifies from the bottom to the top; When the solid-phase ratio reaches 90%, the castings of the shearer rocker arm shell produced by the casting products manufacturers have basically solidified. However, there is a clear isolated liquid phase zone at the bottom thick wall position of the output end of the rocker arm shell. At this time, the top riser has solidified, making it impossible to supplement the central thick wall position of the shearer rocker arm shell castings produced by the casting products manufacturers. Therefore, it may lead to a higher probability of shrinkage and porosity in the shearer rocker arm shell castings produced by the casting products manufacturers.
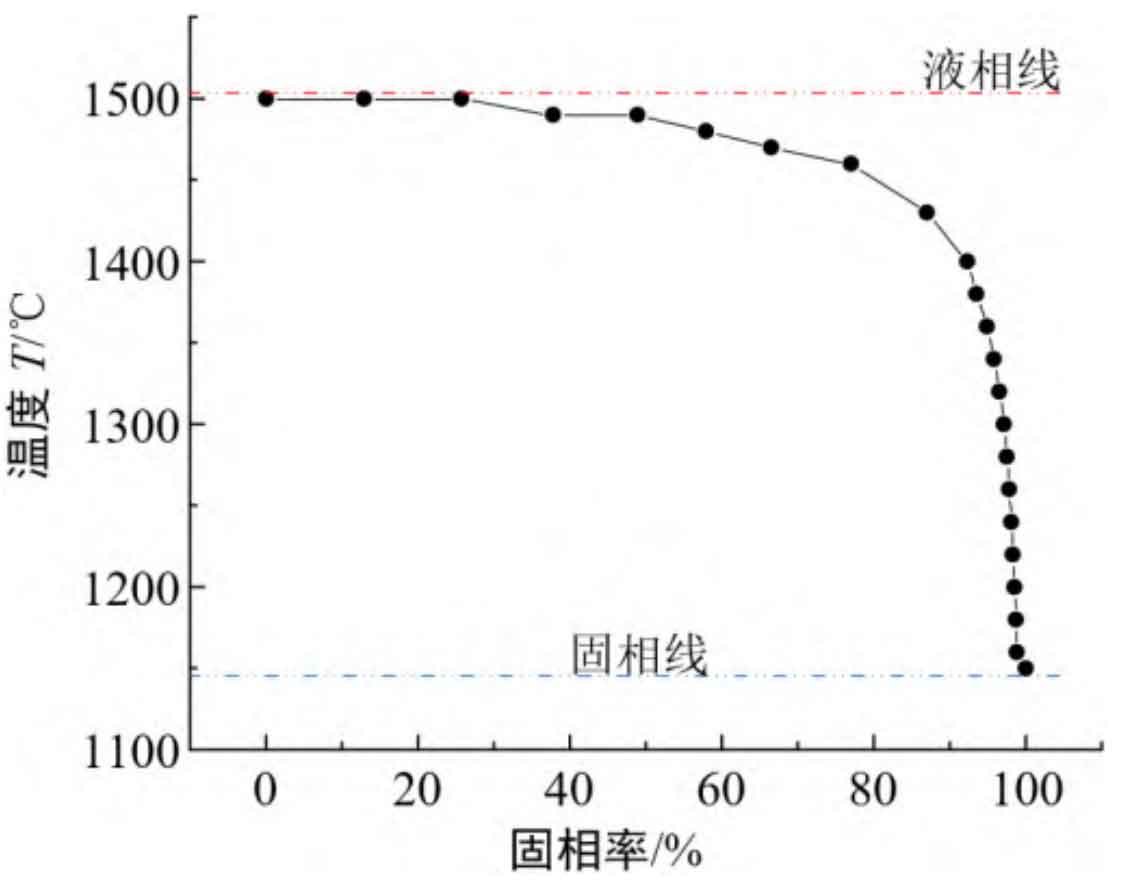
The curve of solid-phase ratio and temperature change of molten metal is shown in Figure 6. From Figure 6, it can be seen that after the metal liquid is injected into the mold cavity, there will be a more intense heat exchange between the metal liquid and the mold. When the temperature does not drop below the solidus line, the coal mining machine rocker arm shell castings produced by the casting products manufacturers are always in a solid-liquid coexistence state. When the solidus rate exceeds 80%, the temperature begins to rapidly drop to the solidus line.
3. Defect prediction analysis
After the complete solidification of the coal mining machine rocker arm shell castings produced by casting products manufacturers, the distribution of shrinkage porosity and shrinkage holes is shown in Figure 7. The internal shrinkage holes of the coal mining machine rocker arm shell castings produced by casting products manufacturers are relatively few and mainly distributed at points A and B with thicker inner walls. Due to the inconsistency between the solidification speed at points A and B and the surrounding structure, the molten metal cannot be effectively replenished, resulting in casting defects. This phenomenon is consistent with the simulation results of the solidification field. The top injection coal mining machine rocker arm shell castings produced by casting products manufacturers have a shrinkage volume of 143.41 cm3, accounting for 0.0775% of the rocker arm shell volume. The bottom injection rocker arm shell castings have a shrinkage volume of 133.57 cm3, accounting for 0.0721% of the rocker arm shell volume. From this, it can be seen that the bottom injection process scheme produces less shrinkage and porosity defects than the top injection process scheme.
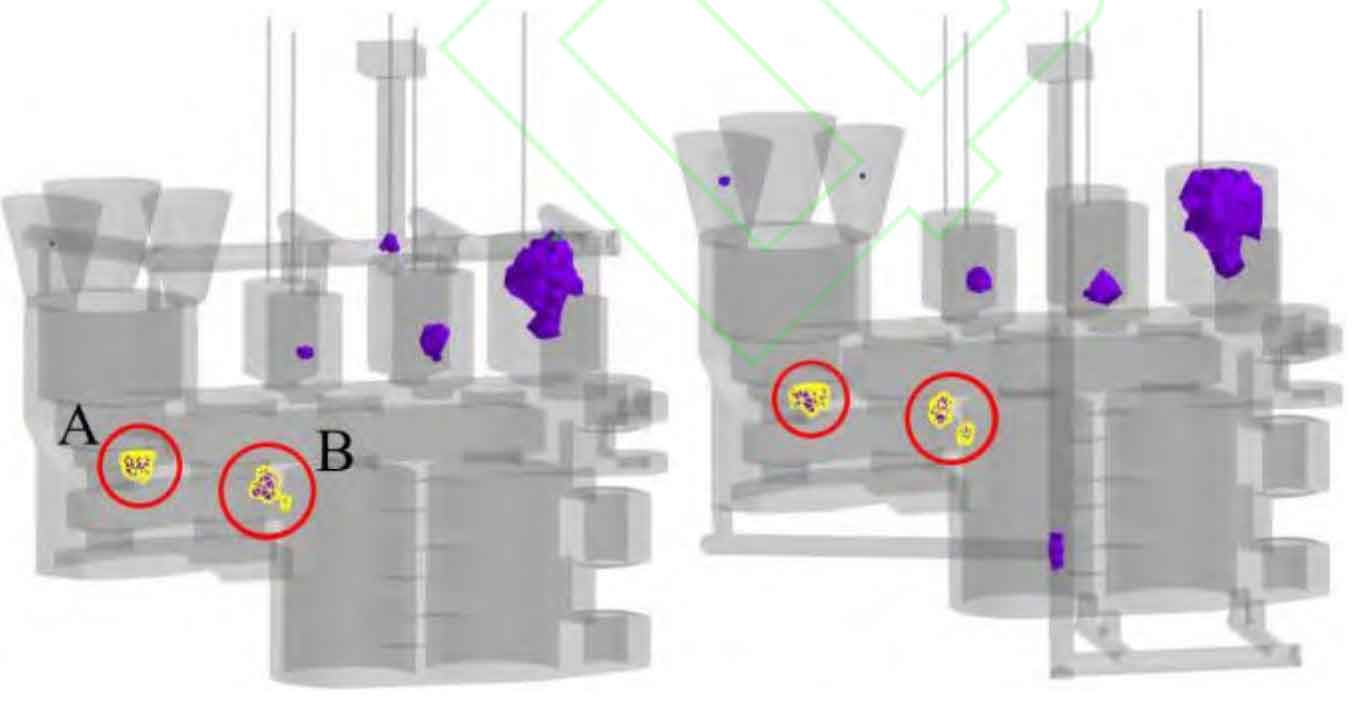
Through the analysis of filling, solidification, and defects of the rocker arm shell, it can be concluded that the bottom pouring process scheme produces fewer defects in the rocker arm shell, and the casting effect of the rocker arm shell produced by the casting products manufacturers is better. It is known that there are shortcomings in the process design of the pouring system, which lays the foundation for further optimizing the chemical process design.
4. Stress Field Analysis
Due to the fact that casting thermal stress is the root cause of residual stress in the rocker arm shell and will accompany the entire life cycle of rocker arm shell manufacturing and service, in order to study the stress field during the solidification and cooling process of the rocker arm shell castings produced by casting products manufacturers, a stress field analysis was conducted on the rocker arm shell cast using the bottom injection process scheme.
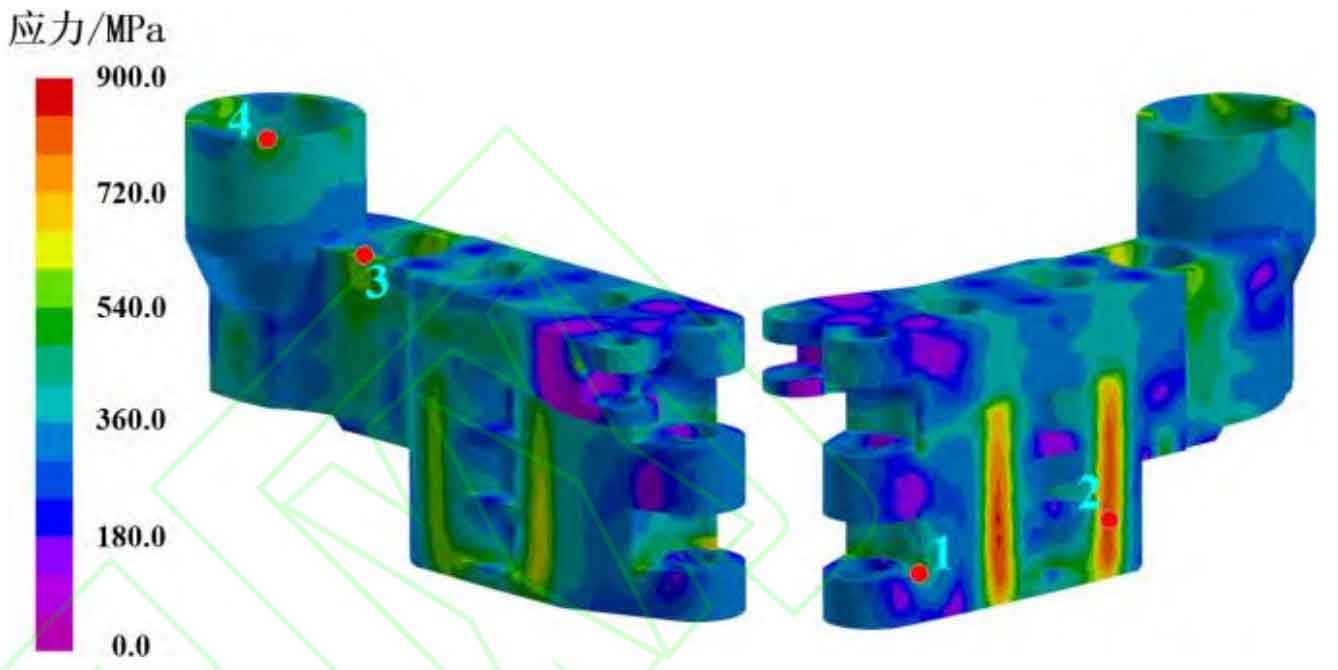
The stress distribution of the coal mining machine rocker arm shell castings produced by casting products manufacturers is shown in Figure 8 when the casting is completely solidified after 28211 seconds and the cooling time reaches 50000 seconds. The stress over time curves at four monitoring points are shown in Figure 9. When the cooling time reaches 33100 seconds, the temperature cools to 867 ℃. Due to changes in the internal temperature distribution and material properties of the coal mining machine rocker arm shell castings produced by the casting products manufacturers, the microstructure of the materials changes. The coal mining machine rocker arm shell castings produced by the casting products manufacturers will experience a brief stress release, as shown in Figure 9. At the same time, the stress at each monitoring point will experience a cliff like decrease, and then continue to increase.
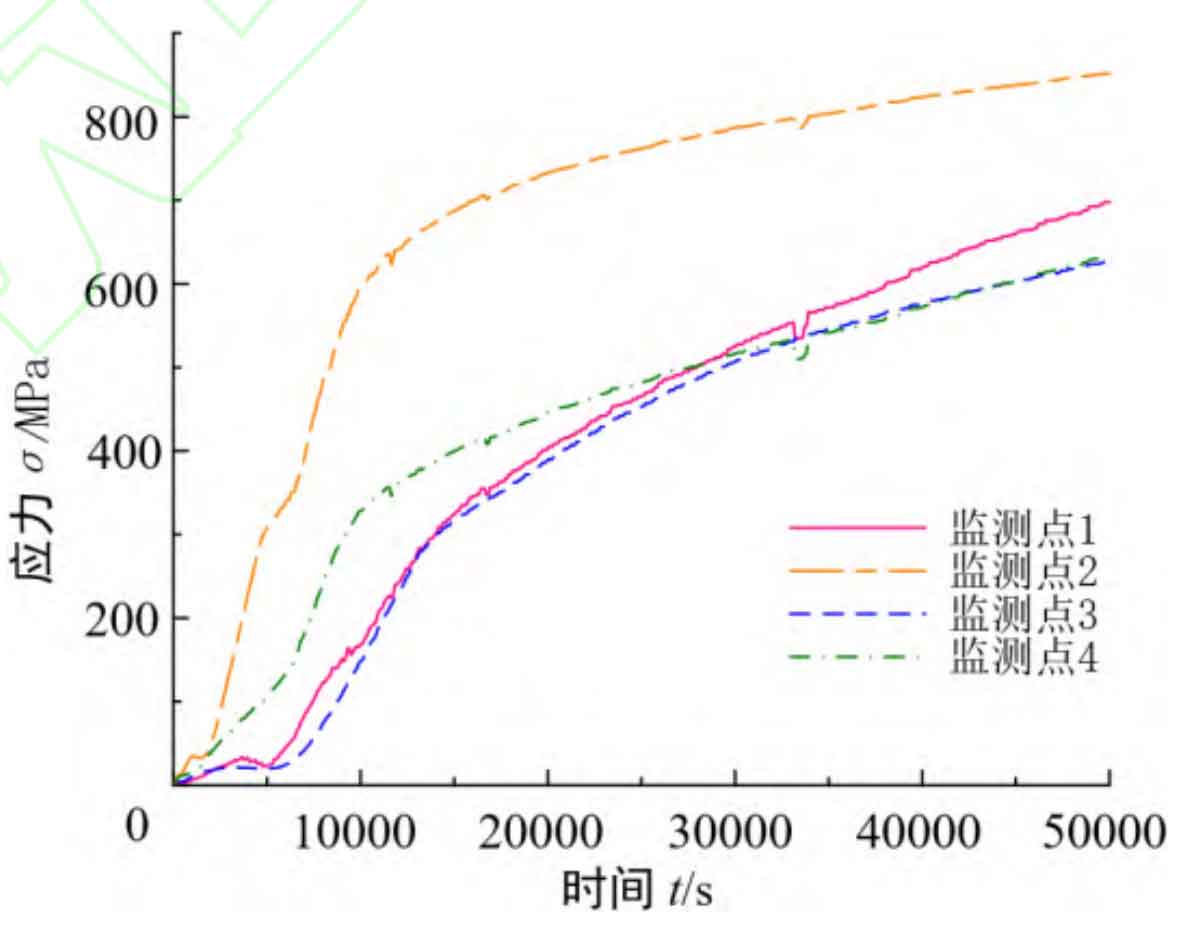
After the coal mining machine rocker arm shell castings produced by casting products manufacturers have completely solidified, the stress is most significantly concentrated in the motor hole, connecting shaft hole, idler shaft hole, output end hole, and other positions, as shown in Figure 8. The stress value of monitoring point 2 at the end of the motor hole is 850 MPa, and the stress value of monitoring point 1 at the pin shaft hole of the shell and the body is 696 MPa. The stress value of monitoring point 3 at the rear idler shaft hole of the output end of the shell is 625 MPa, and the stress value of monitoring point 4 at the output end hole of the shell is 632 MPa. After complete solidification, there is a significant concentration of residual stress at the thin-walled and variable cross-section of the rocker arm shell with significant thickness differences. Some stress distributions exceed the maximum tensile strength of the material. Therefore, as the casting of the rocker arm shell produced by the casting products manufacturers further cools down, the probability of defects such as tensile cracks will also increase.