Fig. 1 is an OM picture of the alloy structure of metal mold casting and conventional squeeze casting. As shown in Fig. 1a, the microstructure of the metal mold casting alloy is similar to that of the alloy with pressure of 0 MPa, that is, there are some sub grains in the grains, and there are massive mg12nd phases in the grain boundaries. However, due to the grain refinement effect of electromagnetic stirring, the grain size of rheo squeeze casting alloy (about 47 μ m) is smaller than that of metal mold casting alloy (about 52 μ m) when the pressure is 0 MPa. Compared with the metal mold casting alloy, the mg12nd phase is uniformly distributed in the alloy prepared by conventional squeeze casting, and the grain size (about 37 μ m) is smaller than that of the metal mold casting alloy, which is equivalent to that of the rheo squeeze casting alloy (80MPa and 120MPa). Figure 2 shows the XRD patterns and lattice constants of metal mold and conventional squeeze casting alloys. Similar to the rheo squeeze casting alloy, the microstructure of the alloy is composed of α – Mg matrix and mg12nd eutectic phase. The lattice constant of α – Mg in the metal mold casting alloy is smaller than that in the conventional squeeze casting alloy, which further indicates that the solid solubility of Nd in α – Mg increases with the increase of pressure, and more nd atoms dissolve into the α – Mg matrix in the conventional squeeze casting alloy.
Figure 3 shows the mechanical properties of metal mold casting alloy, conventional squeeze casting alloy and rheo squeeze casting alloy. Compared with the metal mold casting alloy, the amount of eutectic phase in the conventional squeeze casting alloy is less, the distribution is more uniform, and the grain size is smaller, so the yield strength and tensile strength are higher, but the elongation decreases. This may be caused by plastic deformation between adjacent particles. The yield strength and tensile strength of rheo squeeze casting alloy are higher than those of the other two alloys, but the elongation is lower. This may be due to the large plastic deformation of primary phase particles in rheo squeeze casting alloy, and the oxidation of semi-solid slurry is easy to occur in the process of moving, which may lead to some oxidation inclusions in the forming alloy, so the plasticity of the alloy decreases.
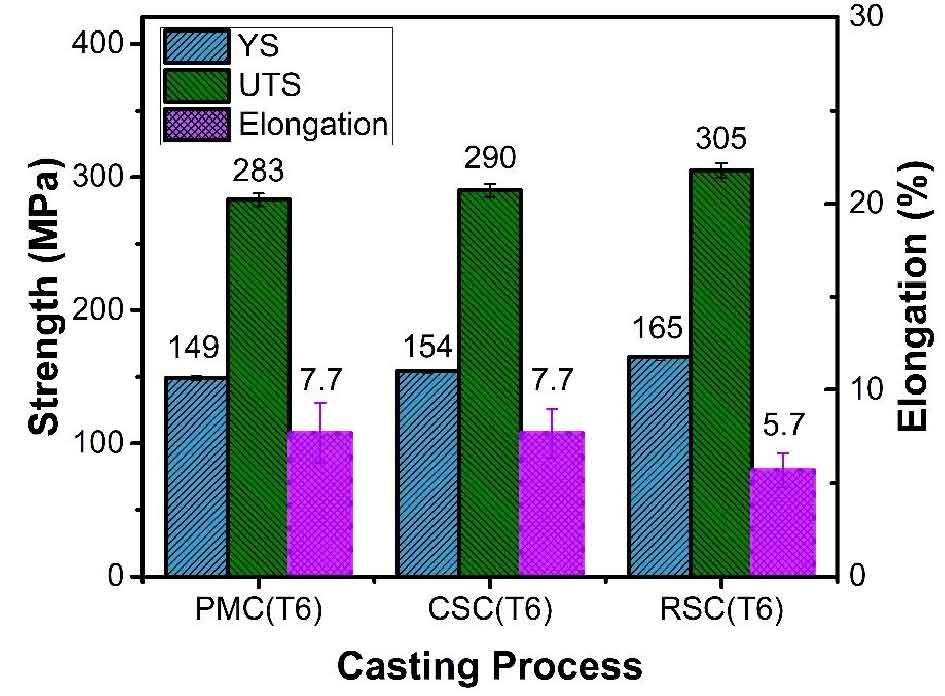
Figure 4 shows the fracture morphology of the alloy obtained by different forming methods. It can be seen from the figure that the fracture surface is mainly composed of some cleavage surface and eutectic structure, but the fracture mechanism of different forming methods is different. For the metal mold casting alloy and the conventional squeeze casting alloy, the crack mainly propagates along the eutectic structure, that is, the fracture mode is mainly intergranular fracture (as shown in Fig. 5A and B, arrow a). And for flow
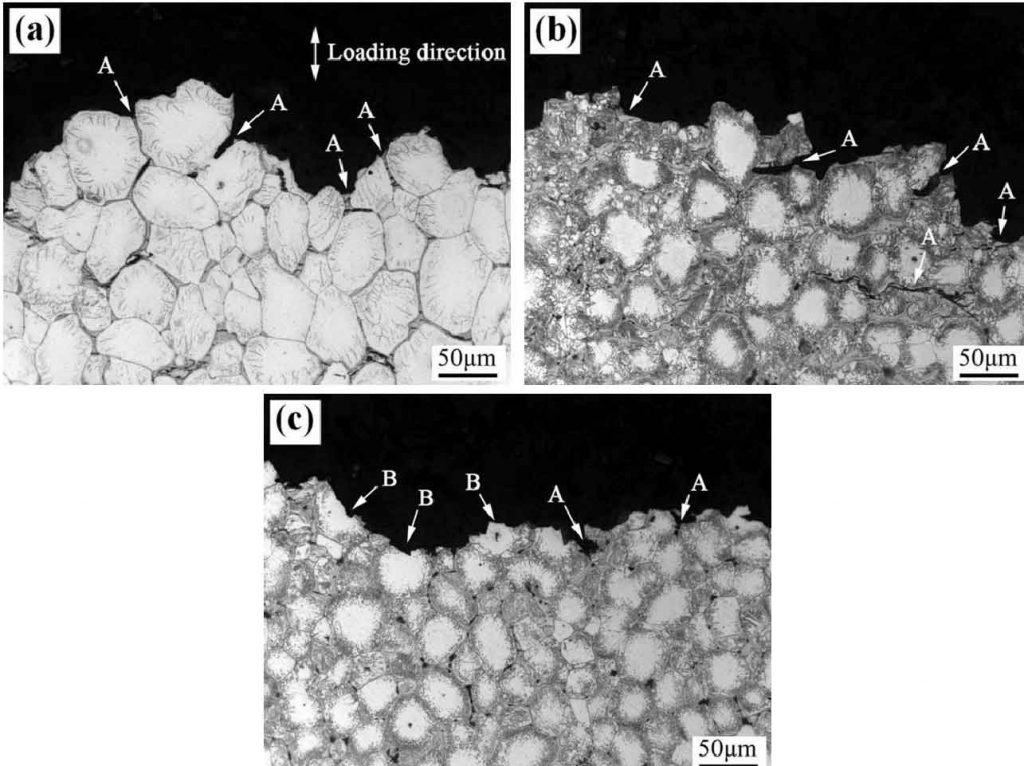
The results show that the cracks propagate along the primary particles (arrow B in Fig. 5C) and the secondary solidification structure (arrow A in Fig. 5C), indicating that the fracture mode is mixed fracture. Comparing Fig. 6C, FIG. 1a and Fig. 1b, it can be found that the grain size of rheoform alloy (about 35 μ m) is smaller than that of metal mold casting alloy and conventional squeeze casting alloy. In addition, compared with the metal mold casting alloy and the conventional squeeze casting alloy, the eutectic structure of rheo squeeze casting alloy is smaller and more evenly distributed among the particles. It can be seen that the amount and distribution of eutectic phase have a great influence on the fracture behavior of the alloy. The more the amount of eutectic phase is, the more uneven the distribution is, and the easier the crack initiation is.
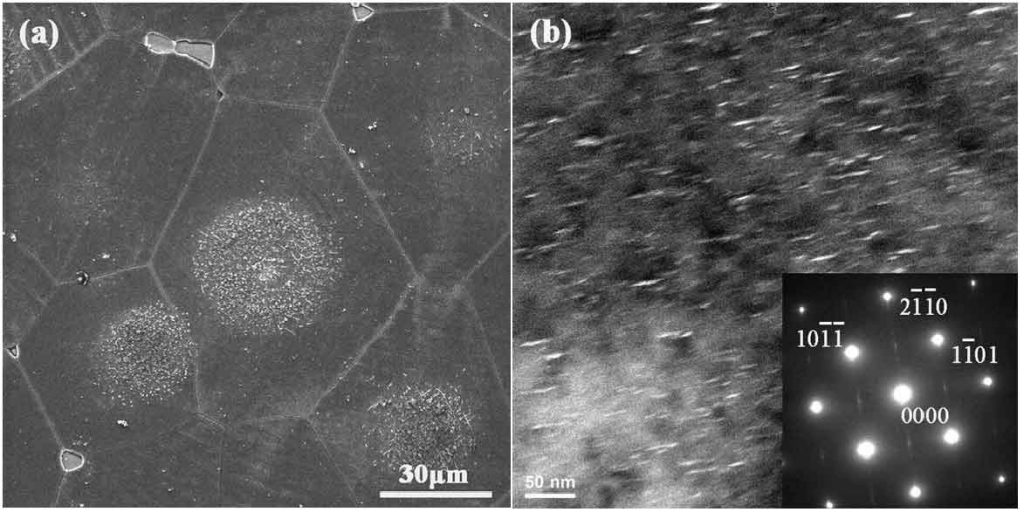
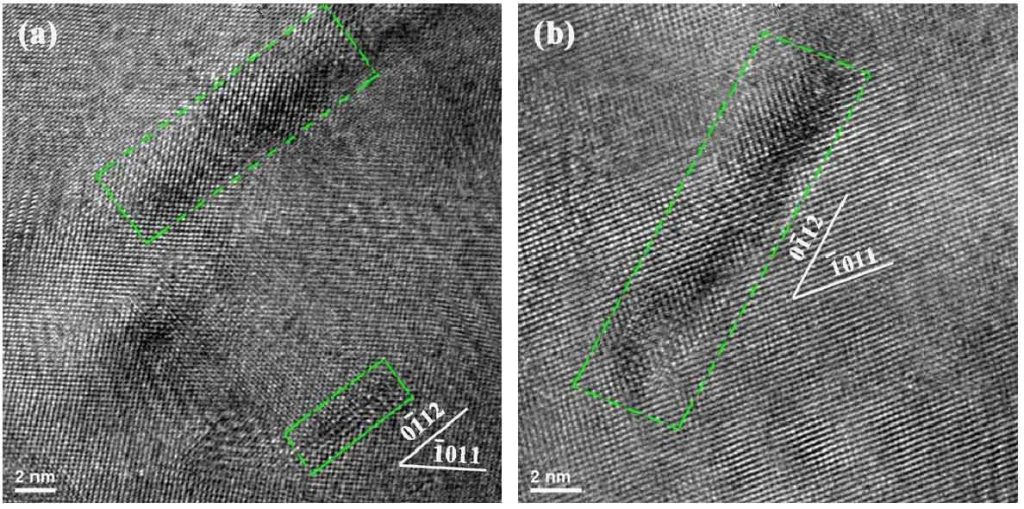
Figure 7 shows the SEM and TEM images of the alloy after T6 treatment. After T6 treatment, the grain size of the alloy is 69 μ m, which is much larger than that of the rheo squeeze casting alloy (the grain size is 27 μ m when the pressure is 120 MPa). Similar to the microstructure of rheo squeeze casting alloy, Zr containing particles also exist in the α – Mg grains of the metal mold casting alloy, and long rod-shaped zn2zr3 phase exists around the Zr containing particles. TEM dark field images and diffraction patterns show that the precipitated phase in the alloy is mainly β′, and according to the HRTEM diagram (Fig. 8), the β′ precipitated in the metal mold casting alloy is smaller than that in the rheo squeeze casting alloy.
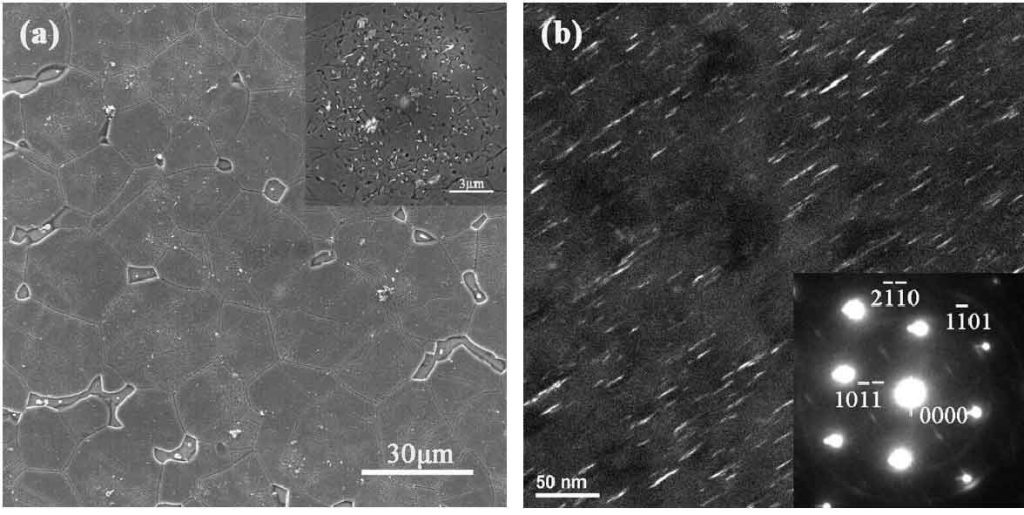
Figure 9 shows the SEM and TEM images of conventional squeeze casting alloy nz30k. The grain size of the alloy is about 33 μ m (Fig. 9a). Similar to the other two alloys, long rod like zn2zr3 phase is found around Zr containing particles in α – Mg grains. TEM dark field images and corresponding diffraction patterns show that the precipitates in conventional squeeze casting nz30k alloy are mainly β′ (Fig. 9b). The fine discoid β″ phase in the rheo squeeze casting alloy was not detected in the metal mold casting alloy and the conventional squeeze casting alloy.
Generally speaking, the grains can be refined by applying pressure during solidification. On the one hand, the air gap between the slurry and the mold wall is reduced, which increases the heat transfer coefficient. On the other hand, the phase diagram of the alloy will be affected by the pressure during solidification, and the liquidus, solidus and eutectic point of the alloy will change. The nucleation rate of the alloy melt increases and the grains are refined. In the process of electromagnetic stirring, the particles grow up through aging, so the primary particle size of rheo squeeze casting alloy is larger than that of conventional squeeze casting alloy. However, although the particle size is small, the mechanical properties of the conventional squeeze casting alloy are lower than those of the rheo squeeze casting T6 alloy (FIG. 10).
According to the formula, the contribution of grain boundary strengthening in the metal mold casting alloy is 55 ~ 60 MPa, and that in the squeeze casting alloy is 70 ~ 77 MPa, which is less than that in the rheo squeeze casting alloy of 75 ~ 83 MPa. The contribution of precipitation strengthening σ PPT can be calculated according to the formula, the experimental value of yield strength minus the contribution of grain boundary strengthening and precipitation strengthening. The σ ppt of T6 rheo squeeze casting alloy is 67 ~ 74 MPa, which is equivalent to that of metal mold casting alloy, and is higher than that of conventional squeeze casting alloy (56 ~ 63 MPa). Based on the above results, the following conclusions can be drawn: compared with the metal mold casting alloy, the higher yield strength of rheo squeeze casting alloy is mainly due to the grain refinement and the greater contribution of grain boundary strengthening; compared with the conventional squeeze casting alloy, the higher yield strength of rheo squeeze casting alloy is mainly due to the stronger precipitation strengthening effect.