This article focuses on the utilization of casting CAE sand shooting simulation software to address the sintering casting defects in the water jacket sand core of a cylinder head with a complex inner chamber structure. By analyzing the simulation results, the root cause of the low sand density and lack of compactness in the injector hole area of the water jacket sand core after sand shooting, which leads to sintering in the casting inner chamber, was identified. Through calculations and principle analyses of the nozzle area and exhaust area on the sand core in the sintering area, the specifications and arrangements of the nozzles and exhaust plugs were optimized and adjusted. Subsequently, sand shooting simulation calculations and analyses were conducted, ultimately determining the implementation plan for the rectification of the nozzles and exhaust plugs on the mold. Verification through sand shooting and casting production demonstrated that the rectified sand core was complete, dense, and compact, with no sand sticking in the casting inner chamber, no sintering in the injector hole area, and a significant improvement in the cleanliness of the casting inner chamber.
1. Introduction
With the continuous upgrading of automobile engines and the increasing requirements for comprehensive performance, higher demands are placed on the cleanliness of the inner chambers of engine cylinder blocks and heads. At the same time, customers’ requirements for engine reliability, economy, and comfort are also constantly rising. The improvement of engine product performance has brought new upgrades to the inner chamber structure of the cylinder head, such as the integration of casting the injector sleeve and valve guide, the optimization of the structure of the inner baffle, and the upper and lower double-layer water jacket structure, which enhance the overall water flow field of the cylinder head and improve the cooling effect of the bridge area. However, these structural changes have undoubtedly increased the castability of the cylinder head and put forward higher requirements for casting process technology and production process quality control.
The cylinder head of a certain engine cast by Yuchai has a complex inner chamber structure, with the injector hole directly cast out. The water cavity of the product is separated into upper and lower layers, resulting in a small sand core with a minimum width of 3 – 4 mm. The oil passages in the front and back directions and the valve guide hole structure on the top surface of the casting cause large hot spots in the casting, leading to the sintering of the sand core in the casting inner chamber with a proportion of over 20%. Moreover, the complex water cavity structure increases the difficulty of cleaning the casting inner chamber. The sintering in the casting inner chamber not only affects the cleanliness of the cylinder head inner chamber but also directly reduces the engine reliability if the cleanliness does not meet the standard. Additionally, the inability to clean the inner chamber sintering will directly result in the scrapping of the casting, bringing significant hidden dangers and cost losses to product quality and production manufacturing.
2. Problem Overview
The water jacket sand core of the cylinder head product with a complex inner chamber structure in Yuchai is produced using the cold core resin sand process. Due to the complex inner chamber structure, the proportion of casting sintering defects is as high as over 20%, which has a significant impact on the cleaning difficulty, delivery cycle, and manufacturing cost of the casting. It also affects the cleanliness of the casting inner chamber. The main sintering positions are located around the injector holes of the cylinder head, and the corresponding sand core structure is slender with a minimum width of only 3 mm.
After analysis, the formation of sintering is mainly due to the influence of factors such as the fluidity of the original sand, sand shooting pressure, core box exhaust design, and structural layout during the core shooting process. In the thin-walled area of the sand core, problems such as insufficient and non-compact sand shooting often occur, resulting in sintering under the penetration of high-temperature molten iron. To solve the problem of intracavity sintering quality, common methods include directly replacing with special cold core sand with strong anti-sintering ability, using better high-temperature-resistant coating, or applying a coating with high fire resistance to the easily sintered parts of the sand core before dipping. However, these measures will directly increase the production and manufacturing cost of the cylinder head. Alternatively, the flow direction of the molten iron can be optimized to reduce the flow rate, flow volume, and scouring time of the high-temperature molten iron in the sintering area, thereby reducing the heating degree of the slender sand core position and alleviating the sintering tendency in this area.
To solve the problem of cylinder head inner chamber sintering quality without increasing the production and manufacturing cost, casting CAE software was used to simulate and analyze the shooting process of the water jacket sand core. By identifying the problems of insufficient and non-compact sand shooting in the corresponding sintering area of the sand core, especially the loose, easily deformed, and fractured slender sand core in the injector hole area, which leads to the infiltration of molten iron during casting and the occurrence of sintering, thepositions of the nozzles and exhausts on the mold were optimized and improved based on the CAE sand shooting simulation calculation results. After multiple rounds of simulation and adjustment, the optimal sand shooting design scheme for the arrangement of the nozzles and exhaust plugs on the mold was determined. Then, the mold was modified and verified by sand shooting production. Finally, the compactness and density of the sand core were effectively improved, and the sintering quality problem in the injector hole area of the cylinder head inner chamber was improved and solved. The introduction and use of the sand shooting simulation software have undoubtedly brought great convenience.
3. Application of Sand Shooting Simulation Software
3.1 Sand Shooting Simulation Calculation and Parameter Setting
The water jacket sand core was output as a process model for sand shooting simulation calculation according to the actual specifications and quantities of the nozzles and exhaust plugs on the mold. Then, the STL format file was exported and imported into the geometric model processing interface of the sand shooting simulation software. After adjusting the direction, defining the material groups of each element, and checking for any missing elements, the finite element mesh was divided.
After the mesh division was completed and the quality was checked to be correct, the parameter definition interface was entered. This interface mainly set parameters such as sand shooting pressure, sand shooting time, exhaust area, and sand core material. For solving the problems of non-compactness and lack of density in actual sand shooting production, the closer the simulation parameter settings are to the parameters in the on-site production, the closer the simulation calculation analysis results will be to the actual production situation, and the more effective the optimization scheme output by the simulation calculation analysis will be in solving practical problems.
3.2 Sand Shooting Simulation Calculation and Problem Analysis
After setting the sand shooting parameters according to the actual production situation on-site, the sand shooting simulation calculation was carried out. Through the criterion analysis, it was found that the sand density in the area corresponding to the cylinder head injector hole of the water jacket sand core was relatively low. The sand density in the corresponding area of the inner chamber sintering after core shooting was 1.39 g/cm³, which did not meet the requirement of the sand density of 1.48 g/cm³ after sand shooting, indicating the existence of insufficient or non-compact sand shooting. This was the main cause of the sintering problem in the casting inner chamber.
Based on the analysis of the sand density in each area after sand shooting simulation calculation, it was found that the nozzle arrangement in the cylinder head injector hole area was不合理, resulting in unbalanced sand shooting volume in this area and turbulent flow during the sand shooting process, which was not conducive to the filling of the core sand. Moreover, due to the inappropriate selection of nozzle specifications, there were cases of either too small or too large sand volume, resulting in a low sand core density in the injector hole area after sand shooting.
By calculating the arrangement and specifications of the nozzles and exhaust plugs actually used in the water jacket sand core mold, the proportional relationship between the nozzle area and the corresponding sand core weight in each area of the sand core, as well as the proportional relationship between the exhaust area and the intake area in each area of the sand core, were obtained. The calculation results showed that the ratio of the nozzle area to the weight in the water jacket area of the sand core was relatively large compared to other areas, that is, more nozzles were arranged. However, due to the small number or small specifications of the exhaust plugs arranged, there was a situation of insufficient exhaust in the water jacket area of the sand core during the sand shooting process, even though the sand volume was sufficient, resulting in the problem of non-compact and loose sand shooting in the water jacket area, especially in the slender injector hole position.
3.3 Process Scheme Optimization and Sand Shooting Simulation Calculation
3.3.1 Optimization of Nozzle Arrangement and Specifications
The nozzle is the channel through which the compressed air sprays the loose core sand into the cavity of the core box. It is necessary to ensure that a sufficient amount of core sand enters the core box quickly and that the sand core is filled and cured well. In the narrow, deep concave areas of the core box and the corners where the core sand is difficult to fill, such as the injector hole area of the water jacket sand core, the fluidity of the core sand is generally poor, and the filling effect is not ideal. After setting the sand shooting nozzle in this area, the sand flow can directly fill the corners, making the sand core complete and compact.
Under a certain sand shooting pressure, the selection of nozzle specifications and sand shooting time have a key impact and direct effect on the quality of the sand core. If the nozzle area is too large and the filling time is too short, the kinetic energy of the compressed air cannot be fully utilized during the sand shooting process, resulting in problems such as loose and poor density of the sand core after sand shooting.
According to the structure and shape of the sand core, combined with the arrangement and specifications of the nozzles in this area, the water jacket sand core in the injector hole area was divided into weights according to the structure shape. Then, based on the complexity of the sand core structure, the empirical relationship and statistical analysis between the nozzle specifications and the effective sand shooting weight were carried out. Finally, the nozzle specifications at different positions were optimized and adjusted to improve the compactness and density of the sand core after sand shooting.
3.3.2 Optimization of Exhaust Plug Arrangement and Specifications
The exhaust plug plays a major role in exhausting during the core shooting process. The exhaust plugs arranged in the core box form an exhaust system, and their arrangement is crucial to the quality of the sand core. When the core sand enters the core box during sand shooting, the exhaust system of the core box can quickly exhaust the original air in the core box and the gas brought in during sand shooting to avoid gas accumulation, which may cause the sand core to be incompletely filled and result in a loose and non-dense sand core. Secondly, for the cold core box, the exhaust system can ensure that the triethylamine catalyst can be blown to every corner of the cavity, thus ensuring the complete curing of the core sand.
Based on the function, specifications, and arrangement principles of the exhaust plugs, combined with the optimized intake area after adjusting the nozzle specifications, the required reasonable exhaust area was calculated, and the specifications of the exhaust plugs in the sand core injector hole area were optimized and adjusted.
3.3.3 Effect of Optimized Sand Shooting Simulation Calculation
Based on the above settings of the nozzles and exhaust plugs in the water jacket sand core injector hole area, and through the analysis of the impact of sand shooting simulation calculation on the quality of the sand core, combined with the optimization and adjustment of the arrangement of the nozzles and exhaust plugs, the sand shooting simulation software was used to conduct a simulation calculation on the sand core. According to the calculation results, the sand density in the area corresponding to the injector hole sintering was increased from 1.39 g/cm³ to 1.44 g/cm³, and the compactness and density of the sand core were improved.
After the optimization and adjustment of the nozzles and exhaust plugs, the analysis of the sand shooting simulation calculation results showed that the sand shooting volume of each nozzle was balanced. With the improvement of the exhaust effect, the sand density was increased, and the compactness and density of the sand core were improved. This indicates that the optimization and adjustment of the nozzles and exhaust plugs achieved the desired effect of core shooting and exhaust.
4. Production Verification Effect after Optimization and Improvement
According to the above optimization and adjustment of the specifications and settings of the nozzles and exhaust plugs in the water jacket sand core injector hole area, and through the sand shooting simulation calculation and result analysis, it was concluded that the optimization and adjustment achieved the improvement purpose. The corresponding nozzles and exhaust plugs on the mold were rectified according to this adjustment scheme, and after completion, the sand shooting effect verification was carried out. The sand core in the area corresponding to the injector hole sintering was formed completely, with a smooth surface and was dense and compact. The casting inner chamber had no sand sticking, no sintering in the injector hole area, and was easy to clean, with a significant improvement effect.
5. Conclusion
5.1 Summary of the Solution Process
This article described the use of casting CAE sand shooting simulation software to conduct sand shooting simulation calculations on the water jacket sand core of a cylinder head with a complex inner chamber structure. It was analyzed that the low sand density and lack of compactness in the injector hole area of the water jacket sand core after sand shooting were the main causes of the sintering in the casting inner chamber. By optimizing and adjusting the specifications and arrangements of the nozzles and exhaust plugs on the mold and conducting sand shooting simulation calculations, the implementation plan for the rectification of the nozzles and exhaust plugs on the mold was determined. After the mold was changed, the core shooting effectively improved the sand density in the injector hole area of the sand core, solving the quality problems of sand sticking and sintering in the injector hole area of the casting inner chamber.
5.2 Significance and Value of the Method
Through the use of sand shooting simulation calculation software to solve the problem of casting inner chamber sintering, the calculation and analysis of the mold sand shooting area and exhaust area were carried out, and an empirical method for solving the cleanliness of the casting inner chamber and a process design specification for the setting of nozzles and exhaust plugs were summarized. This effectively guided and solved the quality problems of sand sticking and sintering in the casting inner chamber caused by loose sand cores and insufficient compactness in the actual production process.
In conclusion, the application of casting CAE sand shooting simulation software provides an effective solution for solving the sintering casting defects of cylinder heads with complex inner chamber structures, improving the quality and reliability of castings, and reducing production costs.
6. Discussion
The successful application of casting CAE sand shooting simulation in solving the sintering defects of the cylinder head with complex inner chamber structure demonstrates the effectiveness and importance of this technology in the casting industry. It not only helps to identify the root causes of defects but also provides a scientific basis for process optimization and improvement.
However, it should be noted that the simulation results are still affected by certain factors, such as the accuracy of the model input parameters and the limitations of the simulation software itself. Therefore, in practical applications, it is necessary to continuously validate and refine the simulation model to ensure its accuracy and reliability.
In addition, with the continuous development of casting technology, new challenges and problems may arise. For example, the requirements for the performance and quality of cylinder heads are constantly increasing, and the complexity of the inner chamber structure is also increasing. In response to these challenges, further research and development of more advanced casting CAE simulation technologies are needed to better meet the needs of the industry.
7. Future Outlook
Looking ahead, the application of casting CAE sand shooting simulation in the casting industry is expected to continue to expand and 深化. With the continuous improvement of computer performance and the development of simulation algorithms, the accuracy and efficiency of simulation will be further improved.
In the future, casting CAE simulation is likely to be integrated with other advanced manufacturing technologies, such as 3D printing and intelligent manufacturing. This will not only improve the quality and performance of castings but also reduce production costs and environmental impacts.
Moreover, with the increasing emphasis on sustainable development, the development of environmentally friendly casting processes and materials will become a major trend. Casting CAE simulation can play an important role in this process by optimizing process parameters and reducing waste and emissions.
In conclusion, the future of casting CAE sand shooting simulation is promising, and it will continue to contribute to the development and innovation of the casting industry.
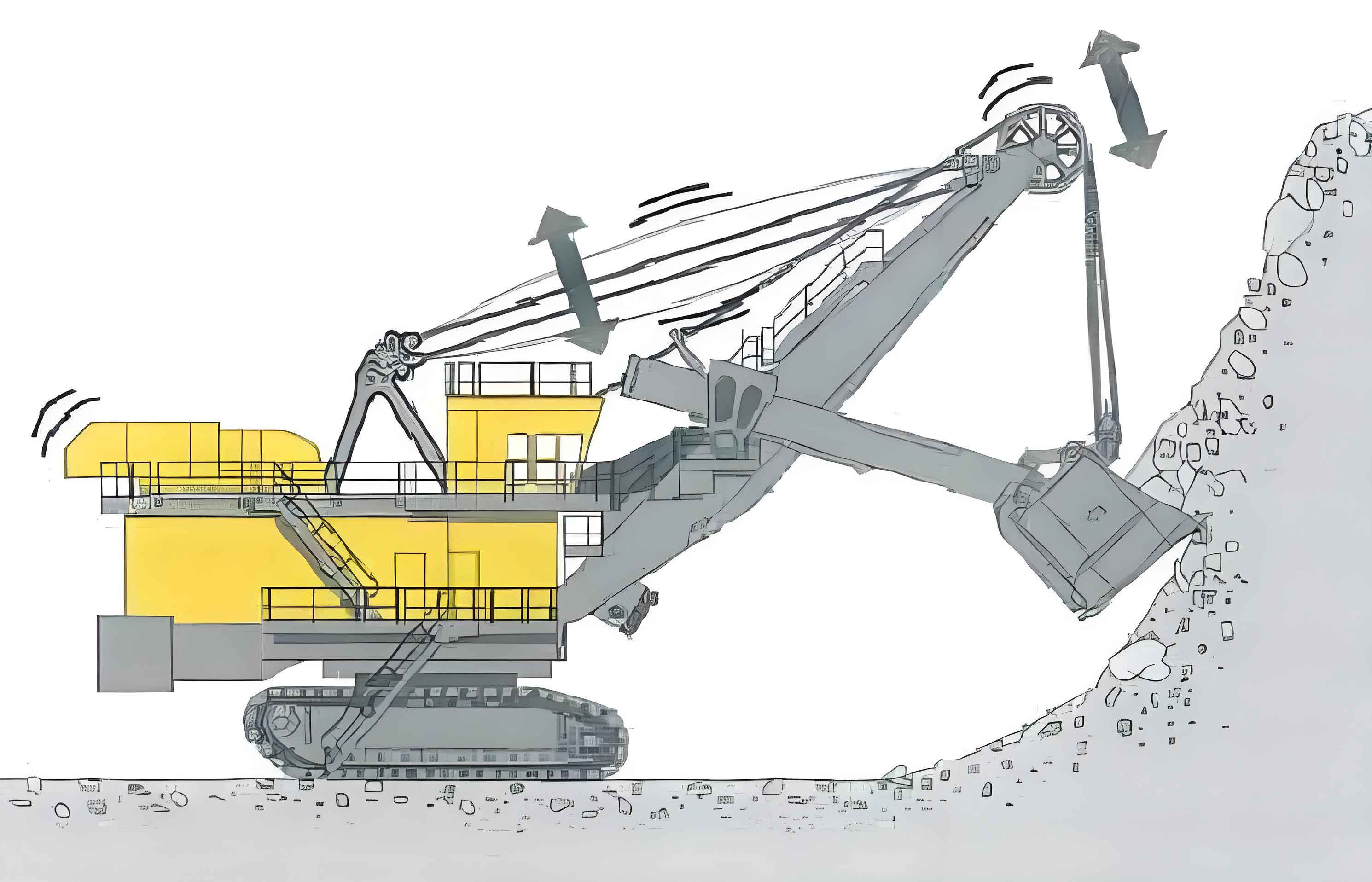