The steel casting process has long been a vital part of industrial manufacturing, but in today’s world, it is imperative to adopt sustainable approaches to minimize its environmental impact and ensure its long-term viability. This article aims to explore the various sustainable strategies that can be integrated into the steel casting process.
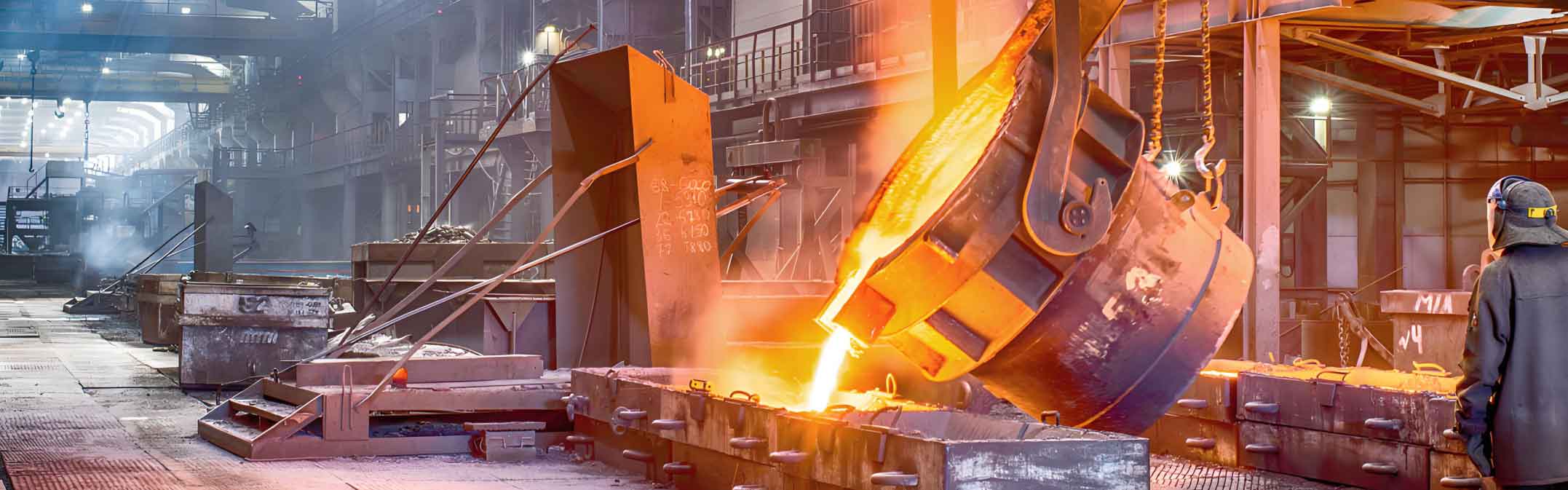
Introduction
The steel casting process plays a crucial role in numerous industries, providing essential components for machinery, infrastructure, and consumer products. However, this process also poses significant challenges in terms of resource consumption, energy usage, and environmental emissions. Embracing sustainable practices is not only an ethical imperative but also a strategic necessity for the continued success of the steel casting industry.
Understanding the Steel Casting Process
Before delving into sustainable approaches, it is essential to have a clear understanding of the steel casting process itself.
The steel casting process typically involves the following steps:
- Pattern Making: Creating a pattern that represents the shape and dimensions of the desired casting.
- Mold Preparation: Preparing the mold, which can be made of sand, metal, or other materials, to receive the molten steel.
- Melting: Heating the steel to its molten state in a furnace.
- Pouring: Pouring the molten steel into the mold.
- Solidification and Cooling: Allowing the steel to solidify and cool within the mold.
- Ejection and Finishing: Removing the solidified casting from the mold and performing any necessary finishing operations.
Environmental Challenges of the Steel Casting Process
The traditional steel casting process presents several environmental challenges:
- Energy Consumption: The melting process requires a significant amount of energy, often derived from non-renewable sources.
- Greenhouse Gas Emissions: The combustion of fossil fuels in furnaces leads to the release of greenhouse gases such as carbon dioxide.
- Waste Generation: The process generates various types of waste, including slag, mold materials, and rejected castings.
- Resource Depletion: The extraction and processing of raw materials for steel production contribute to the depletion of natural resources.
Sustainable Approaches in Materials Selection
Use of Recycled Steel
Recycled steel can significantly reduce the demand for virgin materials and the associated environmental impacts.
Benefits of Using Recycled Steel | Examples of Applications |
---|---|
Reduced energy consumption during production | Automotive components, construction elements |
Lower greenhouse gas emissions | Machinery parts, industrial equipment |
Selection of Low-Impact Alloys
Alloys that require fewer rare or toxic elements can minimize the environmental footprint.
Low-Impact Alloys and Their Benefits | Industries Where They Are Applied |
---|---|
Aluminum-steel alloys for reduced weight and improved fuel efficiency | Aerospace and transportation |
Nickel-free stainless steels for lower toxicity | Medical devices and food processing equipment |
Energy Efficiency Improvements
Advanced Furnace Technologies
Newer furnace designs and control systems can enhance energy efficiency.
Advanced Furnace Types and Their Features | Energy Savings Achieved |
---|---|
Induction furnaces with precise temperature control | Up to 30% energy reduction |
Electric arc furnaces with efficient power management | Up to 25% energy savings |
Heat Recovery Systems
Recovering and reusing waste heat can lead to significant energy savings.
Heat Recovery Methods and Their Applications | Estimated Energy Recovery |
---|---|
Installing heat exchangers in exhaust gases | Up to 20% of total energy input |
Utilizing waste heat for preheating molds | Up to 15% energy efficiency improvement |
Waste Management and Recycling
Minimization of Waste Generation
By optimizing process parameters and mold designs, waste can be reduced.
Waste Minimization Techniques | Estimated Waste Reduction |
---|---|
Precision pouring to avoid overflows | Up to 10% less waste |
Improved mold venting to prevent defects | Up to 8% reduction in rejected castings |
Recycling of Waste Materials
Slag, mold materials, and scrap can be recycled for other uses.
Recyclable Waste Materials and Their Potential Uses | Examples of Recycling Processes |
---|---|
Slag for road construction and cement production | Crushing and processing |
Sand from molds for reuse in new molds | Sieving and cleaning |
Water Conservation Measures
Closed-Loop Cooling Systems
Implementing closed-loop systems can minimize water consumption.
Benefits of Closed-Loop Cooling | Industries Adopting This Approach |
---|---|
Reduced water withdrawal from natural sources | Heavy machinery manufacturing |
Lower wastewater discharge | Metal processing plants |
Water Treatment and Reuse
Treating and reusing process water can further enhance water conservation.
Water Treatment Methods and Their Effectiveness | Percentage of Water Reuse Achieved |
---|---|
Filtration and chemical treatment | Up to 70% water reuse |
Reverse osmosis for purification | Up to 85% recycled water |
Emission Control and Air Quality Improvement
Installation of Pollution Control Equipment
Devices such as scrubbers and filters can reduce emissions.
Pollution Control Devices and Their Functions | Reduction in Emissions |
---|---|
Particulate matter filters to capture dust | Up to 90% reduction in PM emissions |
Gas scrubbers for removing harmful gases | Up to 80% reduction in SOx and NOx emissions |
Optimization of Combustion Processes
Improved combustion techniques can lower emissions.
Combustion Optimization Methods | Impact on Emission Levels |
---|---|
Oxygen enrichment for better fuel efficiency | Up to 30% lower emissions |
Flue gas recirculation to reduce NOx formation | Up to 25% reduction in NOx emissions |
Employee Training and Awareness
Education on Sustainable Practices
Ensuring that workers understand the importance of sustainability and their role in achieving it.
Training Modules and Their Objectives | Outcome of Training |
---|---|
Energy conservation awareness courses | Employees take proactive steps to save energy |
Waste management training | Decreased waste generation through proper handling |
Incentives for Sustainable Actions
Motivating employees to contribute to sustainability efforts.
Incentive Programs and Their Impact | Increase in Employee Engagement |
---|---|
Rewards for suggesting energy-saving ideas | Up to 20% more employee participation |
Recognition for waste reduction achievements | Up to 15% improvement in waste management |
Case Studies of Sustainable Steel Casting Facilities
Let’s look at some real-world examples of steel casting facilities that have successfully implemented sustainable approaches:
Facility Name | Sustainable Initiatives Undertaken | Measurable Outcomes |
---|---|---|
Facility A | Adoption of recycled steel, energy-efficient furnaces, and water recycling | 40% reduction in energy consumption, 30% less water usage, and 25% increase in recycled material usage |
Facility B | Installation of emission control equipment, waste minimization strategies, and employee training programs | 55% reduction in emissions, 20% less waste generated, and improved employee satisfaction |
Challenges and Barriers to Adoption
High Initial Investment
The implementation of sustainable technologies and practices often requires significant upfront capital.
Resistance to Change
Workers and management may be reluctant to adopt new methods and processes.
Lack of Awareness and Knowledge
Limited understanding of sustainable options and their benefits can hinder progress.
Future Trends and Outlook
The future of the steel casting process is likely to see even greater emphasis on sustainability:
- Development of bio-based materials and coatings for improved environmental performance.
- Integration of Internet of Things (IoT) for real-time monitoring and optimization of sustainability parameters.
Conclusion
Sustainable approaches in the steel casting process are not only essential for the protection of the environment but also offer numerous economic and competitive advantages. By embracing these strategies, the steel casting industry can continue to thrive while minimizing its ecological footprint. It is the collective responsibility of all stakeholders – manufacturers, policymakers, and consumers – to drive the adoption of sustainable practices and shape a more sustainable future for the steel casting process.