The microstructure after heat treatment was observed and studied. It was found that there were various sizes of holes left by eutectic phase with low melting point near the grain boundary after solution treatment (see Fig. 1). EDS analysis shows that the undissolved eutectic phase is found at the grain boundary of 7075 alloy by rheo squeeze casting, while the early dissolved eutectic phase with low melting point produces initial melting holes at the intersection and near the grain boundary. The tensile fracture of 7075 alloy formed by rheo squeeze casting after T6 heat treatment was dissected to make metallographic specimen. SEM scanning showed that there were various primary melting holes with different sizes along the grain boundary. As shown in Fig. 2, the primary melting holes were formed at the initial stage of solution treatment, and the melting points of some eutectic phases were lower than T6 The solid solution temperature of the treatment first melted and then left holes. The size and distribution of initial melting voids seriously affect the comprehensive mechanical properties of the alloy, especially the plasticity. Primary melting mainly refers to the intergranular or interdendritic low melting point phase formed by segregation during solidification. In the subsequent heating process, local melting occurs below the solidus temperature, which has a great impact on the overall mechanical properties of the alloy.
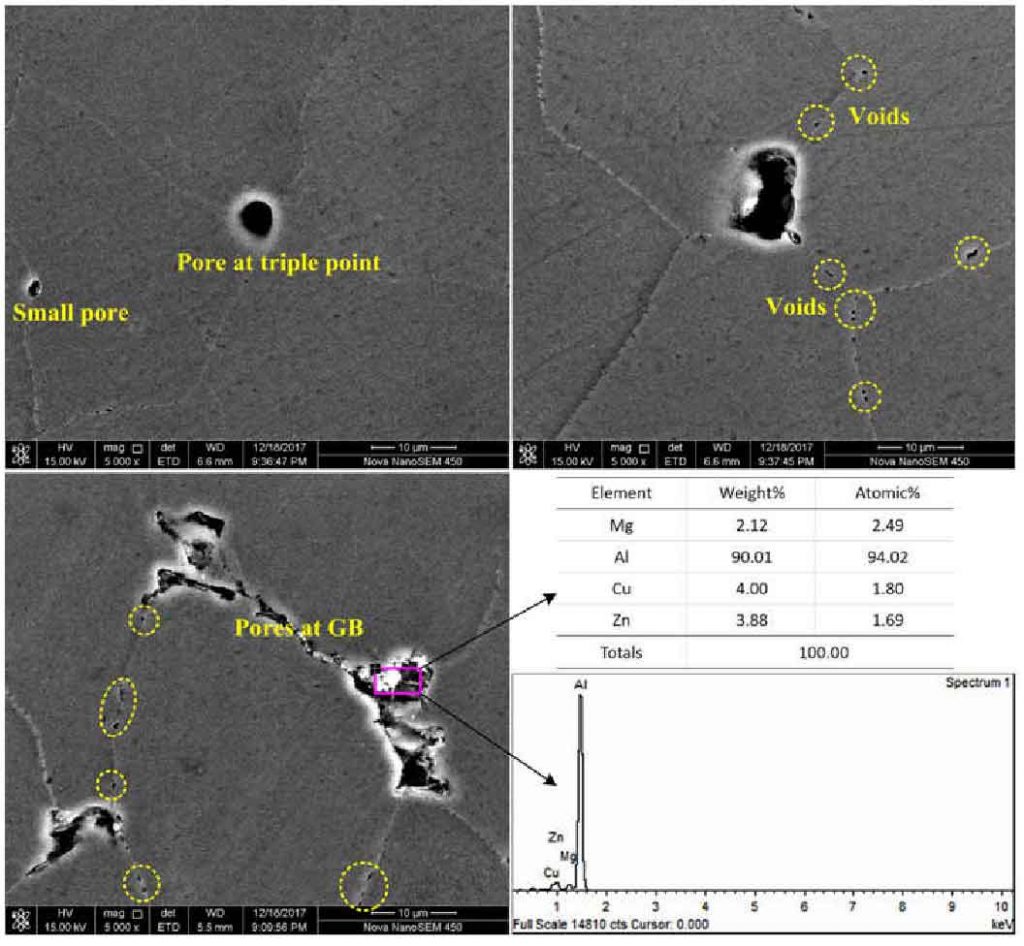
The microstructure of fracture surface of 7075 alloy formed by T6 rheo squeeze casting with good tensile plasticity was further analyzed. Different pore like tear bands were found at the dimples of fracture surface, but no pore like tear was found at the large compact dimples, as shown in Fig. 3 (a-b). According to the microstructure of fracture zone of tensile fracture, when the tensile specimen is subjected to large tensile stress, the strength near the primary melting hole is the weakest. The first dissociation is at the grain boundary with primary holes, tearing along the holes. When the adjacent holes also begin to tear, the hole expansion gradually merges with each other, thus forming a larger tearing zone. The tensile fracture mechanism is shown in the figure below 3 (c).
Therefore, the decrease of macro plasticity and other properties of 7075 alloy formed by rheological extrusion casting after T6 heat treatment reflects that the micro defects are pores and various small pores. It is found from Fig. 3 (a-b) that the fracture surface of the heat-treated tensile specimen is composed of large dimples, flat areas, compact shallow dimples and tearing ridges. With the increase of tensile stress, the pores and cavities combine and expand to form a tearing ridge until the final fracture. As shown in Figure 4, the equivalent stress distribution model of a hole under tensile stress is constructed by using ANSYS software, and the stress distribution of a single hole, the equivalent stress field distribution and interaction of multiple holes and two similar holes are simulated. It can be seen from Fig. 4 (b) that when a single hole is stretched, the stress at the points on both sides perpendicular to the tensile stress is the largest and is most likely to be torn; FIG. 4 (c) shows the stress field distribution of the hole and a row of holes, and with the increase of stress, the three holes have the trend of expanding along the direction perpendicular to the tensile force and forming a tear band; FIG 4 (d) also shows that the two adjacent holes have the tendency to expand along the centerline of the two holes to form tearing ridges under the stress field and its interaction.
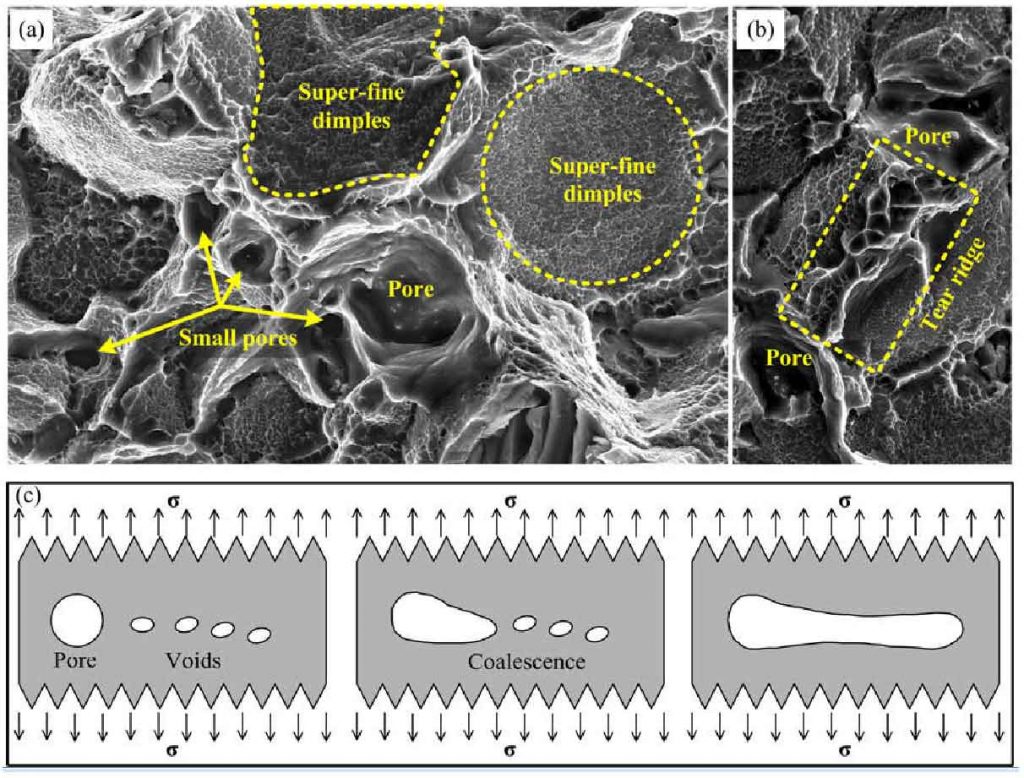
Therefore, the research on the microstructure of rheo squeeze casting alloy heat treatment, the understanding of the initial melting process, the research on the initial melting mechanism of the alloy, the finding of the law of the initial melting property, the improvement of the initial melting resistance of the alloy, the reduction and avoidance of the initial melting holes will be beneficial to improve the comprehensive mechanical properties of rheo squeeze casting alloy, and will be the focus of the next research.