In the cooling and solidification stage, there is eutectic solidification transformation in gray cast iron, and the w stable system develops in the transformation process. The product is austenite plus graphite structure, which is called gray cast iron. Refer to the dotted line in the Fe-C phase diagram.
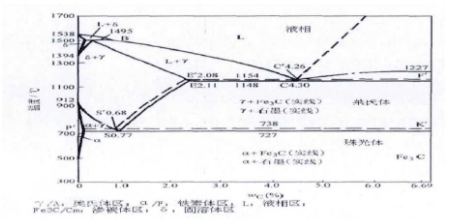
(1) From liquidus to eutectic temperature, primary austenite dendrites are precipitated.
(2) From the beginning of eutectic temperature, austenite w graphite precipitates as the core, which leads to eutectic transformation.
Industrial gray cast iron is mainly hypoeutectic cast iron. In the process of primary phase structure precipitation, when the supercooling degree of the refining liquid meets the requirements and reaches the liquidus, primary austenite nucleation appears, accompanied by temperature cooling, and primary austenite dendrites are precipitated on this basis, while the carbon content in the liquidus increases. When the temperature of molten iron cools to a certain temperature under the eutectic temperature, the carbon content in the liquid phase has exceeded the carbon content of the eutectic cast iron, and the graphite changes back to crystallization and precipitation, so that the carbon content in the liquid phase is reduced and close to the eutectic composition line, and the eutectic austenite is precipitated and mutually promoted with the eutectic graphite, thus forming the eutectic transformation.
In the process of Eutectic Transformation, the first precipitated phase is graphite, and then austenite precipitates between the graphite branches, and then the two grow together to form a symbiotic crystal. Outside the symbiotic crystal, the tip of the graphite sheet always protrudes, extends into the liquid phase, and grows continuously.
Each eutectic crystal can be called a eutectic group. At the end of the eutectic transformation, the intergranular structure of the eutectic group or the primary austenite dendrite and the eutectic group are interlaced. When the gray iron is cooled to normal temperature, the austenite and primary austenite dendrites of each eutectic group form the body of the iron, while the graphite between the eutectic groups forms a network three-dimensional structure, which is distributed in the body. The structure of eutectic group can be seen clearly in the figure, and the purple part is eutectic group.
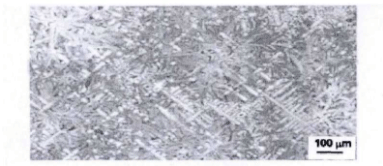
The number of eutectic clusters in gray iron is related to the nucleation and growth conditions during eutectic transformation. The larger the cooling rate and subcooling degree of the molten iron, the more the number of impurity grains and the slower the growth rate, the more the eutectic clusters produced. While the increase of eutectic group number of gray cast iron can improve the mechanical properties of the matrix, it is worth noting that it also increases the probability of shrinkage porosity of the casting.