The picture shows the SEM morphology of the cross section of the nitrocarburized sample at the edge of lzqt600-3 ductile iron profile. After nitrocarburizing at different temperature, holding time and the ratio of NH3 to CO2, different thickness of nitrided layer was formed on the surface of the sample. Oxide layers (OLS), compound layers (CLS) and diffusion layers (DLS) were formed on the surface of the sample, and the morphology of the infiltrated layer at 1 / 2R was the same as that at the center. Taking the edge as an example, when the nitrocarburizing temperature is 540 ℃, it can be seen from Fig. (a) (b) (c) that the diffusion of the nitrided layer is not obvious and the diffusion layer is thin. This is because the nitrocarburizing temperature is low, the decomposed nitrogen and carbon elements are difficult to enter into the matrix material, resulting in the failure of lzqt600-3 ductile iron profile to form an obvious diffusion layer; when the nitrocarburizing temperature rises to 560 ℃ When the temperature of nitrocarburizing is 580 ℃, a large number of loose holes and cracks appear on the surface of lzqt600-3 ductile iron profile.
Holes and cracks appear in the compound layer of the sample, which is caused by the re bonding of active nitrogen atoms and the separation of nitrogen molecules from the surface of the matrix. If the temperature is too low, it will affect the diffusion of elements, and it is not easy to form the infiltration layer on the surface of the sample. If the temperature is too high, there will be more holes on the surface of the material, resulting in the decline of mechanical properties.
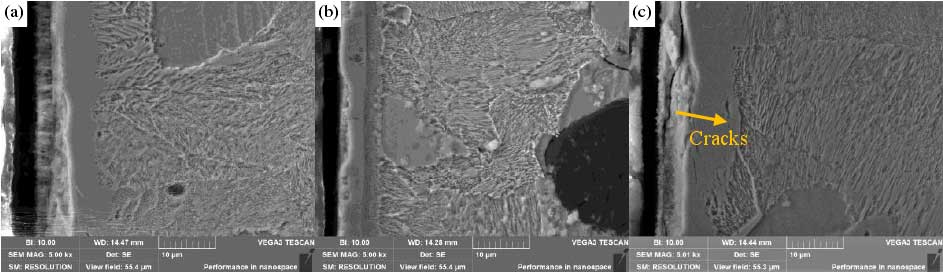
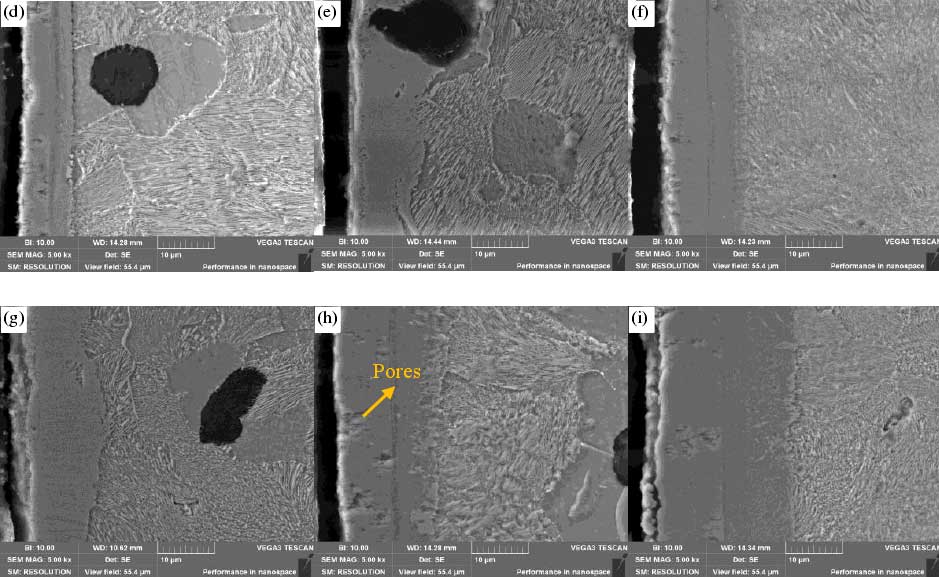
The thickness of the layer is also affected by the time. The results show that the nitriding temperature is 540 ℃, 560 ℃ and 580 ℃, and the holding time is 2 h, 4 h and 6 h, respectively. However, the defects of the surface layer will also appear due to the prolongation of time. For example, there are a lot of loose holes in the OLS layer and CLS layer. The longer the infiltration time is, the thicker the porous layer is. The reason for the formation of the porous layer is that the N atoms needed for the nitriding are decomposed from the nitrogenous compounds, and these N atoms are re combined to form nitrogen and escape from the surface of the matrix to form holes. Another reason may be due to the slight damage to the surface layer in the cutting process when sampling the cross-section of nitrocarburizing sample, resulting in the edge holes and cracks of the surface compound layer.