Chapter 1: Steel Casting is Metal Processing Process
That’s correct! Steel casting is a metal processing technique used to create complex and intricate parts by pouring molten steel into a pre-designed mold, known as a “casting mold” or “casting die.” The mold is typically made from materials like sand, ceramic, or metal. Once the molten steel cools and solidifies within the mold, it takes on the shape of the mold and forms the desired part.
The steel casting process offers several advantages, including the ability to produce intricate and detailed parts that may be difficult or expensive to manufacture through other methods. Steel castings are widely used in various industries, including automotive, aerospace, construction, energy, and more.
The process of steel casting generally involves the following steps:
- Pattern Creation: A pattern, typically made from wood, plastic, or metal, is created to replicate the shape of the desired final part.
- Mold Making: The pattern is used to create a mold cavity in molding material, such as sand or ceramic. The mold consists of two halves, the “cope” and “drag,” which are fitted together to form the mold cavity.
- Molten Steel Preparation: Steel is melted in a furnace to reach the desired temperature. Various types of steel alloys can be used, depending on the properties required for the final part.
- Pouring: The molten steel is poured into the mold cavity through a gating system, which includes channels and sprues that direct the flow of the molten metal.
- Solidification: The molten steel cools and solidifies within the mold cavity, taking on the shape of the pattern.
- Cooling and Removal: After solidification, the casting is allowed to cool and harden further. Once cooled, the mold is removed, and the casting is extracted.
- Finishing: The casting may undergo various finishing processes, such as machining, grinding, heat treatment, and surface coating, to achieve the desired final specifications and surface quality.
Steel casting offers the flexibility to create parts of various sizes and complexities, ranging from small components to large industrial machinery. The process can produce high-quality and structurally sound parts with good mechanical properties. However, like any manufacturing process, steel casting also comes with its own set of challenges and considerations, including design constraints, material selection, mold preparation, and post-casting treatments.
Overall, steel casting is a versatile and widely used method for producing a wide range of steel parts used in diverse industries.
Chapter 2: The Process Flow of Steel Casting
The steel casting process involves several essential steps, from model preparation to post-treatment, to create high-quality steel parts. Here’s a detailed breakdown of the process flow:
1. Pattern or Model Preparation:
- A pattern or model of the desired part is created using materials like wood, plastic, or metal.
- The pattern is an exact replica of the final part and is used to create the mold cavity.
2. Mold Making:
- A mold is created around the pattern using molding material, typically a mixture of sand and binders.
- The mold consists of two halves: the upper half (cope) and the lower half (drag).
- Cores, which are inserts made of sand or other materials, may also be placed within the mold to create internal features.
3. Molten Steel Melting:
- Raw steel materials are melted in a furnace, often an electric arc furnace or an induction furnace.
- Alloying elements can be added to achieve the desired properties of the final steel casting.
4. Pouring:
- Once the molten steel reaches the required temperature and composition, it is poured from the furnace into a ladle.
- The ladle is then transported to the mold for pouring.
5. Pouring and Solidification:
- The molten steel is poured into the mold cavity through a gating system, which includes channels and sprues.
- The molten steel starts to cool and solidify as it comes into contact with the mold walls.
6. Cooling:
- The casting is left undisturbed to cool and solidify completely.
- The cooling rate can affect the microstructure and properties of the final casting.
7. Shakeout and Demolding:
- Once the casting has cooled, the mold is removed, typically by breaking or shaking the mold.
- The sand is separated from the casting, and any cores are removed.
8. Cleaning and Finishing:
- The casting is cleaned to remove residual sand, scale, and any other contaminants.
- Any excess material or imperfections are removed through processes like grinding, cutting, or machining.
9. Inspection:
- The casting undergoes thorough inspection to ensure it meets quality standards.
- Various testing methods, such as visual inspection, dimensional measurement, and non-destructive testing, may be employed.
10. Heat Treatment:
- Heat treatment may be applied to improve the casting’s mechanical properties and remove internal stresses.
- Processes such as annealing, normalizing, quenching, and tempering may be used.
11. Surface Treatment:
- The casting may undergo additional treatments, such as shot blasting or surface coating, to enhance its appearance and corrosion resistance.
12. Final Inspection and Packaging:
- The finished casting undergoes a final inspection to ensure it meets all specifications and requirements.
- If approved, the casting is prepared for packaging and shipment to the customer.
Throughout the process, strict quality control measures are implemented to ensure the integrity, accuracy, and performance of the final steel casting. The steps outlined above demonstrate how each phase contributes to producing high-quality steel parts suitable for various industrial applications.
Chapter 3: Types of Steel Suitable for Steel Casting
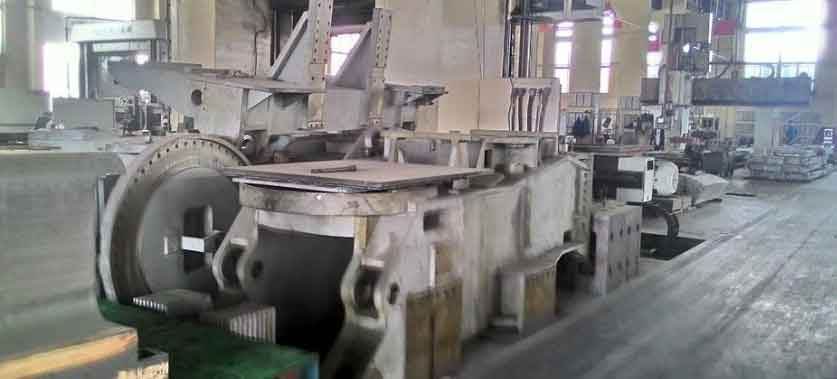
When selecting steel for casting, several factors need to be considered to ensure that the material meets the requirements of the specific application. The choice of steel type depends on factors such as the intended use of the casting, mechanical properties needed, heat treatment capabilities, and environmental conditions. Here are some types of steel suitable for casting and key considerations for material selection:
1. Carbon Steel:
- Carbon steel is a versatile and commonly used material for casting due to its ease of casting and good machinability.
- Considerations: Chemical composition, carbon content, and desired mechanical properties (strength, hardness) based on heat treatment.
2. Low-Alloy Steel:
- Low-alloy steels contain small amounts of alloying elements (such as manganese, nickel, chromium) to enhance specific properties.
- Considerations: Alloying elements and their effects on mechanical properties (tensile strength, impact resistance, wear resistance).
3. Stainless Steel:
- Stainless steel is known for its corrosion resistance and is suitable for applications where exposure to moisture or corrosive environments is a concern.
- Considerations: Corrosion resistance, chemical composition, and heat treatment requirements.
4. Tool Steel:
- Tool steels are used for applications requiring high hardness, wear resistance, and heat resistance.
- Considerations: Tool steel type (cold work, hot work, high-speed), heat treatment capabilities, and desired hardness.
5. Duplex Stainless Steel:
- Duplex stainless steels offer a combination of good corrosion resistance and higher strength compared to standard stainless steels.
- Considerations: Corrosion resistance, mechanical properties, weldability, and heat treatment.
6. Heat-Resistant Steel:
- Heat-resistant steels are suitable for applications involving high-temperature environments, such as furnace components.
- Considerations: Heat resistance, thermal stability, and mechanical properties at elevated temperatures.
7. Wear-Resistant Steel:
- Wear-resistant steels are designed to resist abrasion and wear in harsh conditions.
- Considerations: Wear resistance, hardness, toughness, and impact resistance.
8. Alloy Cast Iron:
- Alloy cast iron contains added alloying elements (such as chromium, molybdenum) for improved properties.
- Considerations: Alloying elements and their effects on mechanical properties, wear resistance, and corrosion resistance.
Key Considerations for Material Selection:
- Mechanical Properties: Determine the required tensile strength, hardness, impact resistance, and other mechanical properties based on the application’s demands.
- Corrosion Resistance: Evaluate the level of exposure to corrosive environments and select a material with suitable corrosion resistance.
- Heat Treatment Compatibility: Consider the feasibility of heat treatment processes such as annealing, quenching, and tempering for achieving desired properties.
- Weldability: Assess the ease of welding and the potential impact on the material’s mechanical properties.
- Cost and Availability: Consider the cost and availability of the chosen steel type, including the potential for sourcing specific alloying elements.
- Environmental Conditions: Account for factors like temperature, humidity, and exposure to chemicals or abrasive media.
- Part Complexity: The casting method and part geometry may influence material selection to ensure successful casting and desired properties.
- Regulatory and Industry Standards: Ensure that the selected material complies with relevant standards and regulations for the intended application.
By carefully evaluating these considerations, manufacturers can select the most appropriate steel type for casting to achieve the desired performance, durability, and reliability of the final product.
Chapter 4: The Process of Melting Molten Steel in Steel Casting
The process of melting molten steel in steel casting is a crucial step in ensuring the quality and properties of the final castings. It involves selecting the appropriate furnace type, controlling the melting process, and applying degassing treatment to remove impurities. Here’s an overview of these steps:
1. Furnace Type Selection:
- Different types of furnaces are used for melting molten steel, including electric arc furnaces (EAF), induction furnaces, and cupola furnaces.
- Electric Arc Furnace (EAF): Uses electric arcs generated between electrodes and the steel charge to melt scrap steel or raw materials. Offers precise temperature control and can accommodate various steel types.
- Induction Furnace: Employs electromagnetic induction to generate heat directly within the metal. Offers high efficiency and rapid heating.
- Cupola Furnace: Traditionally used for iron and low-alloy steel melting. It relies on the combustion of coke to generate heat.
2. Melting Process Control:
- The melting process involves charging scrap steel, pig iron, or other raw materials into the furnace.
- Furnace operators monitor and control parameters such as temperature, alloy composition, and gas injection to achieve the desired melt quality.
3. Alloying and Adjusting Composition:
- Alloying elements are added to achieve the desired steel composition and properties. This may include elements like manganese, chromium, nickel, and others.
- Adjustments are made based on chemical analyses and desired material specifications.
4. Degassing Treatment:
- Degassing is a critical step to remove unwanted gases, such as hydrogen and oxygen, from the molten steel. These gases can cause porosity and other defects in the final castings.
- Various degassing methods are used, including:
- Vacuum Degassing: Utilizes a vacuum chamber to extract gases from the molten steel.
- Inert Gas Injection: Inert gases (such as argon) are injected into the melt to displace dissolved gases.
- Ladle Treatment: A degassing agent is added to the ladle before pouring molten steel into molds.
5. Slag Formation and Control:
- Slag is formed as a result of chemical reactions between the molten steel and refractory lining materials.
- Proper slag control is essential to maintain clean molten steel and prevent slag-related defects.
6. Temperature Control and Tapping:
- The furnace’s temperature is closely monitored and controlled to ensure that the molten steel reaches the desired temperature for casting.
- Once the molten steel is ready, it is tapped (poured) from the furnace into ladles for transportation to the casting area.
Proper control and management of the melting process are essential to achieve consistent quality and properties in the molten steel. The choice of furnace type, degassing methods, and temperature control techniques can impact the cleanliness, composition, and overall quality of the molten steel. Manufacturers must follow precise procedures and best practices to ensure that the molten steel meets the requirements for successful steel casting and produces high-quality castings.
Chapter 5: The Pouring Process of Molten Steel Casting
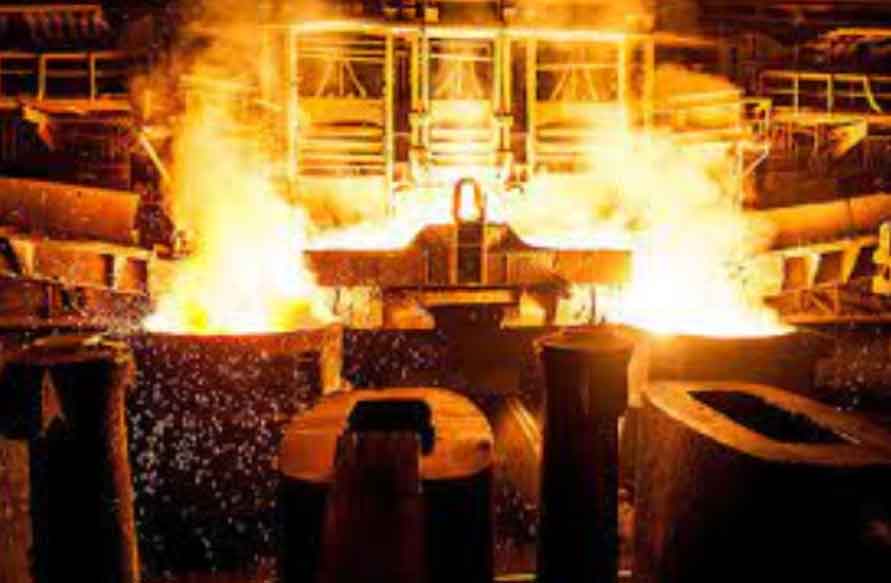
The pouring process of molten steel casting is a critical step that involves transferring the molten metal from the furnace to the mold cavity. Proper control of pouring temperature, speed, and technique is essential to ensure the quality and integrity of the final castings. Here’s an overview of the pouring process and how to control temperature and speed:
1. Pouring Ladle Preparation:
- The pouring ladle is prepared to receive the molten steel from the furnace. The ladle may be preheated to prevent rapid cooling of the molten metal upon contact.
2. Pouring Temperature Control:
- The pouring temperature of the molten steel is a crucial parameter that affects the solidification process and the properties of the casting.
- Pouring temperature is typically determined based on factors such as the alloy being cast, the size and complexity of the mold, and the desired solidification rate.
- Temperature control is essential to prevent issues like overheating, which can lead to defects or excessive wear on the mold.
3. Pouring Technique:
- The molten steel is poured into the mold cavity in a controlled manner. Proper pouring technique helps ensure even filling of the mold and minimizes the risk of defects like cold shuts or misruns.
- Pouring can be done using various methods, including bottom pouring, top pouring, and vacuum-assisted pouring.
4. Pouring Speed Control:
- The speed at which the molten steel is poured into the mold is important for achieving uniform filling and preventing turbulence that could introduce defects.
- Too high a pouring speed can lead to mold erosion and turbulence, while too low a speed can cause premature solidification and incomplete filling.
5. Cooling and Solidification:
- As the molten steel enters the mold, it begins to cool and solidify from the mold walls inward. The solidification process influences the microstructure and properties of the final casting.
- Proper cooling is necessary to avoid defects like shrinkage and porosity, which can occur if the metal solidifies too rapidly.
6. Chills and Risers:
- Chills (metal inserts or plates) may be strategically placed in the mold to enhance cooling or promote directional solidification.
- Risers (also known as feeders) are extra sections of the mold designed to contain additional molten metal. They supply molten metal to compensate for shrinkage during solidification.
7. Monitoring and Quality Control:
- Pouring conditions may be monitored using temperature sensors, flow sensors, and other instruments to ensure consistent results.
- Quality control personnel may visually inspect the pouring process and analyze samples of the molten metal to verify its composition and temperature.
8. Post-Pouring Treatment:
- After pouring, the mold is allowed to cool and solidify. Depending on the casting design and requirements, post-pouring treatments such as shakeout, cleaning, and heat treatment may be performed.
By carefully controlling the pouring temperature, speed, and technique, manufacturers can achieve proper filling of the mold, uniform solidification, and minimize the risk of defects. The pouring process is a critical factor in ensuring the quality and integrity of the final castings, and it requires skilled operators and precise control to achieve consistent results.
Chapter 6: The Process of Steel Castings after Demolding
After the steel casting has been demolded and allowed to cool, various subsequent processes may be required to achieve the desired final properties, dimensions, and surface finish. These processes are essential to refine and enhance the quality of the steel castings. Here are some of the key subsequent processes commonly used for steel castings:
1. Deburring and Cleaning:
- During the casting process, small protrusions called burrs or flash may form on the edges or surfaces of the castings.
- Deburring involves removing these excess material remnants to achieve a clean and smooth surface finish.
- Cleaning processes such as shot blasting or chemical cleaning may also be used to remove any residual mold material, sand, or other contaminants.
2. Trimming and Machining:
- Trimming involves removing any excess material or irregularities from the casting using machining processes such as milling, turning, drilling, or grinding.
- Machining may also be used to achieve precise dimensions and tolerances for critical features of the casting.
3. Heat Treatment:
- Heat treatment is often performed to optimize the mechanical properties of steel castings.
- Processes such as annealing, normalizing, quenching, and tempering are used to achieve specific hardness, toughness, and strength characteristics.
- Heat treatment also helps relieve internal stresses and improve dimensional stability.
4. Surface Treatment:
- Surface treatments are applied to improve the aesthetics, corrosion resistance, and wear resistance of steel castings.
- Common surface treatments include plating, coating, painting, passivation, and galvanization.
5. Non-Destructive Testing (NDT):
- NDT methods such as ultrasonic testing, radiographic testing, and magnetic particle testing may be used to detect internal defects or irregularities without damaging the casting.
6. Inspection and Quality Control:
- Each casting is thoroughly inspected to ensure it meets specified quality standards and dimensional requirements.
- Inspections may include visual checks, dimensional measurements, material testing, and other assessments.
7. Assembly and Joining:
- In some cases, steel castings may need to be assembled or joined with other components to create a larger assembly or finished product.
- Welding, brazing, or other joining techniques may be used to integrate the castings into the overall structure.
8. Final Surface Finish:
- The final surface finish of the casting may involve additional processes such as polishing, buffing, or honing to achieve the desired texture and appearance.
The specific subsequent processes required for a particular steel casting will depend on factors such as the casting’s intended use, design complexity, material properties, and quality requirements. Manufacturers carefully plan and execute these processes to ensure that the steel castings meet all specifications and are ready for their intended applications.
Chapter 7: The Quality Control Methods for Steel Castings
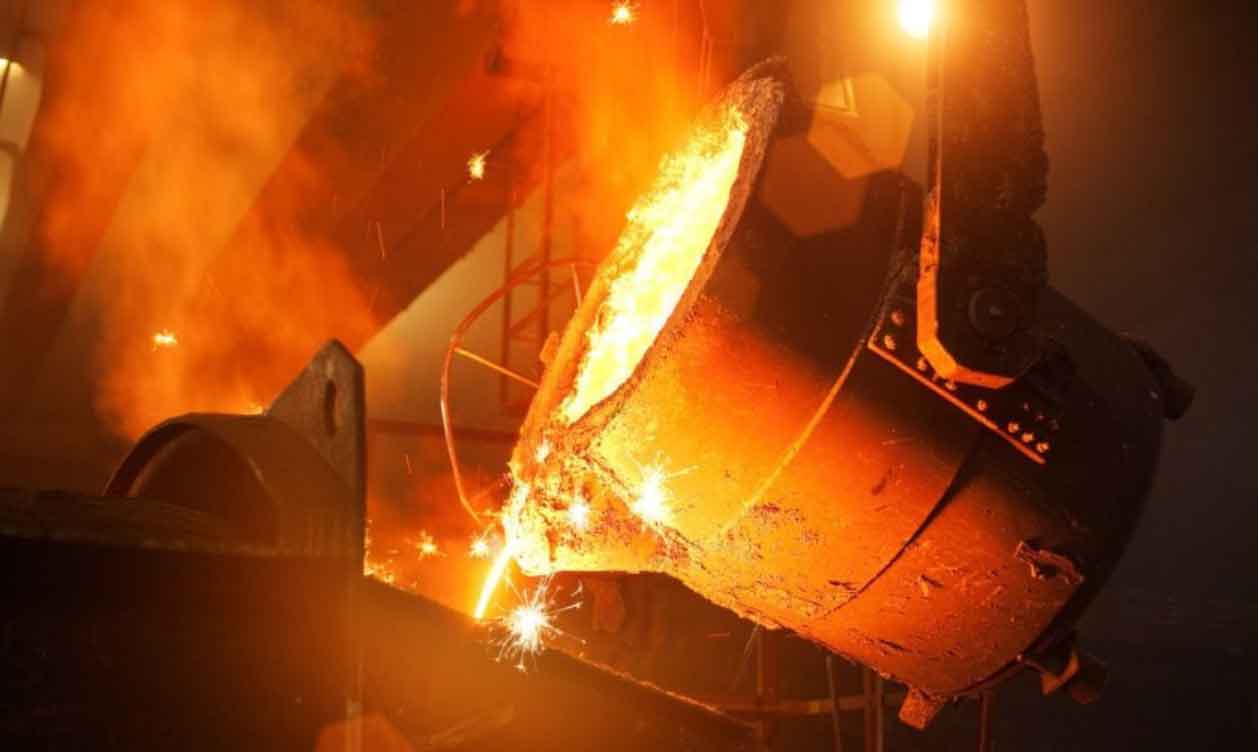
Quality control is a critical aspect of steel casting production to ensure that the final products meet specified standards, performance requirements, and safety criteria. Various quality control methods are employed at different stages of the casting process to monitor and verify the quality of steel castings. Here are some common quality control methods used for steel castings:
1. Dimensional Measurement:
- Precise dimensional measurements are essential to ensure that steel castings meet specified tolerances and fitment requirements.
- Coordinate measuring machines (CMMs), calipers, micrometers, and optical measurement devices are used to accurately measure dimensions and geometries.
2. Visual Inspection:
- Visual inspection is performed to identify surface defects, such as cracks, porosity, surface roughness, and irregularities.
- Skilled inspectors visually assess the castings to detect any issues that may affect the casting’s functionality or appearance.
3. Metallographic Analysis:
- Metallographic analysis involves preparing thin sections of the casting and examining them under a microscope.
- This technique helps assess the microstructure, grain size, phase distribution, and any potential defects within the casting.
4. Non-Destructive Testing (NDT):
- NDT methods are used to detect defects or irregularities without damaging the casting. Common NDT methods include:
- Ultrasonic Testing (UT): Uses high-frequency sound waves to detect internal defects.
- Radiographic Testing (RT): Involves X-rays or gamma rays to image internal structures.
- Magnetic Particle Testing (MT): Detects surface and near-surface defects using magnetic fields.
- Dye Penetrant Testing (PT): Reveals surface defects by applying a colored liquid that penetrates defects.
- Eddy Current Testing (ET): Detects surface and near-surface defects using electromagnetic induction.
5. Mechanical Testing:
- Mechanical tests, such as tensile testing, hardness testing, and impact testing, assess the material’s mechanical properties, strength, and durability.
6. Chemical Analysis:
- Chemical analysis verifies the composition of the steel casting to ensure it meets the required alloy and element content specifications.
7. Ultrasonic Velocity Measurement:
- Ultrasonic velocity measurement helps assess the uniformity of material properties within the casting by measuring the speed of ultrasonic waves.
8. Pressure Testing:
- Pressure testing involves subjecting the casting to pressure to ensure its integrity and leak-tightness.
9. Load Testing:
- Load testing assesses the structural integrity and load-bearing capacity of the casting under specific conditions.
10. Documentation and Traceability:
- Comprehensive documentation and traceability systems are maintained to track the production process, materials used, testing results, and any corrective actions taken.
By employing a combination of these quality control methods, manufacturers can identify and address defects, deviations, and irregularities, ensuring that the steel castings meet the highest standards of quality and reliability.
Chapter 8: The Widespread Application of Steel Castings
Steel castings are widely used across various industries due to their versatility, strength, and durability. Here are some of the fields where steel castings find extensive applications:
1. Energy Industry:
- Steel castings are used in components of power generation equipment, such as turbines, generators, and boilers, due to their ability to withstand high temperatures and mechanical stresses.
2. Construction and Infrastructure:
- Steel castings are utilized in construction machinery, cranes, bridges, and other structural elements for their load-bearing capacity and resistance to wear and tear.
3. Automotive Industry:
- Steel castings are employed in engine blocks, transmission components, suspension parts, and other critical automotive components due to their high strength and durability.
4. Aerospace Industry:
- Steel castings are used in aircraft engines, landing gear components, and other aerospace applications where high strength and reliability are crucial.
5. Mining and Earthmoving Equipment:
- Steel castings are utilized in mining machinery, excavators, bulldozers, and other heavy equipment that requires rugged components capable of withstanding harsh conditions.
6. Oil and Gas Industry:
- Steel castings are used in oil rigs, drilling equipment, and processing facilities due to their corrosion resistance and ability to withstand extreme environments.
7. Marine Industry:
- Steel castings are employed in shipbuilding, marine engines, propellers, and other marine components for their resistance to corrosion and high mechanical loads.
8. Rail and Transportation:
- Steel castings are used in rail infrastructure, locomotives, and rolling stock for their durability and load-bearing capacity.
9. Mechanical Manufacturing:
- Steel castings are commonly found in industrial machinery, pumps, valves, gearboxes, and other mechanical components due to their strength and reliability.
10. Agricultural Machinery:
- Steel castings are utilized in agricultural equipment such as tractors, plows, and harvesters for their ability to handle heavy loads and challenging conditions.
11. Medical Equipment:
- Steel castings are used in the construction of medical devices and equipment where precision and durability are essential.
12. Food Processing Equipment:
- Steel castings find applications in food processing machinery and equipment due to their resistance to corrosion and hygienic properties.
These are just a few examples of the many industries where steel castings play a crucial role in providing reliable and durable components for various applications. The versatility of steel castings makes them a preferred choice in diverse sectors where strength, longevity, and performance are paramount.
Chapter 9: The Environmental Impact during Steel Casting Process
The steel casting process, like many industrial processes, can have potential environmental impacts. These impacts may include energy consumption, greenhouse gas emissions, waste generation, and resource depletion. However, there are several measures that can be taken to improve the sustainability of the steel casting process and minimize its environmental footprint:
1. Energy Efficiency:
- Implement energy-efficient technologies and practices to reduce energy consumption during the melting and casting processes.
- Optimize furnace operations to minimize heat losses and improve overall energy efficiency.
2. Emission Reduction:
- Use cleaner energy sources, such as renewable energy or lower-emission fuels, to reduce greenhouse gas emissions associated with the melting process.
- Install emission control technologies to capture and mitigate pollutants released during the melting and casting processes.
3. Waste Minimization and Recycling:
- Minimize waste generation by optimizing mold and core designs to reduce the amount of material waste.
- Implement recycling programs to recycle scrap steel and other materials, reducing the need for virgin resources.
4. Water Conservation:
- Implement water-saving technologies and practices to minimize water consumption during the casting process.
- Recycle and reuse water within the facility to reduce water demand.
5. Sustainable Materials:
- Source materials responsibly, considering factors such as recycled content and responsible mining practices.
- Opt for environmentally friendly binders and refractory materials used in mold and core preparation.
6. Process Optimization:
- Use advanced simulation and modeling tools to optimize the casting process, reducing the need for trial-and-error casting attempts.
- Employ process monitoring and control systems to ensure optimal process conditions and reduce material waste.
7. Environmental Management Systems:
- Implement environmental management systems and certifications (e.g., ISO 14001) to ensure compliance with environmental regulations and continuous improvement.
8. Research and Innovation:
- Invest in research and development to identify innovative technologies and materials that reduce environmental impacts.
- Explore alternative casting methods that have lower energy and resource requirements.
9. Life Cycle Assessment (LCA):
- Conduct a comprehensive life cycle assessment of the steel casting process to identify key environmental impacts and prioritize areas for improvement.
10. Stakeholder Engagement:
- Engage with employees, suppliers, customers, and the local community to raise awareness of environmental issues and promote sustainable practices.
By adopting these measures, steel casting manufacturers can reduce their environmental impact, improve resource efficiency, and contribute to a more sustainable and environmentally responsible manufacturing process.