Scale formation, which is the oxidation of the material’s surface during heat treatment, can lead to several issues such as reduced mechanical properties, surface defects, and dimensional changes. Minimizing oxidation is crucial to maintain the integrity and quality of the heat-treated components. Here are some strategies to tackle scale formation and minimize oxidation during heat treatment:
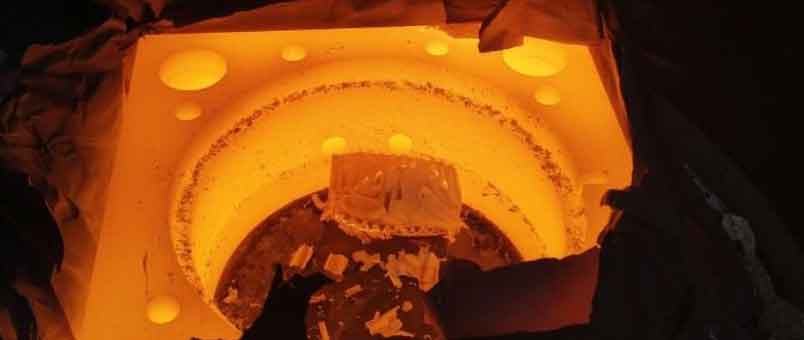
1.Controlled Atmosphere:
Utilize a controlled atmosphere within the heat treatment furnace or chamber to minimize the presence of oxygen and prevent oxidation. Common methods include:
- Gas atmosphere: Use an inert gas such as nitrogen, argon, or helium to create a protective environment and displace oxygen.
- Vacuum heat treatment: Conduct heat treatment in a vacuum environment to eliminate the presence of oxygen.
2.Protective Coatings:
Apply protective coatings on the component surface to act as a barrier against oxygen contact and prevent oxidation. Coating materials can include refractory coatings, metallic coatings, or ceramic coatings, depending on the specific heat treatment process and material.
3.Pack or Case Hardening:
In certain heat treatment processes like pack or case hardening, materials are surrounded by a carbon-rich medium. The presence of carbon in the environment helps to reduce the oxidation potential and minimize scale formation during heating.
4.Inert Gas Blanketing:
Implement inert gas blanketing techniques, such as nitrogen or argon, during the heating and cooling stages of the heat treatment process. Inert gas blanketing helps create an oxygen-free environment around the components and reduces the chances of oxidation.
5.Controlled Heating and Cooling Rates:
Properly control the heating and cooling rates during the heat treatment process to minimize the exposure of the material to high temperatures and reduce the duration of the oxidation-prone temperature range. Rapid and uniform heating and controlled cooling can help minimize oxidation and scale formation.
6.Surface Cleaning:
Thoroughly clean the component surface before heat treatment to remove any contaminants, oils, greases, or dirt that can contribute to oxidation and scale formation. Utilize appropriate cleaning methods, such as degreasing or acid cleaning, to ensure a clean surface.
7.Reduce Exposure Time:
Minimize the exposure time of the material to high temperatures during heat treatment. Optimize the process parameters, such as temperature and time, to achieve the desired transformation while reducing the oxidation potential.
8.Post-Treatment Cleaning:
After heat treatment, remove any scales or oxidation layers that may have formed on the component surface. Employ suitable cleaning methods such as pickling, abrasive cleaning, or chemical cleaning to eliminate the scales and restore the surface finish.
9.Continuous Monitoring:
Implement continuous monitoring of the heat treatment process, including temperature, atmosphere composition, and other critical parameters. Regularly inspect and maintain the heat treatment equipment to ensure consistent and controlled conditions.
10.Quality Control and Inspection:
Conduct quality control measures, including visual inspection, non-destructive testing, and dimensional checks, to detect any surface defects or issues resulting from oxidation. Implement appropriate corrective actions if oxidation-related defects are identified.
By incorporating these strategies into the heat treatment process, manufacturers can minimize oxidation and scale formation, preserving the material’s quality and performance. It is important to consult with heat treatment experts, metallurgists, and process engineers to develop the most suitable approaches for specific materials, components, and heat treatment requirements.