1. Introduction
The coupler is a crucial component in the railway system, connecting train carriages and locomotives, ensuring the safe operation of the train. The performance of the coupler directly affects the safety and reliability of the entire train. In this article, we focus on the simulation of working stress and fatigue life of investment casting locomotive couplers.
1.1 Importance of Coupler in Railway System
The coupler is responsible for transmitting the forces between adjacent vehicles, especially during the start, stop, and acceleration/deceleration of the train. Any failure in the coupler can lead to serious accidents, such as derailment or separation of train carriages. Therefore, it is essential to ensure the strength and fatigue life of the coupler.
1.2 Research Background and Significance
Previous studies have investigated the fatigue performance of couplers through various methods, including experimental tests and theoretical analyses. However, these methods often have limitations, such as being time-consuming and costly. In this study, we aim to provide a convenient and effective method for evaluating the stress distribution and fatigue life of investment casting couplers through simulation analysis. This method can save time and resources while providing accurate results, which is of great significance for the design and maintenance of couplers.
2. Materials and Methods
2.1 Material Properties of the Coupler
The coupler used in this study is made of E-grade steel ZG25MnCrNiMo through investment casting. The microstructure and mechanical properties of the material were analyzed through optical microscopy (OM) and scanning electron microscopy (SEM), as well as tensile tests.
2.1.1 Microstructure Analysis
The microstructure of the coupler in the as-cast and heat-treated states was observed. In the as-cast state, the microstructure mainly consists of pearlite and ferrite. After heat treatment (normalizing + quenching + tempering), the microstructure becomes fine and uniform tempered sorbite, with many fine and uniform carbide particles distributed on the ferrite matrix.
2.1.2 Mechanical Properties Testing
Tensile tests were carried out on samples taken from the coupler in different states. The results showed that the tensile strength in the as-cast state ranges from 550 to 675 MPa, with an elongation of 1.5% – 2.7%. After heat treatment, the tensile strength reaches 900 – 1450 MPa, the yield strength is 920 MPa, and the elongation can be up to 14.5%. These mechanical properties meet the requirements for the use of the coupler.
2.2 Finite Element Model of the Coupler
2.2.1 Model Establishment
A finite element model of the coupler was established in ANSYS Workbench. Due to the complex structure and uneven wall thickness of the coupler, tetrahedral elements were used for meshing. The global meshing process started from a 10 mm size and gradually reduced until the stress result change was less than 3%. The stress concentration positions were identified, and then the local meshing was further refined with a minimum mesh size of 0.5 mm. The final model had 3,369,299 nodes and 1,924,534 elements.
2.2.2 Boundary Conditions and Loads
The coupler is mainly subjected to longitudinal forces during operation. In the static analysis, different tensile and compressive loads corresponding to the平稳运行 (600 kN),启动 (800 kN), and紧急制动 (1000 kN) conditions were applied. In the fatigue analysis, two types of load spectra were used: the load spectrum measured on the Daqin Line and a simplified sinusoidal load spectrum for the Chongqing Metro Line 3. The Daqin Line load spectrum was modified to adapt to the characteristics of the urban rail vehicle coupler, with amplitudes exceeding 800 kN set to 800 kN.
3. Simulation Results and Discussion
3.1 Static Strength Simulation
3.1.1 Stress Distribution
Under different working conditions, the stress distribution of the coupler was analyzed. In the平稳运行 condition with a 600 kN static tensile load, the maximum stress at the traction end of the coupler was 362.04 MPa, and the maximum deformation was 2.41 mm. In the启动 condition, the maximum stress was 482.72 MPa, and the maximum deformation was 3.21 mm, with the maximum value located at the bottom of the coupler head. In the紧急制动 condition, the maximum stress was 603.4 MPa, and the maximum deformation was 4.01 mm, with the stress maximum at the connection between the connection port and the hook tongue boss.
3.1.2 Comparison with Material Properties
The maximum stresses under different working conditions were compared with the material properties. The tensile limit of the heat-treated coupler material is 1020 MPa on average, and the normal working stress is far less than the yield limit. The elongation after heat treatment is 14.5%, and the calculated maximum deformable amount of the coupler is 62.35 mm. The actual deformations in different working conditions are far from reaching this maximum value, indicating that the coupler can be used safely under normal working conditions.
3.2 Fatigue Analysis
3.2.1 Fatigue Analysis Method
The fatigue life of the coupler was predicted based on the strain-life method. The strain-fatigue life curve of the E-grade steel coupler material was obtained through experiments. The relationship between stress and fatigue life was established according to fatigue theory, and the fatigue life of the coupler was estimated by substituting the stress values obtained from the simulation into the relevant equations.
3.2.2 Fatigue Simulation Results
- Daqin Line Load Spectrum Fatigue Simulation
- The fatigue simulation was carried out using the Daqin Line load spectrum. The results showed that the most fatigue-prone position of the coupler was at the bottom of the coupler head, the connection port, and the connection between the hook body and the coupler head cavity. The lowest fatigue life was 105.2 cycles.
- By comparing with the static stress analysis results, it was found that the fatigue-prone positions were consistent with the stress concentration positions in the static stress simulation.
- The total length of the Daqin Line load spectrum is 15000 km. According to the calculated relationship between the load spectrum length, the number of cycles, and the safe driving mileage, the calculated safe driving mileage of the coupler was 1578000 km.
- Chongqing Metro Line 3 Fatigue Simulation
- First, a simple comparison was made by converting the mileage that the coupler can safely run on the Daqin Line to the Chongqing Metro Line 3. The calculated life of the coupler on the Chongqing Metro Line 3 was 12.8 years. However, this method is inaccurate for estimating the smooth running life on the urban rail.
- Then, a more accurate fatigue simulation was carried out using a sinusoidal load spectrum considering different load conditions (including overload). The fatigue life curve of the coupler was drawn. The results showed that the fatigue life of the coupler decreased with the increase of the load (or the maximum internal stress of the coupler). When the coupler worked at a 1440 kN load, the maximum tensile stress inside the coupler was 868.6 MPa, and the theoretical safe working time was only 0.26 years. When the coupler worked at a 600 kN load, it could withstand 5.1×10 times of sinusoidal load impacts, which fully met the use requirements. When the load was reduced to 580 kN, the maximum stress inside the coupler was 349.86 MPa, and the coupler theoretically would not experience fatigue.
- The calculated lives of the coupler under 800 kN and 600 kN sinusoidal load amplitudes on the Chongqing Metro Line 3 were 31.5 years and 740.7 years, respectively. According to the requirements of the《Metro Vehicle Coupler Technical Specification》, the service life of the coupler should not be less than 30 years. The investment casting coupler after heat treatment far exceeds this requirement, but if the train is frequently overloaded, timely maintenance is required.
4. Conclusions
- The microstructure of the investment casting coupler material is uniform, with fine grains and no obvious casting defects. The tensile strength in the as-cast state can reach up to 675 MPa, and after heat treatment, it can reach up to 1540 MPa, with an evaluated value of 1020 MPa, meeting the requirements of the coupler.
- Under the three working conditions of启动,平稳运行, and紧急制动, the stress and deformation of the coupler are far less than the allowable yield strength and deformation amount, satisfying the service requirements.
- The fatigue life curve of the coupler under sinusoidal load was drawn through simulation. The fatigue life of the coupler loaded with the Daqin Line load spectrum can reach up to 12.8 years, and the fatigue life of the Chongqing Metro Line 3 under 800 kN sinusoidal spectrum is 31.5 years, meeting the use requirements. The simulation results can provide a basis for the maintenance of the coupler.
In conclusion, this study provides a comprehensive analysis of the working stress and fatigue life of investment casting locomotive couplers through material property testing and simulation analysis. The results can be used for the design, evaluation, and maintenance of couplers, ensuring the safety and reliability of railway operations.
Tables
Table 1: ZG25MnCrNiMo Coupler Mechanical Properties Before and After Heat Treatment
Material | Elongation after fracture % | Section shrinkage rate % | Tensile strength MPa | Yield strength MPa | Elastic modulus E/MPa | Hardness/ HBW |
---|---|---|---|---|---|---|
Before heat treatment | 2.1 | 3.9 | 626 | – | 78220 | 235 – 241 |
After heat treatment | 14.5 | 34.5 | 1020 | 920 | – | 315 – 320 |
Table 2: Comparison of Different Load Conditions and Simulation Results
Load Condition | Load Value (kN) | Maximum Stress (MPa) | Maximum Deformation (mm) | Fatigue Life (years) |
---|---|---|---|---|
平稳运行 | 600 | 362.04 | 2.41 | – |
启动 | 800 | 482.72 | 3.21 | – |
紧急制动 | 1000 | 603.4 | 4.01 | – |
Daqin Line (fatigue) | – | – | – | 12.8 (converted) |
Chongqing Metro Line 3 (800 kN) | 800 | 482.7 | – | 31.5 |
Chongqing Metro Line 3 (600 kN) | 600 | – | – | 740.7 |
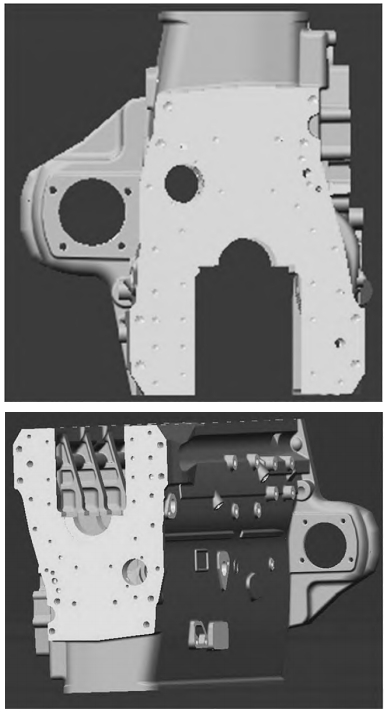