1. Brushing method
Brush the clean surface to be observed with mixed lime water, and block the through-hole within the surface to be tested with putty or rubber plug. After the lime water is dry, place the part to be inspected horizontally downward, brush kerosene on the inner surface corresponding to the part to be inspected for 3-5 times, and after standing for 3 hours, observe whether there is kerosene exudation on the lime surface.
The product adopts the painting method of scheme 1 to conduct the leakage test on the box. See Figure 1 for the placement position and detection position. The ambient temperature during the detection period is below 30 ℃. The defects found in the inspection are shown in Figure 1.
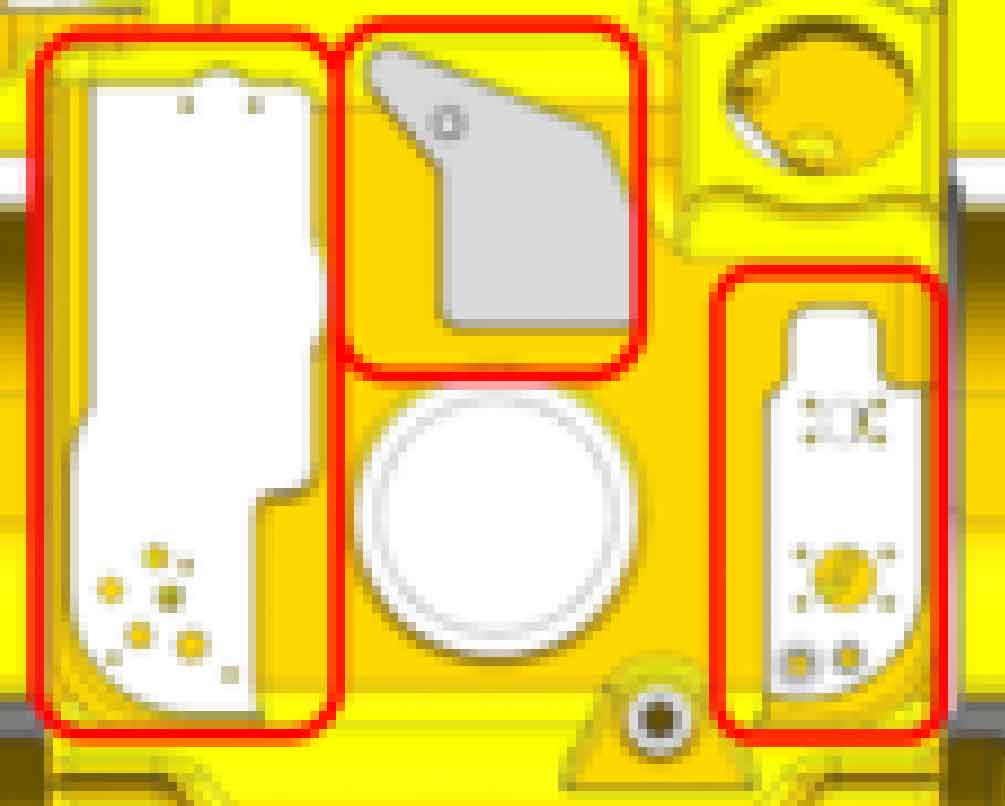
During the period from February to may 2021, scheme 1 was adopted to detect 103 castings, of which 9 were found to have kerosene leakage problems internally. However, after the castings were sent out, 6 products still had leakage problems during the client air tightness test. See Table 1 below for specific test results:
Test method | Time slot | Number of leakage found | Location of defects | Number of customer feedback | Feedback the location of the defect |
Brush coating method | 4 months | 9 | Zone 1 | 6 | Zone 1:2, Zone 2:4 |
It can be seen from the above test results that the kerosene leakage detection of this product using the above brush coating method cannot completely and effectively detect defects, and there are still some defects found during the customer’s air tightness detection.
2. Pouring method
Place the products with clean and clean surface in a proper position, and use the rubber plug with appropriate aperture to plug the through hole in turn until there is no kerosene leakage. Evenly brush the mixed lime water on the tested surface. Place the product in the direction that kerosene can be poured, and make the plane to be inspected be in a horizontal position. After the lime solution is dry and turns white, fill the inner cavity with kerosene and make it cover the area to be inspected completely. After standing for at least 12 hours, extract kerosene into the designated storage container, turn the workpiece over to the designated position, and visually detect whether there is kerosene leakage trace on the surface of lime brush.
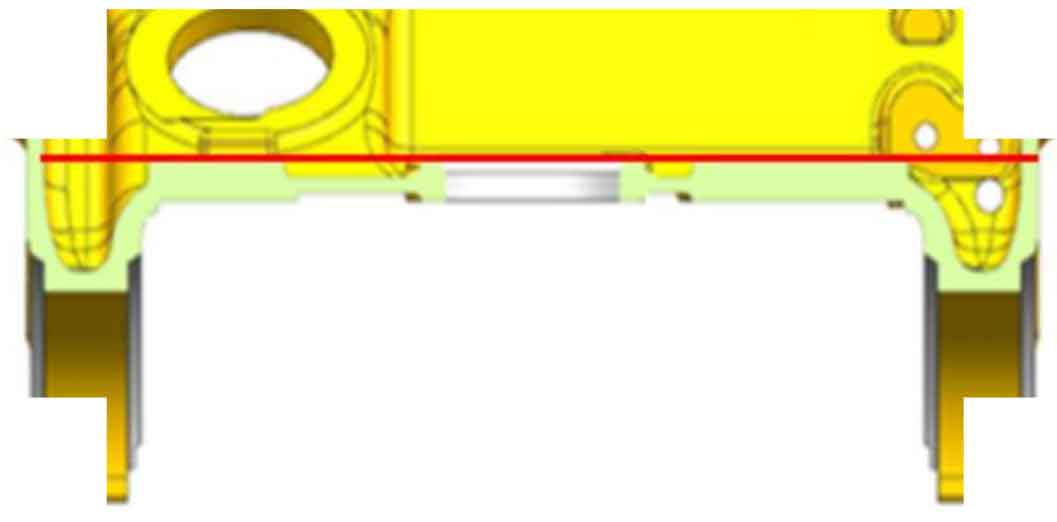
During the period from June to November 2021, kerosene injection method was used to detect the kerosene leakage of a box product. The ambient temperature was similar to the brush coating method, both of which were normal temperature and pressure. A total of 206 pieces were detected, of which 42 pieces were found to have leakage defects internally. After the defects were reworked, the problems were not fed back at the client. See Table 2 below for specific test results:
Test method | Time slot | Number of leakage found | Location of defects | Number of customer feedback | Feedback the location of the defect |
Perfusion method | 5 months | 42 | Area 1:36, Area 2:6 | 0 | / |
3. Comparison and analysis of different test methods
Using brush coating method to detect kerosene leakage of this kind of box can not effectively find the defects in area 2, and the detection effect is not as good as that of pouring method. Through further analysis and verification of the defect type in area 2, it can be seen that this defect is a hole type defect, and its volume is large, which has exceeded the size that can produce capillary effect. When brush coating method is adopted, kerosene can only penetrate into the hole surface inside the product, but cannot penetrate into the surface to be observed on the other side of the product. The filling method can provide enough kerosene to fill the internal holes, so that the kerosene in the holes can further penetrate into the surface to be observed on the other side, so that the defects can be displayed.