Aluminum alloy castings are extensively utilized in aerospace, automotive, and rail industries due to their superior strength-to-weight ratio and corrosion resistance. Thin-wall structures, typically under 6mm thick, present significant manufacturing challenges including premature solidification, incomplete filling, and gas porosity. Squeeze casting—applying high pressure during solidification—effectively mitigates these issues by enhancing metal fluidity and reducing shrinkage defects. This article details a comprehensive approach to producing a magnetic levitation train component (1000×254×208 mm) using ZL101A-T6 alloy, integrating sand mold low-pressure casting with squeeze casting principles to achieve near-defect-free outcomes.
1. Performance Requirements and Process Challenges
Critical specifications for the thin-wall component include:
Parameter | Requirement |
---|---|
Wall Thickness | 6 mm (uniform) |
Tensile Strength | ≥275 MPa |
Yield Strength | ≥190 MPa |
Surface Roughness | Ra ≤25 μm |
Internal Defects (ASTM E155) | Class ≤1 |
Thermal gradients in thin sections impede directional solidification, heightening risks of misruns and porosity. Squeeze casting counteracts this by imposing controlled pressure ($P_{sq}$) to prolong feeding time, governed by:
$$ P_{sq} = \frac{F}{A} $$
where $F$ is the applied force and $A$ is the cross-sectional area.
2. Integrated Squeeze Casting Process Design
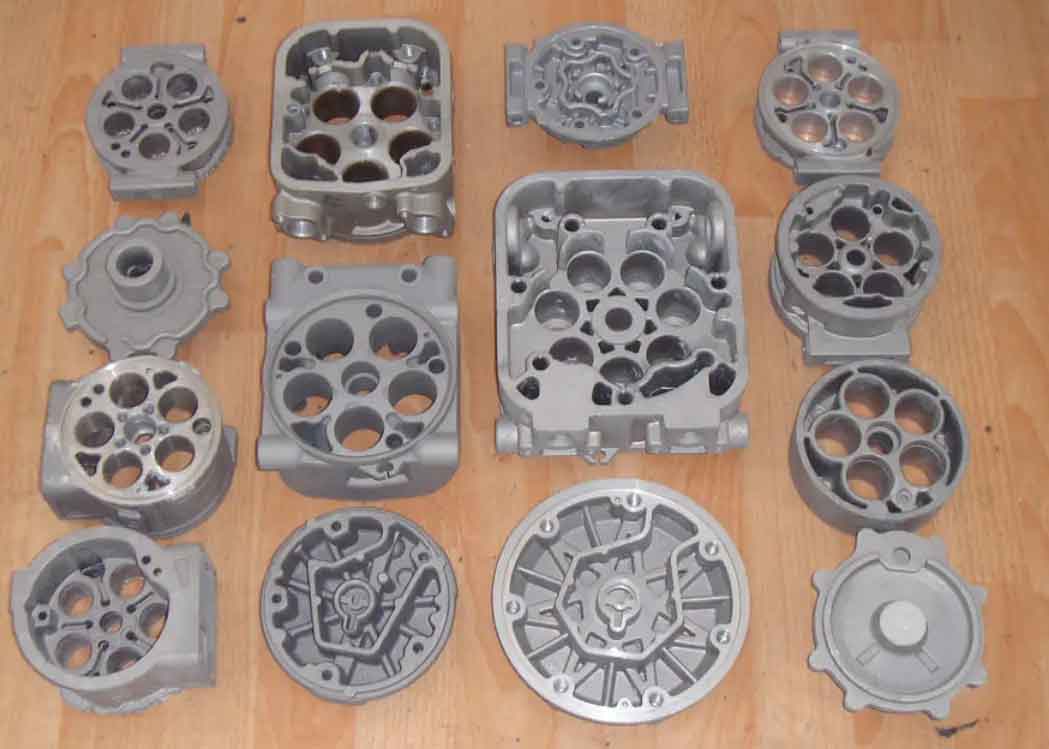
We combined low-pressure filling with squeeze casting to optimize feeding. Molten ZL101A (725–735°C) was injected via vertical slot gates at 0.5 bar, while squeeze pressure (80–100 MPa) was applied during solidification. Chills accelerated cooling in thick sections, synchronizing solidification fronts. The pressure-enhanced Niyama criterion predicts shrinkage avoidance:
$$ G / \sqrt{\dot{T}} \geq K \cdot P_{sq}^{0.5} $$
where $G$ is thermal gradient, $\dot{T}$ is cooling rate, and $K$ is a material constant.
3. Numerical Simulation and Defect Mitigation
CFD simulations mapped filling sequences and thermal profiles (Figure 3). Velocity fields ($\vec{v}$) confirmed laminar flow through slots, minimizing turbulence:
$$ \nabla \cdot (\rho \vec{v}) = 0 $$
Solidification modeling revealed that squeeze casting extended feeding time by 40%, eliminating macro-porosity. Initial trials showed mistuns and slag inclusions due to low metal quality. Corrective measures included:
Defect | Root Cause | Squeeze Casting Solution |
---|---|---|
Mistruns | Low Pouring Temperature | Increase temperature to 735°C + apply $P_{sq}$ |
Slag Inclusions | Impure Charge | Limit scrap to 30%; use rotary degassing |
Microporosity | Insufficient Feeding | Maintain $P_{sq}$ ≥80 MPa until solidus |
Post-optimization, X-ray inspection showed defect rates below 0.5% (Figure 5).
4. Metallurgical and Mechanical Outcomes
Squeeze casting refined grain structures by suppressing dendritic growth under pressure. Hardness homogeneity improved by 22%, satisfying HB≥80 requirements. Yield strength ($\sigma_y$) enhancements followed the relationship:
$$ \sigma_y = \sigma_0 + K_{sq} \cdot d^{-1/2} $$
where $d$ is grain size and $K_{sq}$ is the squeeze casting coefficient. Batch production achieved 98% yield with near-net-shape dimensional accuracy.
5. Conclusions
Squeeze casting is indispensable for thin-wall aluminum components requiring high integrity. Integrating low-pressure filling with high-pressure solidification enables:
- Complete cavity filling despite rapid heat loss
- Suppression of gas/shrinkage porosity through pressure-assisted feeding
- Enhanced mechanical properties via microstructural refinement
This synergy proves critical for applications like magnetic levitation systems where weight savings and reliability are paramount. Future work will optimize $P_{sq}$ gradients for complex geometries.