Abstract
This paper presents a comprehensive study on the casting process optimization of knuckle castings for railway freight cars. Traditional casting methods often result in defects such as sand inclusions, porosity, and surface irregularities, which significantly impact the quality and durability of the final product. To address these issues, various measures including the adoption of a double-pass double-injection pouring cup, improvement of pouring methods, design of an integrated splicing refractory runner, and utilization of a porous grid exhaust valve were implemented. These changes led to a significant improvement in the quality of the knuckle castings, with the qualified rate increasing from 82% to over 96%. The research provides valuable insights into the casting process optimization of complex cast steel components, specifically for railway applications.
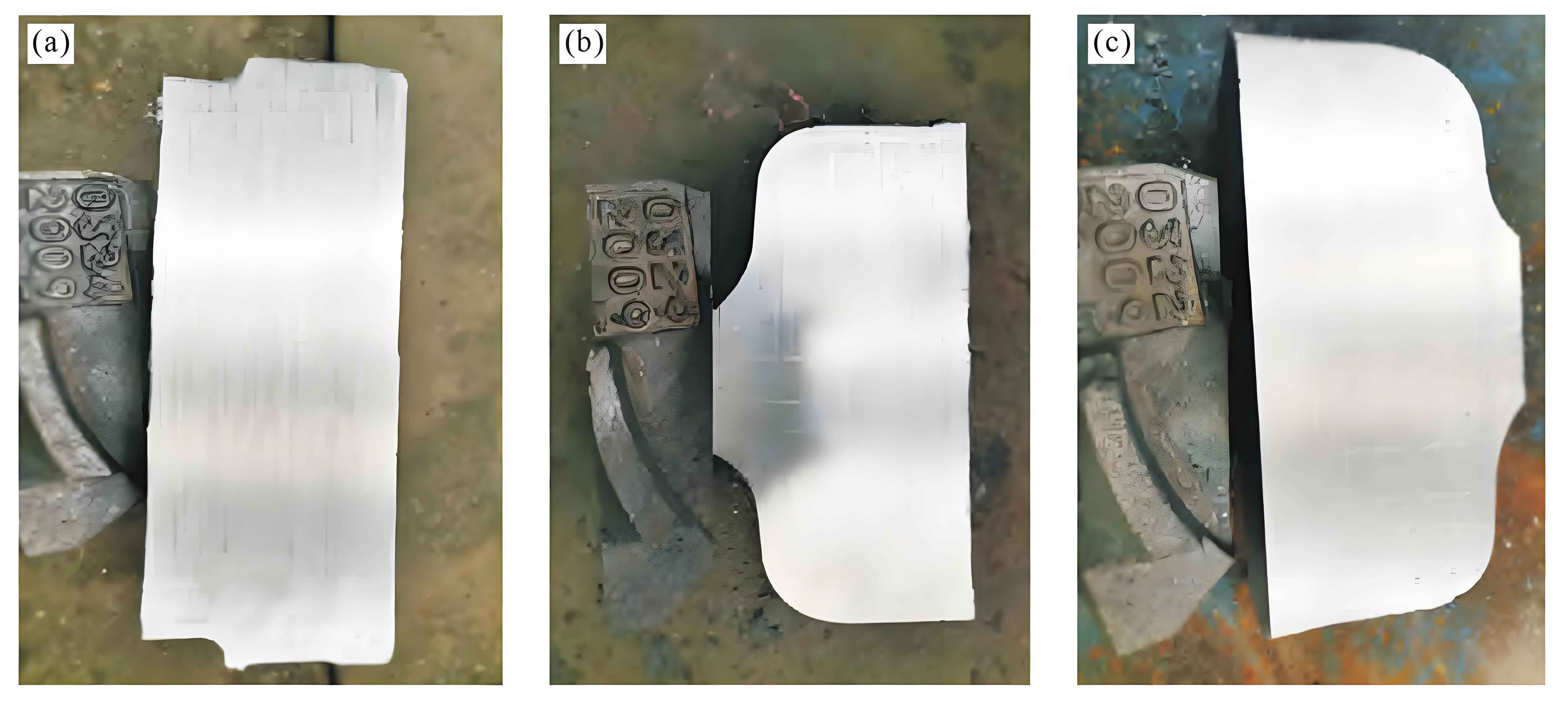
Keywords: knuckle casting, casting process, casting defect, railway freight cars
1. Introduction
Railway freight cars are essential components of modern transportation systems, facilitating the movement of goods over long distances. The safety and reliability of these cars depend significantly on the quality of their components, particularly the coupling devices. The knuckle, as a vital part of the coupling mechanism, bears the brunt of the longitudinal forces and impacts during train operation. Therefore, ensuring the highest possible quality of knuckle castings is crucial.
2. Problem Analysis of Traditional Casting Process
The traditional casting process for knuckle castings involves several challenges that contribute to casting defects. In the pouring system, molten steel flowing through the sand mold can easily cause sand washing, leading to sand inclusions and surface irregularities. Additionally, the traditional exhaust system, which relies on drilled air holes, often results in floating sand that can be trapped within the casting, causing sand inclusions and material loss during cutting operations.
2.1 Sand Inclusions
During the pouring process, molten steel can erode the sand mold, causing sand particles to become embedded within the casting. This issue is exacerbated by the high velocity and turbulence of the molten steel as it enters the mold. The sand inclusions can compromise the mechanical properties of the knuckle and increase the risk of failure during operation.
2.2 Porosity
Trapped gases within the mold can lead to porosity in the final casting. These gases can originate from the decomposition of organic binders used in the sand mold or from entrapped air during pouring. Porosity reduces the strength and fatigue resistance of the casting.
2.3 Surface Irregularities
Surface irregularities, such as watermarks and flow lines, can occur due to uneven flow of molten steel within the mold. These defects not only impact the aesthetic appearance of the casting but can also affect its functional performance.
3. Optimization of the Casting Process
To address the challenges associated with the traditional casting process, several optimization measures were implemented. These measures aimed to reduce casting defects and improve the overall quality of the knuckle castings.
3.1 Pouring System Optimization
3.1.1 Introduction of Double-Pass Double-Injection Pouring Cup
A double-pass double-injection pouring cup was designed to replace the traditional single-pass pouring cup. This new design effectively reduces the velocity and turbulence of the molten steel as it enters the mold, minimizing sand washing and sand inclusions . The pouring cup is made of refractory material to withstand the high temperatures of the molten steel.
3.1.2 Improved Pouring Method
A modified pouring method was adopted, involving the initial filling of the pouring cup to two-thirds capacity with a large flow rate, followed by a slower flow rate to top up the cup. This approach ensures that the pouring cup remains full during the entire pouring process, minimizing the entrainment of air and reducing porosity.
3.2 Runner System Optimization
3.2.1 Integrated Splicing Refractory Runner
A new integrated splicing refractory runner was designed to replace the traditional sand-based runner system. This refractory runner is more resistant to erosion by molten steel, reducing sand washing and improving the overall flow of the molten steel within the mold .
3.3 Exhaust System Optimization
3.3.1 Porous Grid Exhaust Valve
A porous grid exhaust valve was utilized instead of drilled air holes. This valve effectively prevents floating sand from entering the casting while allowing trapped gases to escape during pouring . The porous grid also acts as a filter, trapping larger particles that could otherwise become embedded within the casting.
3.4 Sand and Mold Optimization
Various types of core sand were tested to determine the optimal material for use in the mold. The tests focused on factors such as gas release, tensile strength, and bending strength to identify the sand that would produce the fewest casting defects.
Table 1: Properties of Tested Core Sands
Sand Type | Gas Release (mL/g) | Ultimate Tensile Strength (MPa) | Bending Strength (MPa) |
---|---|---|---|
Sand A | 112.6 | 3.88 | 4.5 |
Sand B | 8.3 | 4.52 | 15.7 |
Sand C | 4.61 | 10.0 | 1.43 |
Sand D | 15.6 | 3.58 | 4.34 |
3.5 Special Tooling Design
Specialized tooling was designed to facilitate the casting process and minimize manual intervention. This included the development of custom sand boxes that optimized the flow of molten steel and reduced turbulence during pouring.
4. Process Validation and Results
To validate the effectiveness of the optimized casting process, a series of trials were conducted. A total of 24 test knuckle castings were produced and analyzed. Dissection of the castings revealed a dense and uniform microstructure, indicating a significant improvement in casting quality .
Based on the positive results from the initial trials, a larger-scale production run was undertaken. A total of 320 knuckle castings were produced using the optimized process. Random sampling and dissection of the castings confirmed the consistent improvement in quality, with the qualified rate exceeding 96%.
Table 2: Comparison of Casting Quality Before and After Optimization
Metric | Before Optimization | After Optimization |
---|---|---|
Sand Inclusions | High | Low |
Porosity | Moderate | Low |
Surface Irregularities | High | Low |
Qualified Rate | 82% | 96%+ |
5. Conclusion
The optimization of the casting process for knuckle castings for railway freight cars has led to a significant improvement in casting quality. The implementation of a double-pass double-injection pouring cup, integrated splicing refractory runner, porous grid exhaust valve, and specialized tooling has effectively reduced casting defects such as sand inclusions, porosity, and surface irregularities. The resulting improvement in the qualified rate demonstrates the effectiveness of these optimization measures and highlights their potential for application in other complex casting processes.