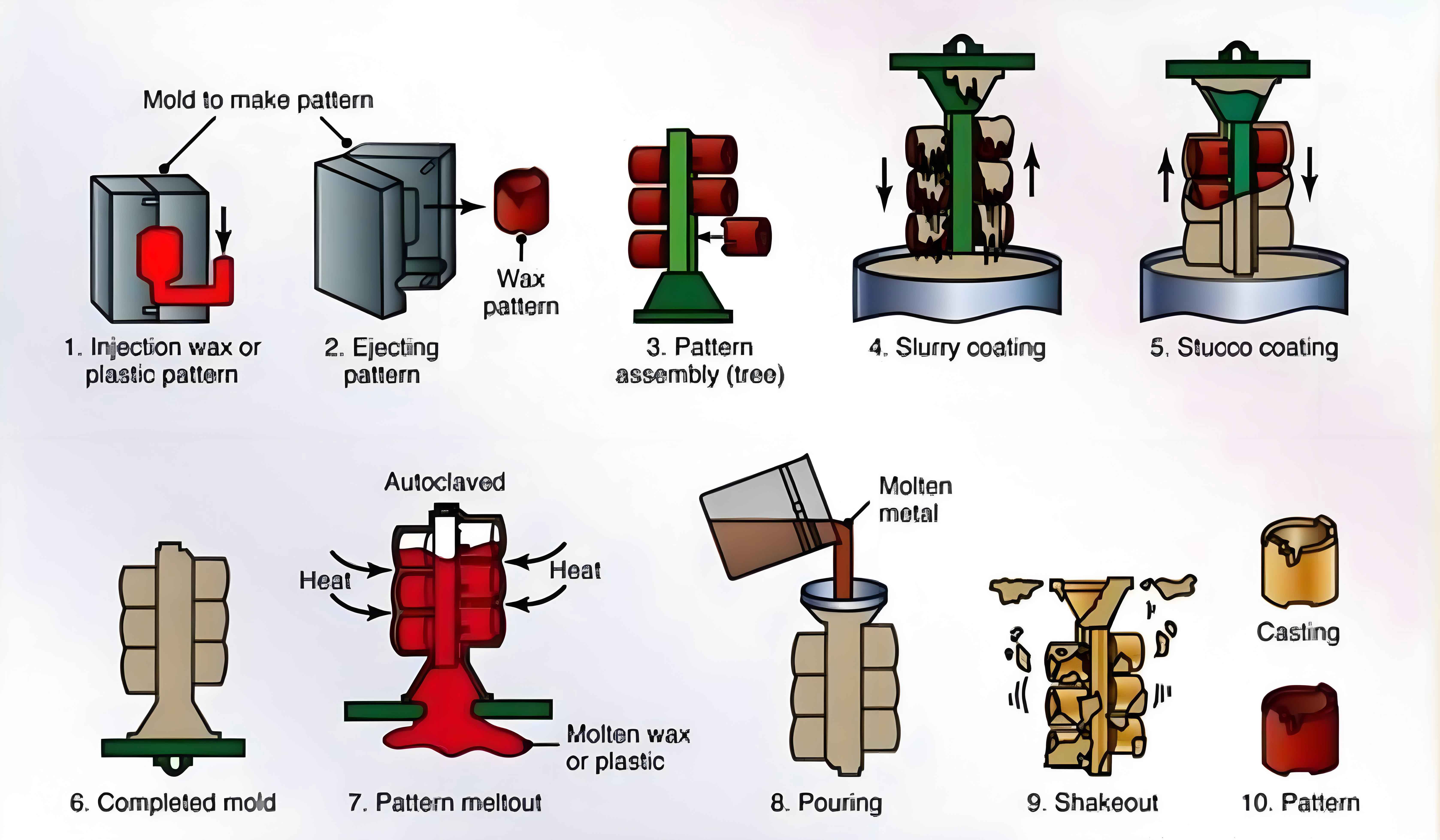
Investment casting, also known as lost-wax casting, is a precise and versatile process used in manufacturing complex metal parts. Incorporating sustainability into investment casting involves using eco-friendly materials and energy-efficient practices to reduce environmental impact. Here’s an overview of how sustainability can be achieved in investment casting:
Eco-Friendly Materials
- Biodegradable Waxes and Patterns:
- Use of biodegradable or bio-based waxes for creating the patterns.
- Alternative materials like PLA (polylactic acid), which are derived from renewable resources, can be used for 3D printing patterns.
- Recycled Metals:
- Utilizing recycled metals in the casting process reduces the need for virgin materials and minimizes mining activities.
- Ensuring the quality of recycled metals through proper sorting and refining processes.
- Environmentally Friendly Coatings:
- Adoption of water-based ceramic slurries and binders for shell building.
- Use of non-toxic and low-VOC (volatile organic compounds) coatings.
Energy-Efficient Practices
- Optimizing Energy Consumption:
- Implementing energy-efficient furnaces and kilns for melting and casting processes.
- Using waste heat recovery systems to utilize excess heat for other processes or heating needs.
- Process Optimization:
- Streamlining the casting process to minimize energy use, such as optimizing the mold preheating schedule and improving the efficiency of pattern removal.
- Employing simulation software to design molds and predict casting outcomes, reducing the need for trial and error and saving energy.
- Renewable Energy Integration:
- Incorporating renewable energy sources such as solar, wind, or biomass for powering the casting facilities.
- Installing solar panels on the roofs of manufacturing plants to supply clean energy.
Waste Reduction and Recycling
- Shell and Core Recycling:
- Recycling used ceramic shells and cores by crushing and reprocessing them for use in new molds.
- Implementing systems for collecting and reusing spent shell materials.
- Wax Recovery Systems:
- Installing wax recovery systems to reclaim wax from used molds and reuse it in future casting cycles.
- Reducing the amount of wax waste generated and lowering the demand for new wax.
- Scrap Metal Recycling:
- Recycling scrap metal generated during the trimming and finishing processes.
- Partnering with recycling companies to ensure proper handling and processing of metal waste.
Water Conservation
- Water Recycling Systems:
- Implementing closed-loop water systems to recycle water used in the investment casting process.
- Treating wastewater to remove contaminants and reuse it in the production cycle.
- Efficient Water Usage:
- Using water-efficient practices in cleaning and cooling processes.
- Monitoring water usage and implementing measures to reduce consumption.
Sustainable Facility Management
- Green Building Practices:
- Designing and constructing casting facilities with sustainable materials and energy-efficient designs.
- Incorporating natural lighting, efficient HVAC systems, and sustainable landscaping.
- Environmental Management Systems:
- Implementing ISO 14001 or similar environmental management systems to continuously improve environmental performance.
- Regularly auditing and reviewing environmental practices to ensure compliance and identify areas for improvement.
Research and Development
- Innovative Materials and Processes:
- Investing in research to develop new eco-friendly materials and more efficient casting processes.
- Collaborating with universities and research institutions to stay at the forefront of sustainable casting technologies.
- Employee Training and Awareness:
- Providing training programs for employees on sustainable practices and the importance of environmental conservation.
- Encouraging a culture of sustainability within the organization.
By adopting these eco-friendly materials and energy-efficient practices, the investment casting industry can significantly reduce its environmental footprint, contributing to a more sustainable future.